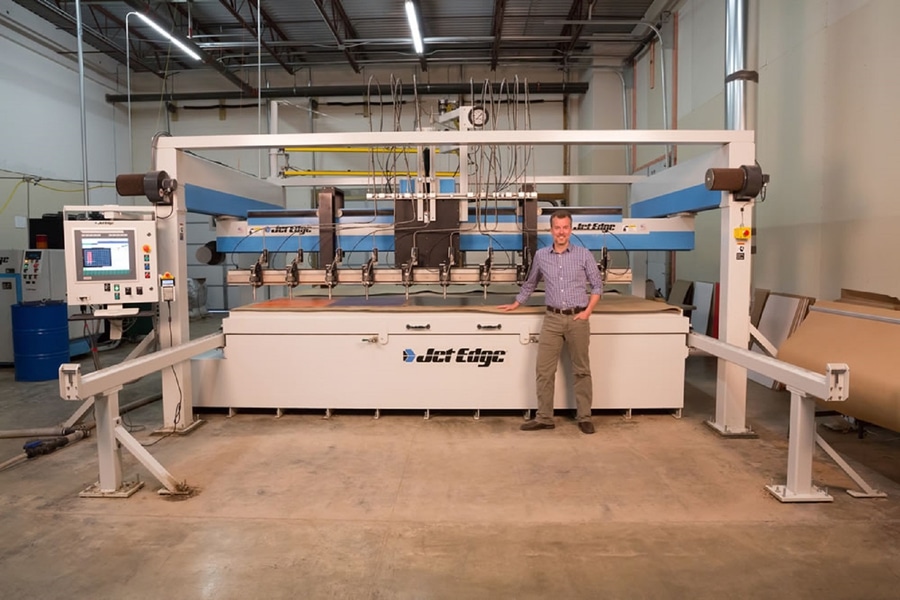
#Industry News
Toymaker YOXO® Doubles Productivity with Jet Edge Waterjet Shuttle System
Shuttle Allows Waterjet Operator to Keep Cutting While Unloading Finished Parts
ST. PAUL, Minn. – (June 2, 2016) – Rapidly growing toy manufacturer YOXO® recently installed a second Jet Edge waterjet cutting system to meet skyrocketing demand for its creative toy construction kits.
Designed to fuel kids’ creativity, YOXO (“yock-so”) kits inspire kids to design and build their own toys using Y, O, and X-shaped links that connect with everyday household items such as toilet paper tubes, paper towel rolls and cereal boxes. YOXO links also can be attached to other connector toys like LEGO®, KRE-O® and Mega Bloks®.
YOXO’s “eco-awesome” toys are made in the company’s wind-powered workshop in St. Paul, Minnesota, where the links are waterjet cut from colorful sheets of locally sourced recycled wood fiber. A truly closed-loop sustainable toy, YOXO can be recycled when kids are done playing with them and made into new YOXO.
When YOXO Founder and CEO Jeff Freeland Nelson launched his innovative toy company in 2011, he wanted to do something different that would encourage kids to use their imaginations. With the encouragement of his wife Alisa Blackwood, he set an ambitious goal for YOXO to be the most sustainable toy manufacturer in the world.
“Most toys are made from plastic on the other side of the planet, and will eventually end up in a landfill,” he said. “We decided to do it differently. We wanted to make a product from sustainable, recycled and recyclable material, and we wanted to manufacture it in the U.S.A.”
Initially, YOXO cut its connectors using laser cutters, but the lasers burnt the edges of the material, forcing the YOXO team to spend hours cleaning parts. Buying multiple lasers to increase production would have been cost prohibitive.
“Parents don’t want their kids playing with sooty toys, so we needed a better solution,” Freeland Nelson recalled.
With contracts then in negotiation with Target and Barnes & Noble, YOXO sought a more productive way to cut its parts. The company tested a variety of cutting technologies before concluding that cutting its water-adverse material with 55,000 psi jets of water was, oddly enough, the most effective solution. They turned to Jet Edge in nearby St. Michael, Minnesota, and worked very closely with the waterjet manufacturer’s engineering and sales staff to custom engineer a solution for their unique application, taking delivery of their first waterjet system in late 2014.
