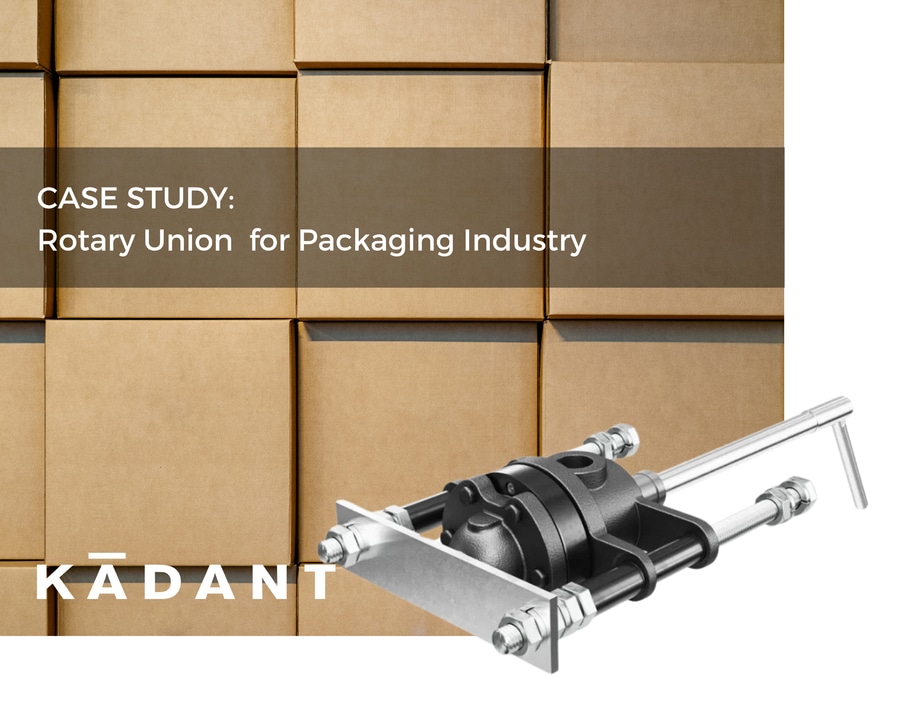
#Industry News
CASE STUDY: Rotary Union for Packaging Industry
Corrugator Increases Runnability To Meet Customer Orders
Challenge:
A major corrugated packaging plant on the East Coast was struggling to meet customer orders on heavyweight board combinations and needed to increase machine runnability quickly. Medium pre-conditioner rolls had uneven and inconsistent heat transfer and the steam shower had inadequate steam flow. To compensate, wrap arms were fully extended and the machine was running at
slower speeds. Additionally, the insufficient steam shower pre-conditioning of the medium before it entered the single facer was causing issues in flute forming and single face web bonding.
---
Solution:
Kadant Johnson experts worked with the customer’s regional manufacturing manager, mill manager, and mill production superintendent to evaluate the runnability challenge. New LJX™ rotary joints with rigid syphons were
installed to ensure continuous condensate evacuation. A ThermoMax® Steam MoisturizerTM system was also installed to increase steam quantity and distribution across the medium. The Kadant Johnson Services team installed the turnkey project over a weekend shut down.
---
Results:
Operational runnability and productivity immediately improved, and speed increased 100 fpm for heavyweight board combinations. The increase in lineal feet per hour recovered the plant investment in less than one month.
Setting and maintaining the proper syphon clearance improved heat transfer across the pre-conditioner roll, resulting in less wrap and increased machine speeds. The moisturizer increased the temperature and moisture content of the medium before it entered the single facer resulting in improved flute formation, bonding, and machine speed.