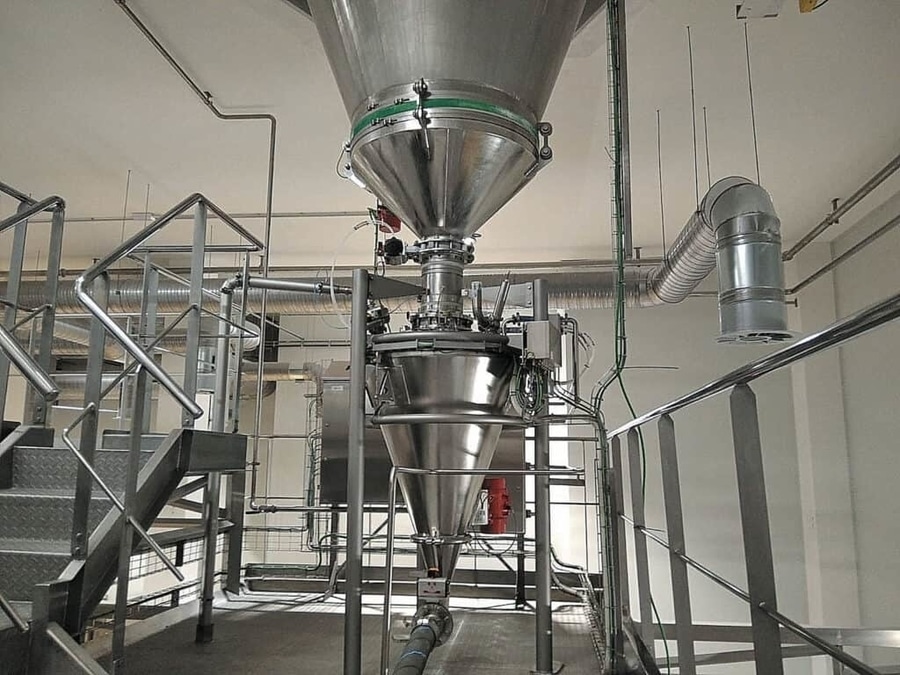
#Industry News
Hygienic Pneumatic Conveying of Milk Powders
Food industry comes up with the most quality equipment’s on their processes, especially milk protein industries are investing the most in manufacturing with the most quality technologies.
This is a case study for a new factory we have been commissioned to design and develop with the highest technology and for safety controls and cleaning processes.
The peculiarity of these systems comes not only by the extract requirements but also by the complexity of the products to be managed which are described as middle–bad fluidity. After analyzing the material for different powders we’ve come up with a Hausner index of 1.28-1.35.
In addition, we have done the analysis under the Geldart index which measures the fluidization and air retention capacity, and come up that the different products oscillate between products of type A and B and we place it specifically in zone 3 (for this we have considered a particle density of around 1500 kg/m3 and an average particle size of 200 µ).
Analysis of bulk solids
First and foremost, an analysis of the bulk goods to be conveyed is required in order to choose the appropriate procedures/systems and components
Geldart divides the bulk cargos according to their fluidization behavior and air retention into groups A, B, C, D, providing a rough classification of the conveying characteristics
A fine-grained powder with low density, easily fluidized with good air retention
B medium granulation with medium density, some fluidization properties with poor air retention
C fine powders with higher density, cohesive, poor fluidization properties with poor air retention
D larger granulation with higher density, no fluidization properties, no air retention
This is the reason why to maintain the integrity of the particle as much as possible and to carefully transport the products, a dense phase pressure conveying system by a push conveying process with high load and slow conveying speed is chosen for this commissioned project.
Chosen conveying system
solids Vibro Puls Pneu Plug conveying with bypass, impulse valve and relay stations Pressure conveying system
Patented pneumatical plug conveying solids PULS PNEU
In 1970 H.J. Linder’s German patent DE-PS 2-122858 described a complete procedure for pneumatical plug conveying for the first time. It features an impulse valve that forms plugs and a second feed line with so-called relay stations to maintain the plugs and continue their transport without dispersing them.
For about 40 years the solids solutions group has planned and built over 1000 systems based on this patent for thousands of different products in all European countries, the USA, Japan, and India.
The innovative and key characteristics were and still are
virtually infinite conveying methods and capacities
no blockage at slow speeds and large loading (µ = kg material/kg air, gas)
slow, gentle conveying from approximately 0,5 m/sec
almost nonwearing – even for extremely firm and abrasive bulk solids e.g. silicon carbide or grinding material
hardly any grain destruction and minimal abrasion of supersensitive products e.g. spray granulate
no decomposition with mixtures and processed masses
low energy costs due to an efficient use of the pressure energy
reliable operating procedures even with damp, cohesive, sticky or poorly flowing bulk goods
Vibro-Pulsor Neumático PIVS-Hygienic-Dry for top hygienic systems.
Operation purpose: Pneumatic pressure conveying vessel with complete facilities. The discontinuous operation, filling with bulk solid when the inlet valve is open under atmospheric conditions. Then locking pressure-tight and discharging the bulk solid and conveying with compressed air into the connected pipeline.
Operating conditions: Permissible operating pressure: 3 barg, Product temperature max: 70° C Max./Min. ambient temperature: -10 °C ≤ T ≤ 50 °C Bulk solids data: Powdered till granulates, up to middle hardness, from free-flowing up to non-flowing products.
This one in the picture is a HYGIENIC pneumatic impeller that has been designed with an internal roughness <= 0.8 microns.
Consisting of:
1. Connection for Butterfly valve for loading and closing the pulsator.
2. Pressure vessel:
– Volume: 450 usable liters
– Material: stainless steel AISI-304L
– Maximum working pressure: 6 bar.
– Maximum temperature: 100°C
– DN-100 manhole.
It comes with outlet elbow, supporting legs, connection for Safety valve s/97/23/EG, de-aeration system, connection for Pressure transducer, and electro-pneumatic panel. ATEX 22.
In this project, we have provided a total of 3 units of our Hygienic-Wet Design according to EHEDG-Guidelines with high hygienic requirements and wet cleaning. As per is a total of three towers to fulfill the production requirements