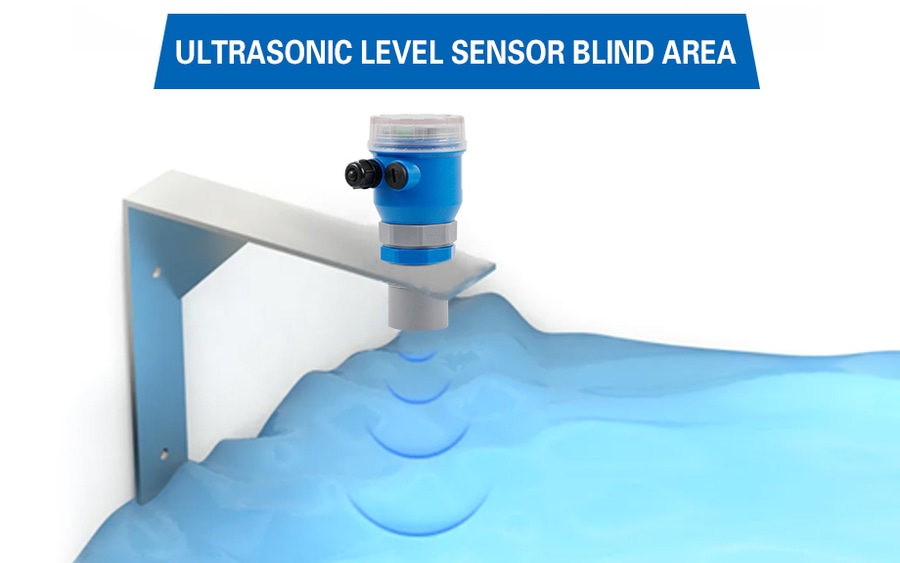
#Industry News
What is Blind Area of Ultrasonic Level Sensors?
Why Do Ultrasonic Level Meters Have Blind Areas?
Abstract
A blind zone exists directly in front of the sensor. It is the range in front of the sensor where objects cannot be reliably detected, or where an unstable output would occur.
As we may know that when we selecting or using ultrasonic level sensors, blind area is a crucial parameter. The blind area of ultrasonic level sensors varies among different products and suppliers and it affects measurement effects.
Why Do Ultrasonic Level Meters Have Blind Areas?
Ultrasonic level transmitters have blind spots caused by factors like beam divergence, reflections from surfaces, signal interference, and acoustic impedance differences in the environment being measured.
Besides, physical conditions like temperature, air pressure, and relative humidity can also exert effects on ultrasonic waves. Higher temperatures and humidity lead to greater sound wave attenuation, consequently reducing the detection area of the sensor. In situations of low relative humidity and cold temperatures, sound wave attenuation in the air decreases, resulting in an expansion of the sensor’s detection area.
What is the impact of blind area on ultrasonic liquid level measurement?
Blind area can affect ultrasonic liquid level measurement in several ways:
Inaccurate Readings: When the ultrasonic waves encounter an obstacle or surface within the blind spot, they may not return to the sensor as expected. This can lead to inaccurate readings that are either too low or too high.
Measurement Gap: The presence of blind spots creates gaps in the measurement data. This can result in an incomplete picture of the actual liquid level, especially if the blind spots are significant in size.
Limited Range: Blind spots can limit the effective measurement range of the ultrasonic level meter. In scenarios where the liquid level is within the blind spot, the sensor might not be able to provide any measurement at all.
Reliability Issues: Blind spots can introduce reliability issues in continuous monitoring applications. Sudden changes in liquid level that occur within blind spot areas might go unnoticed, leading to potential operational problems.
How We Mitigate the Negative Impact?
In industrial occasions, nearly all ultrasonic level gauges have a certain blind spot, typically around 300-500mm. To reduce the impact of blind area on the measurement, we can follow these:
1.The blind area of the ultrasonic level gauge has a relationship with its range. Generally, the greater the range is, the greater the blind area is. The smaller the range, the smaller the blind area. This can be a reference when we choosing ultrasonic level sensors.
2.When installing them, we should install properly. The highest liquid level should be beyond the blind area. If the liquid level enters the measurement blind area, adjust the ultrasonic liquid level gauge’s height accordingly.