The results were immediately noticeable, recalled Trevor Burns, YOXO’s director of production.
“We saw a 15-20 percent productivity gain without sacrificing any of the quality of our products after switching from laser to waterjet. These are remarkable gains to be made from switching manufacturing methods completely.”
A year after installing their first Jet Edge, YOXO, growing by leaps and bounds, needed a second system.
“The second waterjet was a no brainer,” Burns noted. “We needed the production capacity, redundancy, and efficiency. The investment in another waterjet has more than doubled our production output quickly, with an increase in quality of our product.”
For their second waterjet system, YOXO decided to take production goals a step further by installing a high production Jet Edge High Rail Gantry Waterjet Shuttle System with 10 OmniJet® waterjet cutting heads. The custom-engineered shuttle system maximizes productivity by allowing YOXO’s operators to continue cutting as parts are unloaded.
“This upgrade was done due to the observations that our longest loss of production time was caused from the loading and unloading of our table,” Burns explained. “With the shuttle, this time is down from 10-20 minutes to 1-2 minutes, a huge leap in productivity for our process.”
The new system also features a custom slanted tank with blow down system, a feature YOXO also had retrofitted to its first waterjet. The slanted tank makes it easier to clean out pulp debris, while the blow down system helps hold the material in place during the cutting process.
“This has drastically cut down on tank cleaning and increased the quality of our cuts by almost completely eliminating "splash-back" onto our products,” Burns said.
Burns and Freeland Nelson said they have been very satisfied with Jet Edge’s equipment, service and support.
“Jet Edge has been more of a partner than we ever anticipated in helping to build our brand and increase our production capabilities to the level of a successful manufacturer of eco-awesome YOXO toys,” Burns said. “In all aspects, Jet Edge has been there to answer questions, work to solve issues, and deliver parts in a quick reliable way. The hands-on treatment from Ben Callahan, Jet Edge salesman extraordinaire, has from the start allowed us to build a system to fit our needs and budget, and our Jet Edge technician is always available for quick answers and reliable onsite repairs. Jet Edge waterjets are not the cheapest systems out there, but the investment in a greater up front cost more than makes up for itself in the reliability of the waterjet, the service capabilities of Jet Edge, and the reliability of the necessary consumable parts Jet Edge’s parts department has in stock.
With its waterjets running an average of 100 hours a week, YOXO goes through a fair amount of consumable waterjet parts. Burns said he tried to save money with knockoff parts, but quickly switched back to genuine Jet Edge parts.
“There is no comparing,” he said. “After that experiment I have no problem paying more for parts that last two to three times longer. Jet Edge makes the best consumable parts by far. They are better designed and more reliable than any other company's parts that we have tried. You get what you pay for, and they pay for themselves quickly.”
Burns added that YOXO’s Jet Edge waterjet equipment has been very reliable and is easy to operate and maintain.
“The pumps are almost indestructible,” he said. “Waterjets by their nature take a higher level of maintenance than some modes of production. However, by in large, the maintenance itself is quick and well described by the manuals and Jet Edge training program. Our ‘off the street’ operators with no prior experience were quickly able to perform the necessary daily and preventive maintenance requirements to an adequate level. We have used inexperienced operators from the get go. After the install training we were ready to begin full production within days. And with the second machine, we were ready within hours of the final installation testing.”
“Jet Edge has been a wonderful partner,” Freeland Nelson said. “They were the only manufacturer that was willing to work with us to design and test a system that met our needs. Their parts and service department is outstanding, and Jet Edge continues to support us in getting the word out about YOXO. Their willingness to sponsor and help staff our busy Minnesota State Fair exhibit went above and beyond in assisting with brand building and the ‘normal’ experience that companies have with equipment providers. They are even supporting our West Coast Tour with PBS Kids this summer.”
