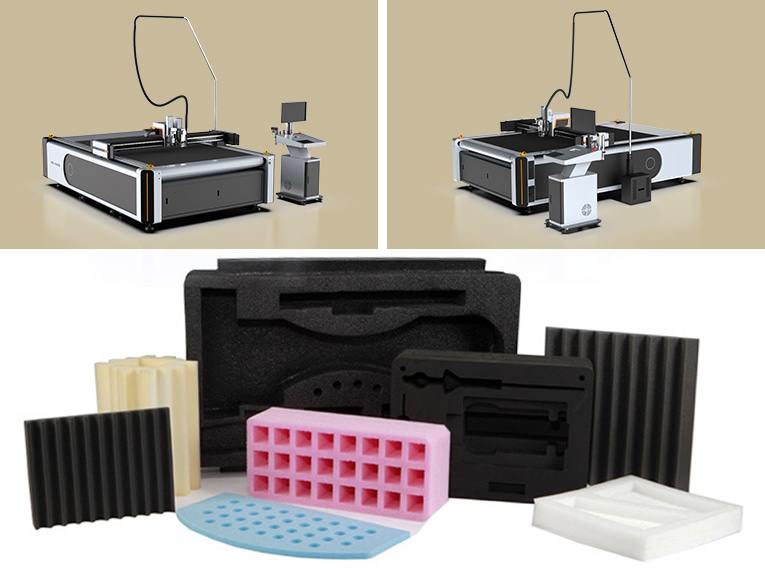
#Industry News
process EVA foam efficiently with a vibrating knife cutting machine
How to process customized EVA foam packaging materials efficiently with a vibrating knife cutting machine
How a CNC cutting machine for cutting EVA material works:
Oscillating knife cutters use a fast-moving blade to precisely cut through materials. Let's break down the tools we use.
Pneumatic Oscillating Tool: Great for cutting EPE foam and low-density EVA foam. It uses compressed air to drive the blade for fast, precise cuts.
Milling Tool: Great for carving and milling EVA and EPE foam. It's great for fine work and creating complex shapes.
Electric Oscillating Tool: Great for cutting high-density EVA foam. It uses an electric motor to drive the blade, providing more power for tougher materials. Each tool has a specific purpose, ensuring you get the best cut for each foam.
What you need before cutting:
Before you start cutting, proper preparation is key:
Design your package: Create a detailed plan using design software. This should include the size and shape of your foam inserts.
Plan your cutting path: Plan your cutting path effectively to minimize waste and reduce cutting time.
Material Preparation: Make sure your EVA foam sheets are clean and flat. Secure them properly to prevent movement during cutting.
Operating steps of oscillating knife cutting machine:
Tool selection and installation: Select the appropriate tool according to the foam density and install the tool firmly in the machine.
Set cutting parameters: Adjust speed, vibration frequency and cutting depth according to the foam type. For example, for high-density EVA foam, use higher speed and frequency.
Optimize cutting path: Plan the cutting path to minimize waste. Use nesting software to effectively arrange the design on the foam board.
About quality control and inspection of CNC cutting machine
It is essential to ensure high-quality cutting and consistency:
Check cutting accuracy: Measure the dimensions of the cut foam block. Make sure they meet the design specifications.
Evaluate surface finish: Look for smooth edges with no wear. Clean cuts indicate correct tool setup and machine operation.
Identify and solve problems: If you find any irregularities, adjust cutting parameters or check tool wear. Regular machine maintenance ensures consistent performance.
Common troubleshooting during cutting:
01. Problem: Jagged edges on cut foam
Possible causes: Blunt blade, incorrect cutting speed or oscillation frequency.
Solution: Replace the blade and adjust the cutting speed and oscillation frequency to better suit the foam density.
02. Problem: Foam deflects during cutting. Possible causes: Improper material fixation, machine vibration.
Solution: Make sure the foam is firmly fixed to the cutting surface, check and adjust machine stability.
03. Problem: Inconsistent cutting depth Possible causes: Incorrect tool setting, uneven foam thickness.
Solution: Verify and adjust cutting depth setting to ensure uniform thickness across the foam sheet.
Combine precision with efficiency when machining custom EVA foam packaging with an oscillating knife cutter. By choosing the right tools, being well prepared, and following best operating practices, you can produce high-quality foam packaging that meets your customers' needs. Regular maintenance and adherence to safety guidelines ensure the longevity of your equipment and the safety of your team.
With the right approach, you can streamline your production process, reduce waste, and deliver quality products. The detailed steps and tips provided here are designed to help you get the most out of your oscillating knife cutter, ensuring every cut is perfect and every product is protected.