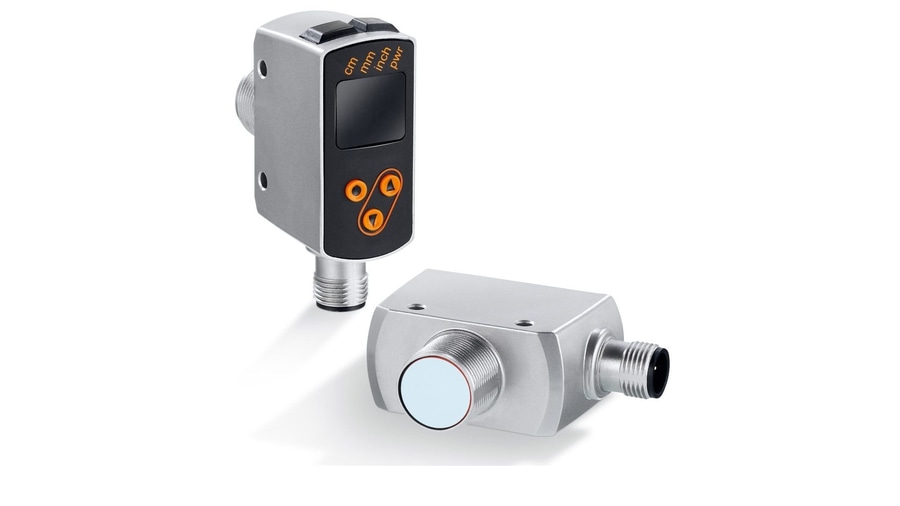
#Product Trends
Distance sensors: advantages of time-of-flight measurement compared to triangulation
PMD sensors allow for more flexible positioning and provide more reliable measurement results
Proven effective in numerous customer applications, our OGD distance sensors with Photonic Mixer Device (PMD) technology are highly versatile problem-solvers for the most challenging tasks. Thanks to the combination of time-of-flight measurement (ToF), background suppression and evaluation of the reflectance, the OGD distance sensors continue to provide stable and precise results where conventional triangulation sensors would fail. In applications with multi-coloured, low-reflectance or shiny surfaces, the OGD sensors detect objects safely – even at extreme alignment angles. A background suppression function ensures maximum reliability even if the sensors are exposed to movements, reflections or poor lighting conditions. The sensors detect dirt on the lens through the reflectance value and alert the operator about cleaning. This increases process reliability.
Advantages of PMD distance sensors:
- detect reflective and light-absorbing objects
- detect multi-coloured objects
- detect objects from oblique detection angles
- detect objects despite background reflections and movements
PMD sensors for quality inspection and conveyor belt control
The OGD Long-Range is typically used in conveying, packaging, food processing, metal working and mechanical engineering applications. Based on the reflectance value, it can, for example, perform quality checks of transparent adhesive tapes or seals of different colours. In material handling, conveyor belt stop functions can be implemented using several switching points and an initial speed reduction. Moreover, objects can be evaluated in terms of quality and product size.
PMD sensors for precise detection of small parts
The OGD Precision is typically used in error proofing, robotics and handling applications, where it performs precise and reliable inline quality checks and monitors the correct position, orientation and quality of small shiny or black components such as O-rings or toothed wheels. Assembly errors can be detected during production, i.e., before the final quality checks, thus minimising the risk of costly consequential damage such as plant downtimes or batch failures. In the fully automated production of electronic devices, detecting objects from different angles is essential. This can be achieved with the OGD.
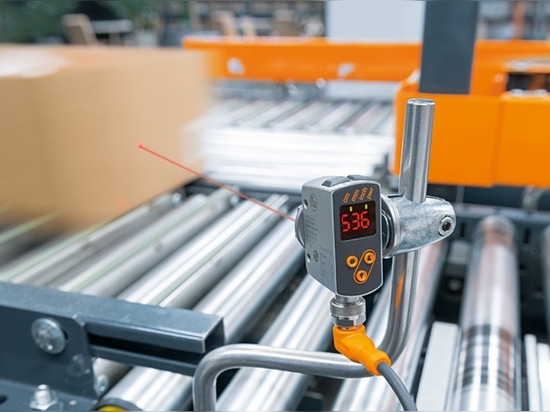
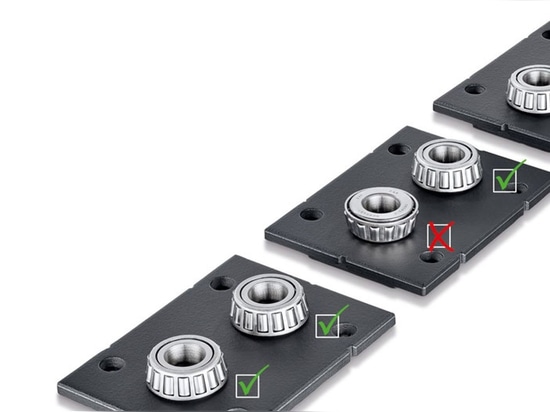
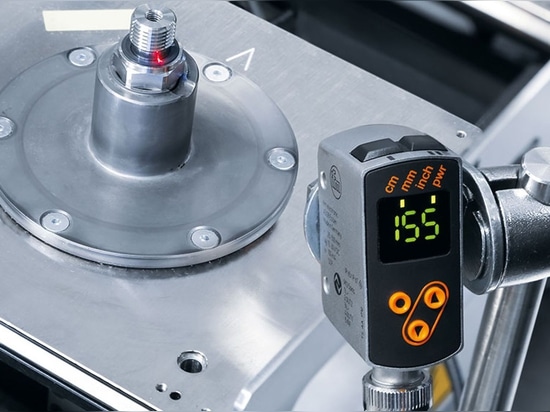