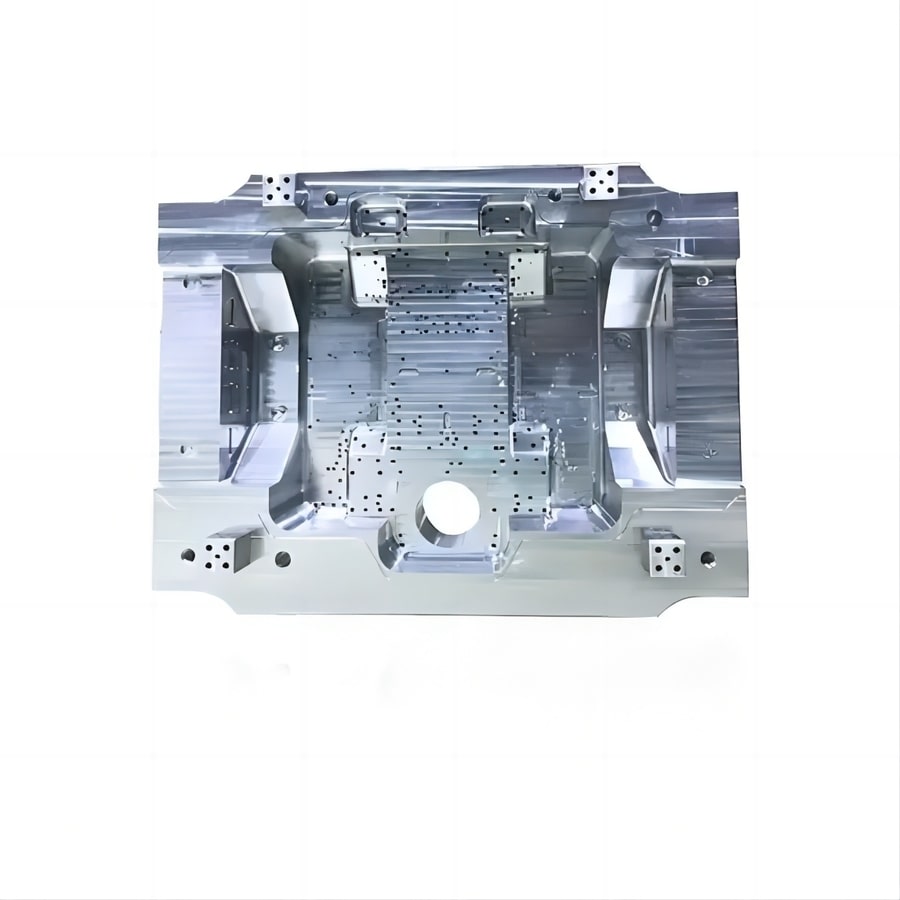
#Industry News
How Does The Implementation Of A One-Piece Die-Forged Body Structure Make Contributions To The Reduced Weight Of The New Strength Vehicle Rear Warehouse Mildew
How Does The Implementation Of A One-Piece Die-Forged Body Structure Make Contributions To The Reduced Weight Of The New Strength Vehicle Rear Warehouse Mildew
How does the implementation of a one-piece die-forged body structure make contributions to the reduced weight of the new strength vehicle rear warehouse mildew, and what implications does this have for the overall performance and performance of electric automobiles?
The integration of a one-piece die-solid frame shape inside the layout of recent strength automobile rear warehouse molds plays a pivotal function in achieving decreased weight, offering numerous blessings that appreciably impact the general performance and performance of electric motors (EVs).
1. Material Selection and Lightweight Alloys:
One of the important thing elements contributing to the decreased weight of one-piece die-solid systems is the cautious choice of substances. Manufacturers frequently choose light-weight alloys consisting of aluminum, magnesium, or zinc. These alloys own an superb electricity-to-weight ratio, permitting engineers to layout sturdy structures even as maintaining the overall weight to a minimum. Aluminum, mainly, is broadly favored for its low density, corrosion resistance, and recyclability.
2. Complex Geometries and Optimization:
The die-casting technique lets in for the introduction of intricate and complicated shapes, optimizing the layout of the rear warehouse mould. This freedom in layout permits engineers to strategically distribute cloth only wherein it is structurally essential, casting off excess weight and reaching a extra efficient use of sources. By minimizing pointless fabric, the overall weight of the element is decreased with out compromising structural integrity.
3. Impact on Electric Vehicle Efficiency:
The decreased weight of the one-piece die-solid rear warehouse mold has direct implications for the efficiency of electrical automobiles. As EVs are particularly sensitive to weight due to their reliance on battery-powered propulsion systems, any reduction in automobile weight translates to progressed electricity performance and expanded driving range. Lighter components make contributions to lower energy consumption throughout acceleration, deceleration, and average car operation, thereby improving the overall performance of the electric drivetrain.
4. Enhanced Range and Battery Performance:
A lighter rear warehouse mold positively affects the electric vehicle's range by means of decreasing the power required to transport the vehicle. This is in particular critical inside the context of new electricity motors, in which improvements in battery era are continuously pursued to increase riding stages. The aggregate of lightweight materials and optimized design enables to maximise the efficiency of the whole vehicle, making an allowance for longer distances on a unmarried rate.
5. Improved Handling and Maneuverability:
Reduced weight no longer most effective enhances power efficiency however also contributes to advanced dealing with and maneuverability of electric cars. The decrease mass reduces the inertia, making the vehicle more conscious of driving force inputs. This is specially crucial for accomplishing a stability between energy performance and a satisfying driving experience in new energy automobiles.
In conclusion, the adoption of a one-piece die-solid body structure for brand spanking new energy automobile rear warehouse molds, with a focal point on decreased weight via material selection and optimized design, is a essential detail in advancing the performance and overall performance of electric motors. As the car industry continues to prioritize sustainability and power efficiency, improvements in lightweight components will play a pivotal position in shaping the future of electrical mobility.