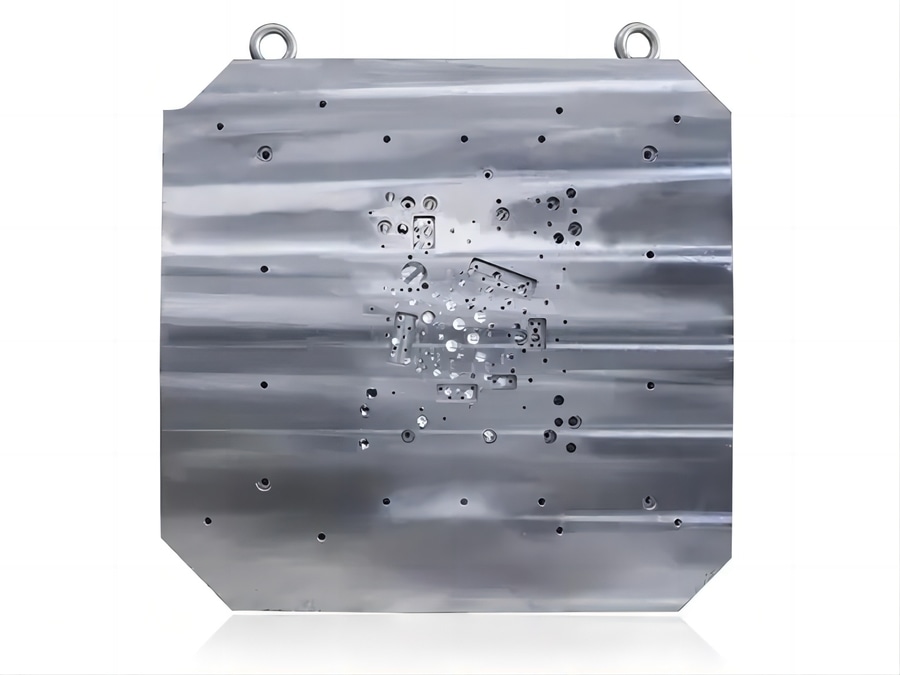
#Industry News
What Are The Challenges And Potential Drawbacks Associated With Using Alloy Molding Frames In The Three-Cylinder Engines Of Fuel Cars, And How Can Manufacturers Address These Issues To Fully Leverage The Benefits Of This Technology?
What Are The Challenges And Potential Drawbacks Associated With Using Alloy Molding Frames In The Three-Cylinder Engines Of Fuel Cars, And How Can Manufacturers Address These Issues To Fully Leverage The Benefits Of This Technology?
The adoption of alloy molding frames in the construction of three-cylinder engines for fuel cars offers numerous advantages, as discussed previously. However, this innovative technology also comes with its share of challenges and potential drawbacks that need to be addressed to fully leverage its benefits. Let's explore these issues in detail:
Thermal Expansion and Contracting:
Aluminum alloys have a higher coefficient of thermal expansion compared to traditional cast iron or steel frames. As the engine heats up during operation, the alloy molding frames may expand, leading to potential issues like increased clearances between mating engine components and possible leakage points. Similarly, during cool-down periods, the frames may contract, which can introduce stresses on the engine structure.
To mitigate these challenges, manufacturers need to carefully consider the design and material selection of the alloy molding frames. Engineering solutions such as thermal barriers, proper gasket materials, and precise machining tolerances can help address thermal expansion concerns and ensure the long-term reliability of the engine.
Material Compatibility and Wear:
When alloy molding frames are used alongside other engine components made from different materials, there is a possibility of galvanic corrosion, also known as dissimilar metal corrosion. Galvanic corrosion occurs when two dissimilar metals are in contact with each other and an electrolyte (e.g., engine oil) is present, leading to accelerated material degradation.
To combat galvanic corrosion, manufacturers can use coatings or sacrificial anodes to protect the alloy molding frames. Additionally, careful material selection for other engine components and the implementation of appropriate isolation measures can minimize the likelihood of galvanic corrosion and ensure the longevity of the engine.
Structural Integrity and Fatigue:
Aluminum alloys have different material properties compared to cast iron or steel, which can impact the structural integrity and fatigue resistance of the alloy molding frames. Engine components, especially those subjected to high-stress conditions, must withstand repetitive loading cycles without failure.
To enhance structural integrity and fatigue resistance, manufacturers can perform detailed finite element analysis (FEA) and use advanced simulation tools during the design phase. This approach enables them to optimize the frame's geometry and thickness distribution, ensuring it meets the required mechanical properties and remains durable throughout its operational life.
Cost Considerations:
The manufacturing cost of alloy molding frames can be higher than traditional materials, such as cast iron. The increased cost can directly impact the overall production cost of the vehicle, potentially affecting its market competitiveness.
Manufacturers can explore opportunities to optimize the alloy molding process and increase production efficiency to bring down the cost. Additionally, advancements in material technology may lead to the development of more cost-effective aluminum alloys without compromising performance, making them more viable for mass production.
Recycling and Environmental Impact:
While aluminum alloys are recyclable, the recycling process requires significant energy inputs. As the automotive industry continues its pursuit of sustainability and reduced environmental impact, addressing the energy-intensive recycling process becomes crucial.
To tackle this challenge, manufacturers can invest in sustainable manufacturing practices and explore closed-loop recycling systems. These systems would promote the collection and reuse of scrap aluminum generated during the manufacturing process, thereby reducing the reliance on primary raw materials and lowering the overall environmental footprint.
In conclusion, the adoption of alloy molding frames in three-cylinder engines of fuel cars presents a promising avenue for enhancing performance, fuel efficiency, and overall vehicle dynamics. However, manufacturers must carefully address the challenges associated with thermal expansion, material compatibility, structural integrity, cost considerations, and recycling to maximize the benefits of this technology while ensuring long-term reliability and sustainability. By doing so, the automotive industry can continue its pursuit of innovation and efficiency in the era of fuel-efficient and environmentally conscious vehicles.