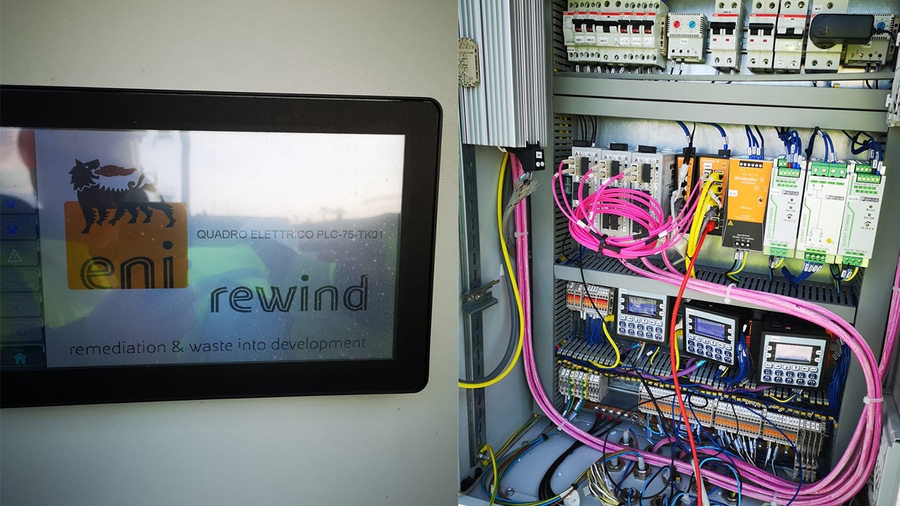
#Industry News
Horner Solution for Oil and Gas “Remediation & Waste into development” in Italy
This project involved a Groundwater Pumping well in a land reclamation system for Oil and Gas application in Italy. There was a 6-month implementation of this project.
Horner Solution for Oil and Gas “Remediation & Waste into development” in Italy
This project involved a Groundwater Pumping well in a land reclamation system for Oil and Gas application in Italy. There was a 6-month implementation of this project.
Project Requirements
Requirements of this project included 6 Electrical cabinets for wells management in different locations, each cabinet with 2 CPUs High availability (Not HW redundant) and small I/O count with analog In/Out.
There were important regulatory requirements to be met with this project including Oil & Gas application with Divisions 1 and 2 Hazardous (Classified) Locations.
The project also had 4.0 requirements including the 6 locations to be connected on fibre optic based Ethernet, to each other and to a central management facility with Scada system for data logging and remote Auto/Man operation.
Moreover, the main Well and pumping station had priority over the other 5 stations and must stop all of them in case of high-high water level in its tank.
Each one of the six wells had the following layout:
1 10” HMI connected to the 2 CPUs on ModBus TCP
1 Master CPU
1 Slave CPU
less than 10 Digital IN
less than 10 Digital Out
max 3 Analog In
max 2 Analog Out
Every Cabinet had a local switch to connect the 2 CPUs and the HMI and to the next switch on fibre optic.
Upon the customer’s request one of the systems was used to collect all data from each well and make them available to a remote Scada.
The main cabinet had 2 frequency drives to regulate the pump speed either in steps or in frequency using analog outputs and receiving the actual frequency with analog inputs.
The Horner Solution
Horner Products used included:
1 HE-X10A used as HMI connected to the 2 CPUs on ModBus TCP
2 HEXE221C100 as Master CPU and Slave CPU
1 HEXE220C116 or 1 HEXE220113 used as remote IO, connected to the 2 CPUs on CsCAN network
Reasons for the choice of HW:
Cost for the X10 Micro, the XLEe and the XLE used as remote IO
No requirement for Hazardous zone on the HMI.
Key point in using the XLEE/XLE was the hazardous zone classification
For all product the other key point was the availability.
Most valuable features of the Horner Technology included:
Fast communications on CsCAN Network and ModBus TCP communication on the units with Ethernet port.
The Horner controllers were most useful for fulfilling all requirements at an acceptable cost and
The possibility to install the XLEe/XLE on a DIN rail inside the cabinet was also an advantage.
Supporting Distributor
For more information, please contact this project’s supporting distributor:
Contact: Enrico Guasco
Tex-El Automazione & Robotica Srl ,
Via Mulini 1,
Candelo (Bi) -13878
Italy.
Mob: +39 393 934 0024
Email: enrico.guasco@horner-apg.com
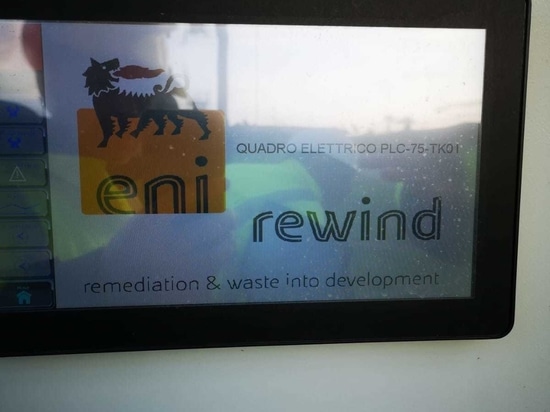
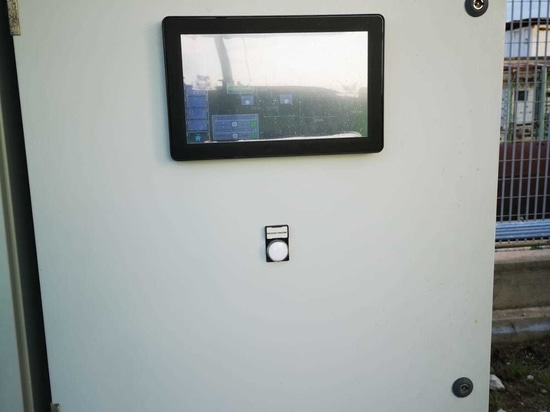
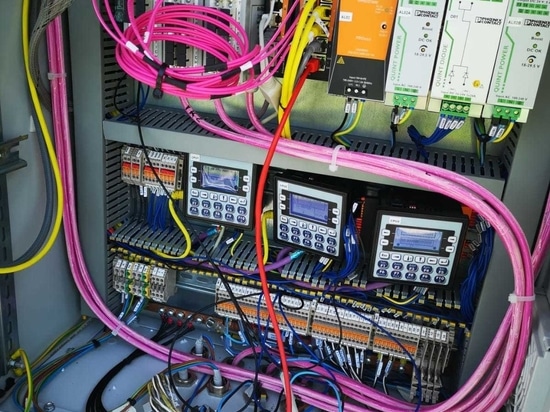