YOXO is so proud of their waterjet systems, they’ve even given them names: Bennie I and Bennie II, after the Elton John song, “Bennie and the Jets.” Every YOXO kit features Jet Edge’s logo and explains how the parts are made with water. YOXO also has installed a window to the waterjet room so kids can see how YOXO are made while visiting the workshop for its popular Play Dates.
Look for YOXO construction kits at select Target and Barnes & Noble stores, Amazon.com, Creative Kidstuff and other specialty retailers. For more information, visit www.yoxo.com.
About Jet Edge, Inc.
Established in 1984, Jet Edge is a global designer and manufacturer of waterjet systems for precision cutting, mobile cutting, surface preparation and coating removal. Jet Edge waterjets are used around the world in a broad range of industries, from the world's leading airlines to automotive, aerospace, industrial manufacturers, machine and job shops. Jet Edge waterjet systems are proudly made in the U.S.A. For more information about Jet Edge, visit www.jetedge.com, e-mail sales@jetedge.com or call 1-800-JET-EDGE (538-3343). Follow us on Twitter @jetedge.
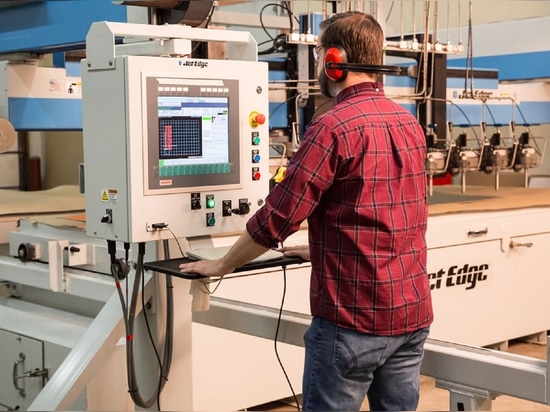
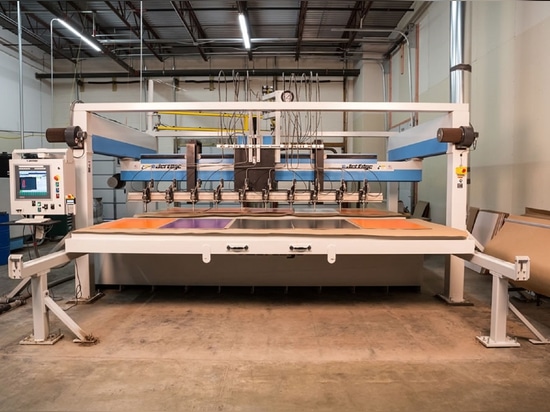
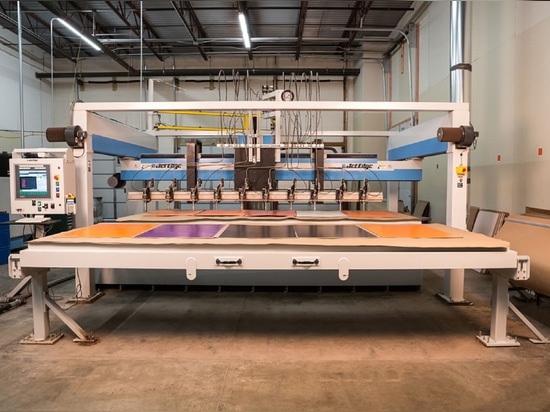

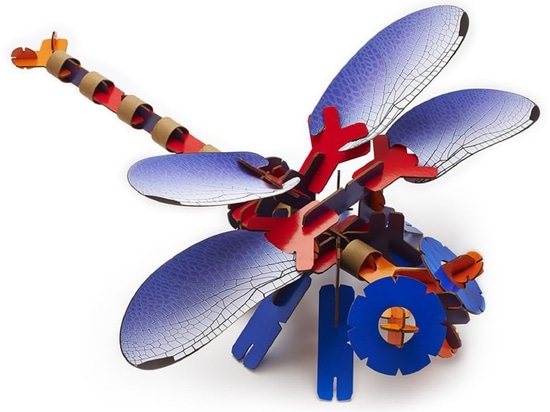