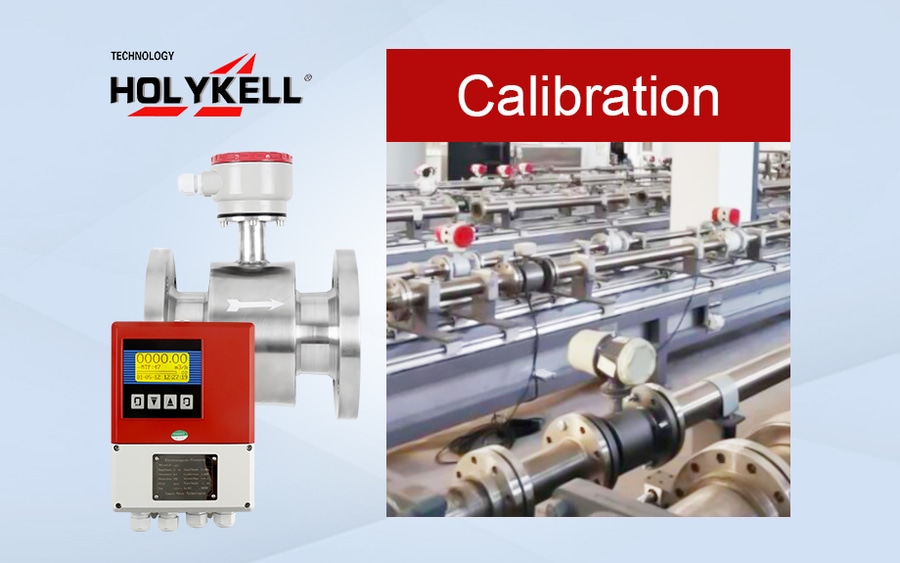
#Industry News
How to Calibrate Electromagnetic Flowmeters: A Comprehensive Guide
Calibration of electromagnetic flow meter
Calibrating electromagnetic flowmeters is essential for ensuring accurate measurement, which is crucial for various industrial applications. Over time, magnetic flowmeters can experience drift, impacting their performance.
Reasons for Flowmeter Drift
After a certain time of use, magnetic flowmeters may exhibit drift due to several factors, including:
Aging: Components may wear out over time.
Internal Surface Deposits: Accumulation of materials on internal surfaces can alter flow characteristics.
Contamination: Foreign substances can interfere with sensor function.
Severe Chemical Exposure: Harsh chemicals can damage the components.
Differences in Fluid Properties: Variations in the fluid being measured can affect readings.
External Influences: Temperature, pressure, vibration, and other environmental factors can impact accuracy.
Improper Use: Incorrect handling or installation can lead to inaccurate measurements.
All these factors can significantly alter the performance of a flowmeter, leading to inaccurate measurements. Regular maintenance and calibration are crucial to mitigate these effects and ensure continued accuracy.
This guide provides a step-by-step calibration process tailored to industry standards.
Preparation and Setup
Before calibration begins, it’s essential to prepare thoroughly:
Selecting Appropriate Equipment: Choose a pump that matches the pipeline diameter and required flow rates for verification testing.
Preheating: Once the flowmeter is installed, ensure it is powered on and allowed to preheat for at least 30 minutes according to calibration specifications.
Initial Setup
Filling with Calibration Medium: Prior to calibration, ensure the flowmeter’s sensor is filled with the calibration medium. Close downstream valves and perform zero adjustment.
Checking Overflow Signals: If using a high-level water tank, verify there are no overflow signals from the surge tank. Circulate the calibration medium within the pipeline system as per specifications, checking for leaks at all seal points.
Calibration Process
Gradual Opening of Valves: Open the valves in sequence—first the front valves, followed by slowly opening the valves at the rear of the flowmeter—to adjust the flow rate at calibration points.
Maintaining Stability: During calibration, adhere to flow measurement regulations. Ensure flow stability at each calibration point: within 1%-2% for volumetric flow method and up to 5% for totalizer method. Monitor temperature fluctuations of the calibration medium, keeping them within 1°C during identification and no more than 5°C throughout the entire process.
Post-Calibration Procedures
After completing calibration, close front valves first, followed by shutting down the pump to prevent damage to pressure stabilization devices. Drain any remaining calibration medium from the testing pipeline and subsequently shut down control systems and air compressors.
Besides, schedule periodic recalibrations as recommended by the manufacturer and take into account ambient temperature and fluid properties. Moreover, conduct training and maintain detailed records of all calibration procedures and results for compliance and reference.
Conclusion
Proper calibration of magflow meters is essential for reliable and accurate flow measurement in industrial settings. By following these calibrated steps and adhering to industry standards, you can optimize the performance of your flow measurement system, ensuring precision and reliability in your operations.
For more information on electromagnetic flowmeter calibration and our services, please contact us today.