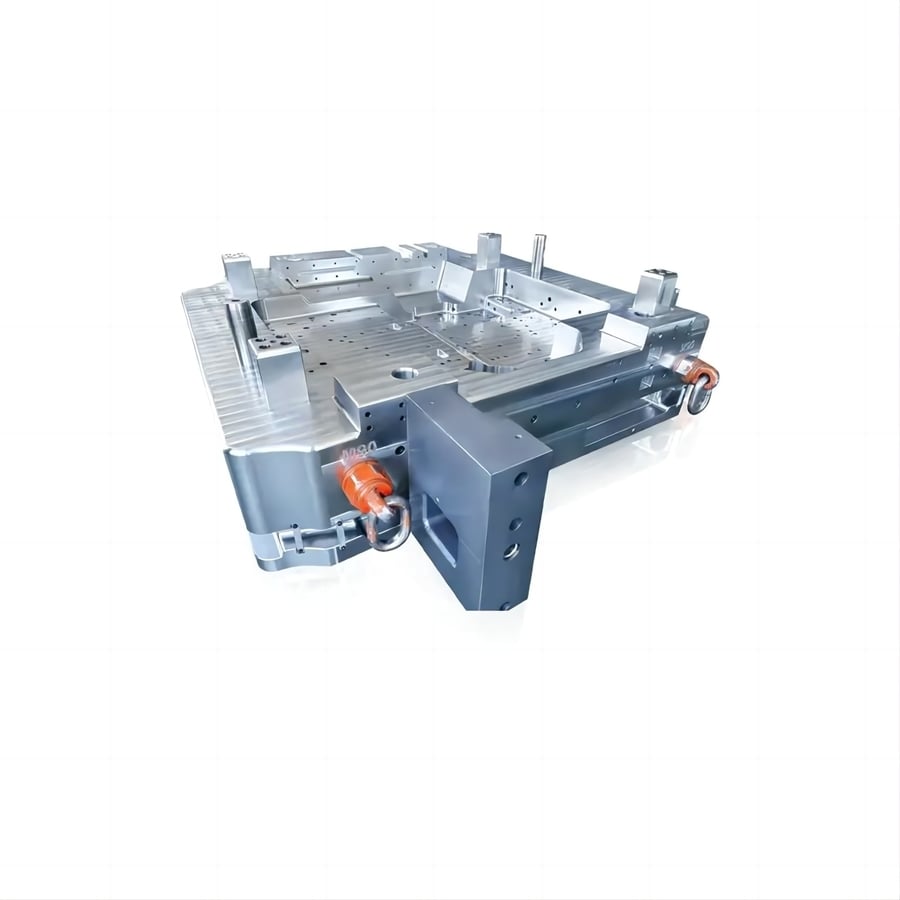
#Industry News
How Does The Design And Material Choice Of The Mold Frame For The Rear Warehouse Left-Right Structure Of New Energy Vehicles Impact Structural Integrity, Weight Distribution, And Overall Vehicle Performance And Safety?
How Does The Design And Material Choice Of The Mold Frame For The Rear Warehouse Left-Right Structure Of New Energy Vehicles Impact Structural Integrity, Weight Distribution, And Overall Vehicle Performance And Safety?
The mold frame for the rear warehouse left-right structure of new energy vehicles play a critical role in ensuring the overall performance, safety, and structural integrity of these vehicles. This frame serves as the foundation for the rear warehouse, accommodating battery packs, electric drivetrains, and other components. The design and material choices for the mold frame can significantly influence various aspects of the vehicle's performance and safety. Let's delve into these factors in detail:
Structural Integrity:
The structural integrity of the mold frame directly affects the vehicle's overall stability and safety. The frame must be designed to withstand various loads and forces encountered during vehicle operation, including acceleration, braking, and cornering. Additionally, it should be capable of supporting the weight of the rear warehouse components without deformation or failure.
To ensure optimal structural integrity, manufacturers need to perform rigorous engineering analyses, such as finite element analysis (FEA), to simulate and assess the frame's behavior under different load conditions. This analysis aids in identifying potential weak points or stress concentrations and allows for design improvements to enhance the frame's strength and durability.
Weight Distribution and Balance:
The mold frame's design significantly impacts the weight distribution and balance of the new energy vehicle. Proper weight distribution is essential for achieving stable handling and predictable dynamics during driving. Uneven weight distribution can lead to issues like understeer or oversteer, negatively affecting the vehicle's cornering performance and overall handling characteristics.
By optimizing the mold frame's design, manufacturers can achieve a well-balanced weight distribution between the front and rear of the vehicle. This can contribute to improved traction, better road grip, and enhanced overall driving dynamics, promoting a safer and more enjoyable driving experience for the vehicle occupants.
Material Choice and Weight Reduction:
The material choice for the mold frame has a direct impact on the weight of the vehicle. New energy vehicles, such as electric cars or hybrids, benefit from reduced weight to maximize their driving range and overall energy efficiency. Therefore, selecting lightweight yet strong materials is crucial to achieving weight reduction without compromising structural integrity.
Aluminum alloys and high-strength steel are common materials used for mold frames in new energy vehicles due to their favorable strength-to-weight ratios. These materials not only contribute to weight reduction but also offer good corrosion resistance, making them suitable for diverse environmental conditions.
Safety and Crashworthiness:
Safety is paramount in the automotive industry, and the mold frame's design must consider crashworthiness to protect occupants in the event of a collision. The frame should be engineered to absorb and dissipate crash energy, reducing the impact forces transferred to the vehicle's cabin.
Integrating crash safety features like energy-absorbing structures, deformation zones, and reinforcement elements into the mold frame's design enhances the vehicle's overall crashworthiness. This attention to safety measures ensures compliance with regulatory standards and improves the vehicle's safety rating, instilling confidence in consumers regarding the new energy vehicle's safety performance.
Manufacturing Efficiency and Cost:
Efficient manufacturing processes and cost considerations are crucial for mass-producing new energy vehicles. The design of the mold frame should be optimized for ease of manufacturing, ensuring cost-effectiveness without compromising quality.
Manufacturers can utilize advanced manufacturing techniques such as computer numerical control (CNC) machining, die-casting, or extrusion processes to efficiently produce the mold frame components. Moreover, design optimization and material selection can help strike a balance between manufacturing costs and overall performance.
In conclusion, the design and material choice of the mold frame for the rear warehouse left-right structure of new energy vehicles play a pivotal role in determining their structural integrity, weight distribution, and overall performance and safety. By focusing on factors such as structural analysis, weight reduction, material selection, crashworthiness, and manufacturing efficiency, automotive manufacturers can deliver safe, efficient, and high-performing new energy vehicles that meet the demands of environmentally conscious consumers.