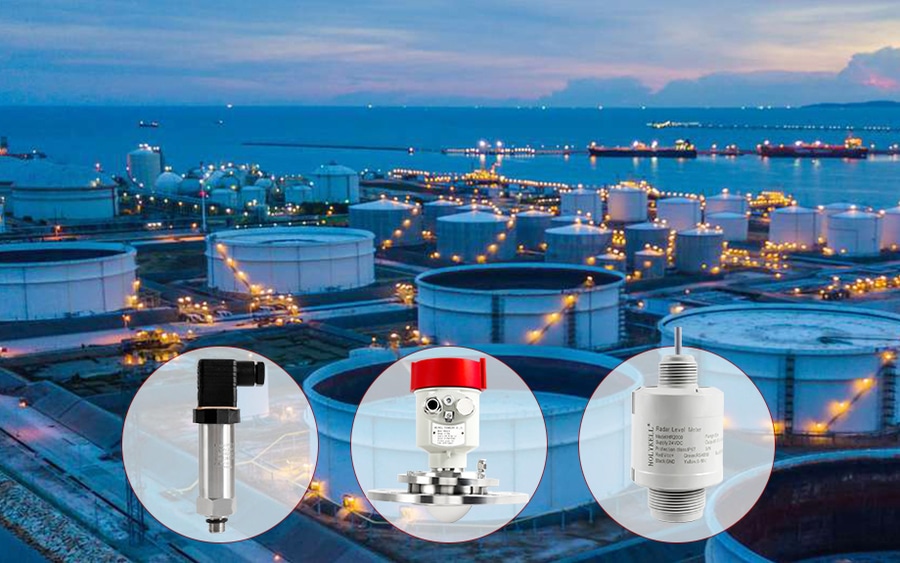
#Industry News
Comprehensive Guide to Storage Tank Types and Measuring Instrumentation
Holykell pressure level sensor
Storage tanks are extensively used in the fluid industry for storing raw materials, finished products, and intermediates. They play an irreplaceable role in ensuring safe production, energy conservation, emissions reduction, and enhancing overall management levels.
Industrial storage tanks are generally made of steel, with material choices such as carbon steel, low-temperature steel, and stainless steel based on the properties of the stored medium and storage parameters like temperature and pressure. Other materials like fiberglass and plastic are not considered due to factors such as fire resistance and pressure tolerance.
1. Types of Storage Tanks
Storage tanks can be classified based on their structure into spherical tanks, horizontal tanks, dome tanks, external floating roof tanks, and internal floating roof tanks.
1.1 Spherical Tanks
Spherical tanks are large-capacity, pressure-resistant spherical storage containers widely used in the petroleum, chemical, and metallurgical industries to store liquefied petroleum gas (LPG), liquefied natural gas (LNG), liquid oxygen, liquid ammonia, liquid nitrogen, and other media, as well as compressed gases such as air, oxygen, nitrogen, and city gas. They are used for storage at normal, low, or cryogenic temperatures and for materials with a saturated vapor pressure greater than atmospheric pressure at storage temperature.
Normal Temperature Spherical Tanks: Used for liquefied petroleum gas, nitrogen, city gas, oxygen, etc., with higher pressure depending on the saturated vapor pressure of the liquefied gas or the compressor’s outlet pressure. The design temperature is greater than -20°C.
Low Temperature Spherical Tanks: These tanks have a design temperature of -20°C or lower, typically not lower than -100°C.
Cryogenic Spherical Tanks: With a design temperature below -100°C, often stored below the liquefaction point of the medium. They have low pressure, sometimes atmospheric, and require high insulation, often using a double-layer spherical shell.
1.2 Horizontal Tanks
Horizontal tanks have a smaller volume (generally less than 100 m³) and occupy a larger area. They are primarily used for storing chemicals such as acids and bases, and for small-capacity storage of other media within production facilities. The tank body is parallel to the ground and typically supported by saddle supports. They are pressure vessels that can withstand higher positive and negative pressures.
1.3 Dome Tanks
Dome tanks have a spherical crown top and cylindrical body. They are simple to manufacture and cost-effective, widely used in various industries. The most common volumes range from 1,000 to 10,000 m³, with the largest dome tank in China reaching 30,000 m³. Dome tanks are generally low-pressure or atmospheric storage tanks used for storing Class IIB and Class III liquids and, in some cases, Class IB and Class IIA liquids with specific storage requirements.
1.4 Floating Roof Tanks
Floating roof tanks consist of a floating roof that rests on the surface of the stored medium and a vertical cylindrical tank wall. The floating roof rises and falls with the storage level, reducing evaporation. They are used for storing Class IB and Class IIA liquids with saturated vapor pressure lower than atmospheric pressure. There are two types of floating roof tanks: external and internal.
