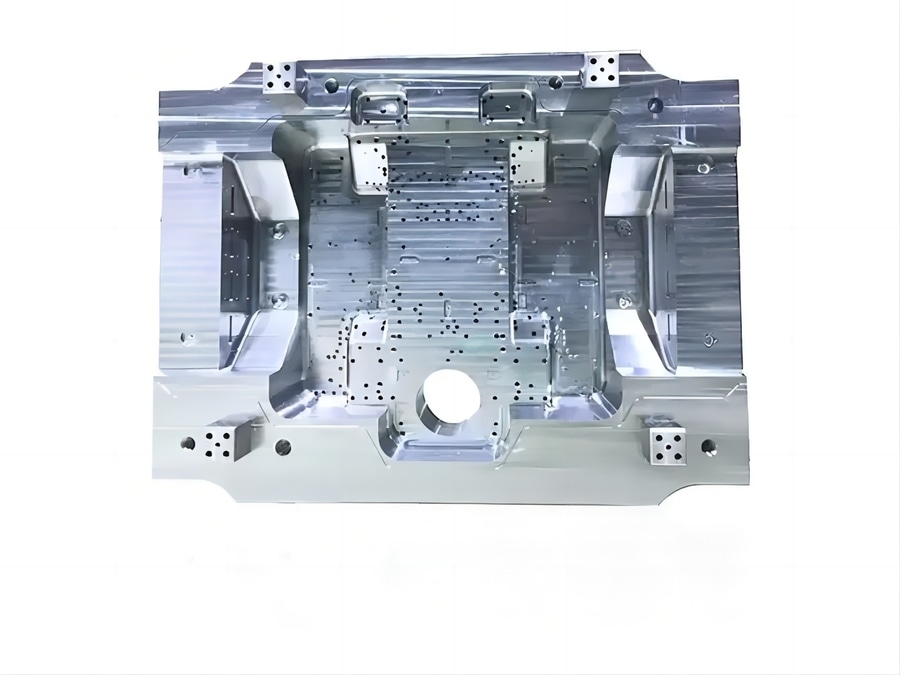
#Industry News
The Automotive Industry Is Constantly Evolving And Evolving The Way It Manufactures Its Products
The Automotive Industry Is Constantly Evolving And Evolving The Way It Manufactures Its Products
Automotive Mould Case
The automotive industry is constantly evolving and evolving the way it manufactures its products. As a result, manufacturers are looking to produce more and more efficient and effective cars and trucks. They are focusing on improving fuel economy by using lightweight materials, reducing overall vehicle weight, and designing components that can withstand the demands of the environment.
As such, many automakers are turning to die casting processes to create components that are lightweight and durable. This process is able to produce custom-made, intricate, and dimensionally stable metal parts.
Choosing the right mold design for your die-cast product is important to ensuring high quality and optimum productivity. The design should allow for a good surface finish and dimensional stability without creating excess stress or heat that could damage the mold. It should also allow for adequate clearance around symbols, logos, and other features that can be difficult to machine or assemble correctly in the final part.
For example, a raised logo or symbol may require extra molten metal volume to cast, whereas a recessed logo or symbol requires less raw material and will typically save money on production. Additionally, a logo or symbol that is recessed into the part can be easier to remove from the mold than a raised logo.
Aluminum Die Casting
The aluminum die casting process is a great choice for making engine parts and wheels. It has a high strength-to-weight ratio, and can help manufacturers build strong, efficient vehicles.
It is a cost-effective way to manufacture complex and specialized components that cannot be produced using other forms of manufacturing, such as injection molding. The aluminum die casting process can also be used to make very large, heavy components such as gear boxes and valve bodies.
Moreover, it is a reliable and high-volume casting method that can be used to manufacture products with challenging shapes and sizes. This type of casting has a wide variety of applications and can be used for consumer and industrial products, aerospace components, automotive components, and medical devices.
The benefits of aluminum casting include improved corrosion resistance, flexibility, and a higher strength-to-weight ratio. This makes it a great option for engineers who are designing advanced and smarter automobiles.
For instance, Tesla is using a massive IDRA Giga Press to die cast the front and rear chassis frames of its Model Y. The Giga Press is a large, high-pressure aluminum die casting machine that uses a cold-chamber casting mold to inject molten aluminum weighing more than 100 kg into the mold.
This press can be installed at a car plant or other manufacturing facility to make complete, one-piece, molded parts. This means that automotive OEMs can create an entire body-in-white as a single piece, eliminating the need for separate pieces to be assembled into a finished vehicle.
A major challenge with this technology is that it must be capable of producing large, complex castings while keeping pressure and cycle times low. The Giga Press has been built with a number of innovative engineering solutions to address these challenges and achieve high production rates, low costs, and superior part integrity.