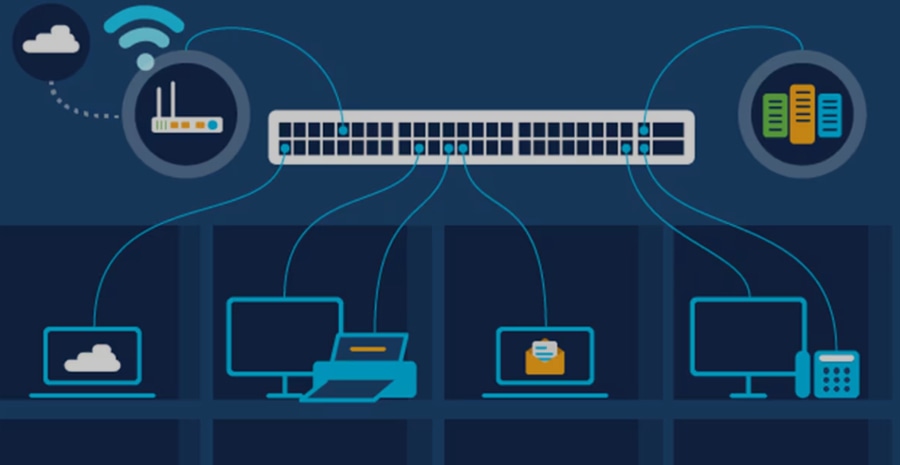
#Industry News
What is Ethernet?
Ethernet is a networking technology that was first proposed in the 1970s and later standardized as IEEE 802.3 in 1983.
Ethernet is a networking technology that was first proposed in the 1970s and later standardized as IEEE 802.3 in 1983. Defined by the Institute of Electrical and Electronics Engineers (IEEE), this standard specifies the physical and data link layers of Ethernet. Ethernet enables computers and devices to connect and communicate within local area networks (LANs) and wide area networks (WANs).
The primary function of Ethernet is to allow devices connected to the network to exchange data. Imagine a scenario where many people are talking at the same time; The conversations would be chaotic and difficult to follow. Similarly, data packets transmitted simultaneously over a shared Ethernet cable can collide and create confusion. Ethernet protocols manage data transmission rules to avoid such conflicts, ensuring regular and efficient communication.
What is Industrial Ethernet?
Industrial Ethernet is a specialized form of Ethernet designed to meet the demanding demands of industrial environments. Specially designed for automation and control systems in production, it has emerged as the leading network technology on factory floors worldwide.
Requirements such as real-time communication, low latency, and deterministic data routing are crucial in industrial environments. Industrial Ethernet uses specially developed protocols to succeed in these harsh environments. There are about 20 industrial Ethernet protocols, but five of the most common are EtherCAT, EtherNet/IP, PROFINET, Modbus TCP/IP, and POWERLINK.
5 Common Industrial Ethernet Protocols
1. EtherCAT
EtherCAT, which stands for Ethernet for Control Automation Technology, was launched by Beckhoff in 2003. It uses the master-slave architecture and is notable for its "on-the-fly processing" capability. Each node (slave device) unpacks the relevant data and transmits it simultaneously; Thus, efficiency and speed increase significantly.
2. EtherNet/IP
Supported by the Open Device Vendors Association (ODVA) and adopted by Rockwell Automation, EtherNet/IP is based entirely on the Ethernet protocol. It uses the Common Industrial Protocol (CIP) for universal industrial automation services. EtherNet/IP supports an unlimited number of nodes due to being connected to standard Ethernet and switches, but its real-time communication capabilities are somewhat limited.
3. PROFINET
Developed in the early 2000s by members of Siemens and Profibus, PROFINET is a common industrial Ethernet solution. It has three classes: CC-A (basic real-time), CC-B (adds support for Simple Network Management Protocol), and CC-C (PROFINET IRT, which offers real-time data changes with cycle times of less than 1 ms). PROFINET is versatile and suitable for a variety of automation tasks, from work systems to motion control.
4. Modbus TCP/IP
Modbus was developed from the Modbus RTU fieldbus, combining TCP/IP, Ethernet, TCP/IP standards and Modbus data transmission methods. It works in the master-slave (client-server) model, where only the master device can initiate queries. Although widely used, Modbus TCP/IP is not designed for real-time communication.
5. POWERLINK
Developed by B&R, POWERLINK is a real-time industrial Ethernet protocol that complies with IEEE 802.3. Flexible network topology offers hot-plugging and cross-connect capabilities. By using polling and time zone methods, it supports various industrial automation components, allowing only one node to transmit data at a time.
Industrial vs. Commercial Ethernet
While commercial Ethernet is ubiquitous in homes and offices, industrial Ethernet has distinct differences that are tailored to industrial needs.
- Standards and Protocols: Commercial Ethernet generally uses the IEEE 802.3 standard. In contrast, industrial Ethernet relies on specialized protocols such as EtherNet/IP, EtherCAT, and others to meet industrial requirements.
- Network Speed: Industrial Ethernet typically operates at slower speeds compared to commercial Ethernet. This is because industrial networks prioritize control and automation data over high-speed data transfer.
- Stability, Reliability, and Safety: Industrial Ethernet components are designed to withstand harsh conditions such as dust, chemicals, vibration, extreme temperatures, and electromagnetic interference. This robustness contrasts with commercial Ethernet, which often cannot withstand such environments.
- Real-Time Communication: Unlike commercial Ethernet, industrial Ethernet must enable real-time data distribution. This is crucial for applications such as automation and control systems, where data must be transmitted at precise time intervals for accurate control.
Imagine Industrial Ethernet as the invisible force behind various industrial processes. It plays a vital role in factory automation, control systems, robotics, transportation, and even the oil and gas industry. This technology integrates seamlessly with Industry 4.0, enabling efficient data transmission and connectivity for advanced automation. With its robust design and increased compatibility, industrial Ethernet is poised for continuous development in the future as well.