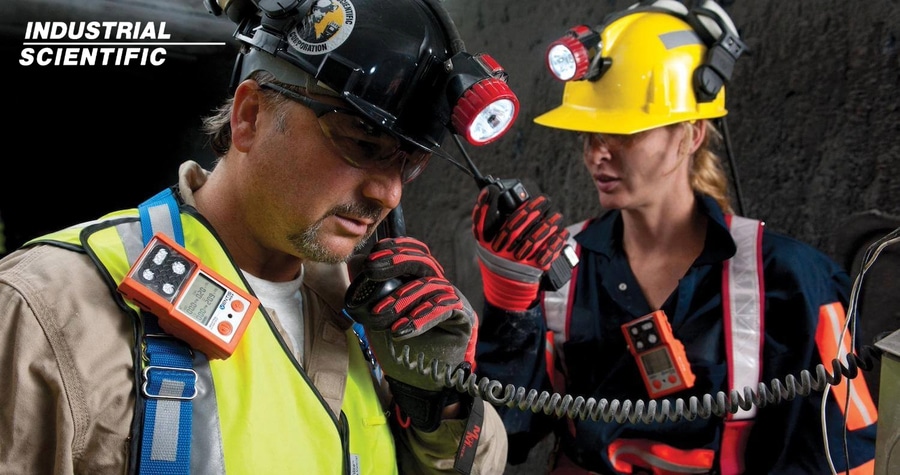
#White Papers
Mining company reduces fleet turnover
Read the case study to know the full story.
Managing gas detectors and ensuring worker accountability in mining operations can be a daunting task. With large fleets, dangerous conditions, and unique connectivity challenges underground, it is crucial to develop a safety program that works to protect your team.
Our recent case study highlights how a large underground mineral mining company in Canada tackled these challenges and successfully improved their safety procedures.
The safety management team implemented a creative combination of solutions to:
- Monitor gas exposure incidents and ensure adherence to safety procedures
- Improve worker accountability by tracking individual gas detector usage
- Reduce fleet turnover and prevent the loss of valuable equipment
- Save time and resources by minimizing the need to replace lost monitors
Read the case study now to discover how you can manage your fleet of gas detectors while ensuring worker accountability and improving safety.