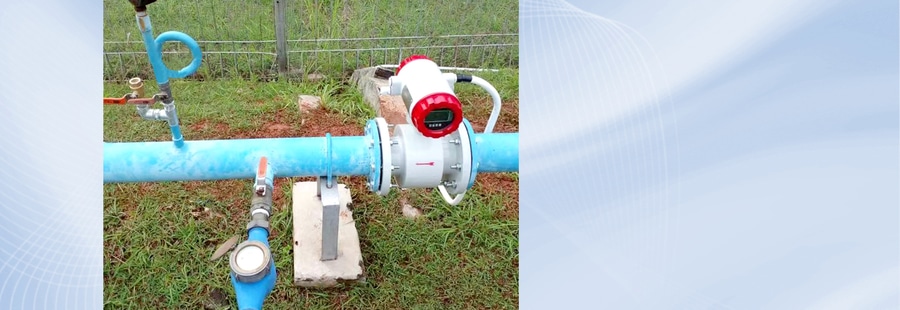
#Product Trends
How does an electromagnetic flow meter work
What are the advantages and disadvantages of electromagnetic flow meters?
Electromagnetic flow meters are commonly used in industrial and municipal applications to measure the flow rate of conductive fluids. They can handle a wide range of fluid types and flow rates, and are particularly well-suited for measuring the flow of corrosive or abrasive liquids. In this article, we'll take a closer look at how electromagnetic flow meters work, their advantages and disadvantages, how to install them, and some common applications and FAQs.
How does an electromagnetic flow meter work?
Before we know the working principle of an electromagnetic flow meter, we should know its structure. Generally, it is comprised of a transmitter, a liner, an electrode and a sensor that together measure flow. The sensor is placed inline and measures an induced voltage generated by the fluid as it flows through a pipe. The transmitter takes the voltage generated by the sensor, converts the voltage into a flow measurement and transmits that flow measurement to a control system.
What are the advantages and disadvantages of electromagnetic flow meters?
Within the context of the principles listed above, electromagnetic flow meters generally have the following features.
PROS
Unaffected by the temperature, pressure, density,or viscosity of the liquid. Able to detect liquids that include contaminants. There is no pressure loss. No moving parts (improves reliability)with less obstruction. A range of liner materials, electrode options and line sizes accommodate a wide variety of process applications
CONS
The substance being measured must be conductive. Therefore, it can’t measure gases and steam, petroleum products and similar liquids having very low conductivity. As it measures the volume rate, the volume of any suspended matter in the liquid will be included. A short section of straight pipe is required.
How to Install Electromagnetic Flow Meters?
We can adopt horizontal, inclined and vertical installation for electromagnetic flow meters. The most common installation is horizontal with the meter always being filled with liquid with the electrodes kept in the axial direction.
When the flow meter is installed horizontally or inclined, its electrode axis should be in the horizontal position.
If the medium contains solid particles or slurry, we recommend installing vertically (flow from bottom to top).
The meter should be properly grounded and have electrical contact with the liquid being processed.
Which Industries that Use Magnetic Flow Meters
There are a limitless number of industries that make use of magmeters due to their adaptability and versatility. The typicals includes:
Chemical Production
Distilleries
Water Supply
Industry Mining
Dairy
Wastewater Management
In conclusion, magnetic flow meters are specially useful in water-based use case.
FAQs
Our engineers and customer service team are happy to answer any questions you may have. Meanwhile, here are a few we answer a lot.
1.Is it safe and reliable install an electromagnetic flow meter next to one water pump?
If the flow meter is installed too close to the pump, it may be affected by the turbulence and vibrations generated by the pump, which can also affect its accuracy. Therefore, it is recommended to install the flow meter at a sufficient distance downstream from the pump to allow the flow to stabilize.
2.Can I use this to get measurement from partially filled (pressurized air and liquid) pipe?
Generally, most electromagnetic flow meters require full pipes, while with the development of technologies, now non-full pipe magnetic flow meters have been developed and used. It does not require full tubes for accurate measurement.
3.In case of more bubbles in liquid, will this flow meter work correctly?
If the bubbles in pipes are evenly distributed, it will generally not affect the measurement; however, if large air bubbles cover the entire electrode, it will cause instantaneous open circuit of the flow signal input and fluctuation of the output signal!
Problem Applications
Coating of the electrodes is a common magmeter problem. Material build-up on the inner surfaces of the meter can electrically isolate the electrodes from the process fluid. This can cause a loss of signal or a measurement error, either by changing the diameter of the flow tube or by causing span and zero shifts.
Naturally, the best solution is prevention. One preventive step is to size the meter such that, under normal flow conditions, the flowing velocity will be relatively high: at least 6-12 ft/sec, or as high as practical considering the possibility of erosion and corrosion.
Another method of prevention is to use electrodes that protrude into the flow stream to take advantage of the turbulence and washing effect. In more severe service, a mechanical cleaning system can be installed and used intermittently or continuously to eliminate coating and build-ups.
We have complete solutions for your applications, contact for professional suggestions.