External Floating Roof Tanks: Typically used for storing volatile petroleum products like crude oil, gasoline, or kerosene. They reduce evaporation losses and environmental pollution and decrease the risk of explosive gas formation.
Internal Floating Roof Tanks: Combine features of dome and floating roof tanks. They have a fixed dome outside and a floating roof inside, providing advantages such as preventing contamination from external elements, reducing evaporation losses by 85%-96%, and lowering fire and explosion risks. They are suitable for storing high-grade gasoline, jet fuel, and toxic petrochemical products.
2. Tank Farm Classification
In the fluid industry, storage tanks are typically arranged in tank farms based on their usage or pressure levels.
By Medium and Pressure Levels: Classified into atmospheric tank farms, spherical tank farms, acid and alkali tank farms, and cryogenic tank farms.
By Usage: Divided into raw material tank farms, intermediate tank farms, and finished product tank farms.
Each tank farm is further subdivided into different tank groups based on tank types, medium properties, pressure levels, and safety requirements.
3. Common Measuring Instruments in Tank Farms and Storage
Storage tanks are essential in the fluid industry, and we generally measure their parameters such as liquid level, temperature, density, and pressure (for pressurized tanks) to calculate storage volume and mass, and control inlet and outlet valves and flow rates.They can be classified into intermediate tanks and trade tanks.
Intermediate Tanks: Monitored the level, temperature, and pressure to prevent accidents like tank overflow or vacuum formation.
Trade Tanks: High precision monitoring and measurement of level, temperature, density, volume, and mass are required for trade accuracy.
How to Select the Right Measuring Instrumentation?
Instrument selection should be based on environmental conditions, tank type, maintenance and operation cycles, and lifecycle costs to ensure optimal performance and cost-effectiveness.
Contact our sales engineer for right selection here.
3.1. Level Instruments
Accurate level measurement is crucial for monitoring and calculating stored volume, and, if necessary, density compensation to determine storage mass.
3.1.1 Radar Level Transmitters
Radar level transmitters are non-contact instruments with no moving parts, providing reliable operation, especially suitable for high viscosity and highly corrosive media. They are ideal for large tanks, high-temperature, high-viscosity, and highly corrosive environments, offering high accuracy and fast response times. When installing, consider tank type, medium properties (dielectric constant, volatility, boiling, steam, dust, adhesion), and operating parameters (temperature, pressure, etc.).
3.1.2 External Ultrasonic Level Meters
External ultrasonic level meters consist of a main unit, probe, and metal structure, used for measuring liquid levels in rail tank cars, road tankers, and various storage tanks. They measure liquid level by transmitting ultrasonic waves through the tank wall and liquid, receiving echo signals from the liquid surface. They are ideal for high and low-level supplementary measurements without requiring tank penetration.
3.1.3 Magnetostrictive Level Meters
Magnetostrictive level meters feature high accuracy, installed on the top or side of the tank. They measure liquid levels using magnetic pulse waves. The float with a permanent magnet moves along the rod with the liquid level, creating a magnetic field that interacts with the pulse wave to generate a return pulse, indicating the level change. This type of level sensors are easy to install with little maintenance.
3.1.4 Capacitive and RF Admittance Level Meters
Capacitive level meters measure liquid levels based on changes in capacitance between electrodes and the conductive tank wall. They require stable dielectric constants in the measured medium.
Due to the tendency of capacitive electrodes to accumulate material during use, which generates additional capacitance and resistance directly affecting the performance of capacitive level meters, RF admittance level meters overcome this issue by using compensation technologies, available in rod, coaxial, cable, and heavy-duty cable forms, with various output signals and connection sizes.
3.1.5 Differential Pressure Level Transmitters
Differential pressure level measurement uses transmitters like blowdown, standard, single-flange, double-flange, and insertion flange transmitters based on specific conditions. Different types are suitable for specific applications.
4. Pressure Instruments
Pressure measurement in storage tanks is straightforward. Spherical tanks or pressurized dome tanks need pressure alarms or interlocks. Micro-positive pressure dome tanks or internal floating roof tanks generally require pressure measurement for nitrogen sealing. Industrial pressure transmitters are commonly used.
5. Flow Instruments
Flow instruments are generally not required in tank farms unless for metering purposes. Common instruments include mass flow meters and volumetric flow meters. Utility metering can use vortex flow meters or differential pressure devices with temperature and pressure compensation if needed.
By using these right instrumentation and following best practices in installation and maintenance, tank farms can achieve optimal automation and efficiency in storage operations.
Holykell has rich experience in this industrial automation. Reach out to us for more technical information.