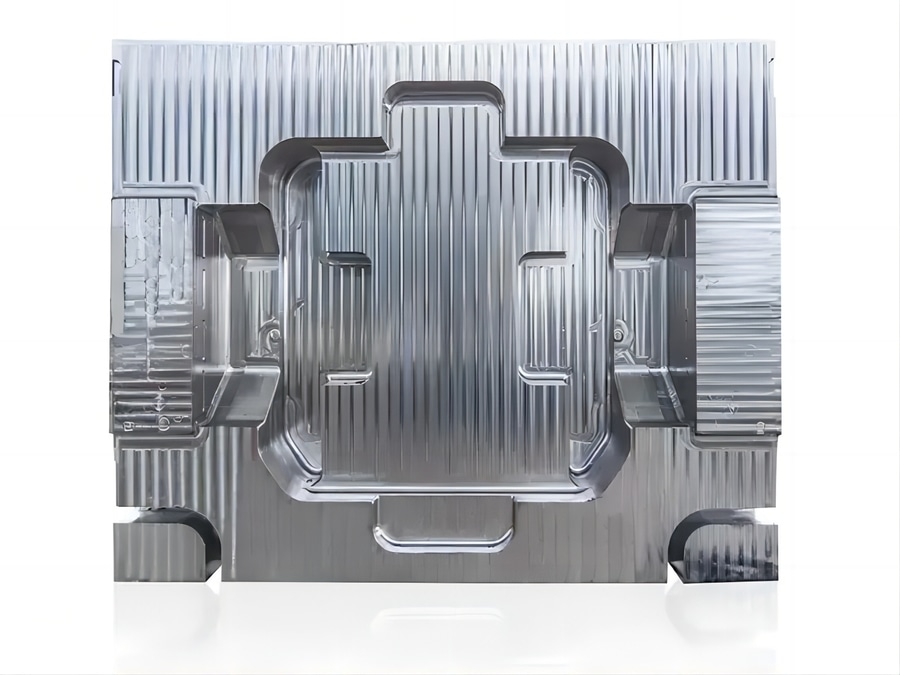
#Industry News
How Does The Adoption Of A One-Piece Die-Cast Body Structure In The Rear Warehouse Of New Energy Vehicles Impact Vehicle Performance, Safety, And Sustainability?
How Does The Adoption Of A One-Piece Die-Cast Body Structure In The Rear Warehouse Of New Energy Vehicles Impact Vehicle Performance, Safety, And Sustainability?
The adoption of a One-piece die-cast body structure in the rear warehouse of new energy vehicles (NEVs) brings forth a range of significant implications for vehicle performance, safety, and sustainability. Let's explore these aspects in detail:
Performance:
The One-piece die-cast body structure offers several advantages that can enhance the overall performance of new energy vehicles. By integrating multiple components into a single unit, it reduces the weight of the vehicle, leading to improved energy efficiency and range. The streamlined design also reduces air resistance, contributing to better aerodynamics and, consequently, higher speeds and smoother handling.
Moreover, the structural rigidity provided by the One-piece design enhances the overall vehicle stability, reducing chassis flex during acceleration, cornering, and braking. This stiffness can positively impact the vehicle's dynamic performance and contribute to a more enjoyable driving experience.
Safety:
Safety is a paramount concern for all automotive manufacturers and consumers alike. The One-piece die-cast body structure brings inherent safety benefits due to its monolithic construction. The elimination of weld points and joints minimizes the risk of structural weaknesses, which could compromise the vehicle's crashworthiness.
Additionally, the One-piece design allows for better distribution of impact forces in the event of a collision, improving the vehicle's ability to absorb and dissipate crash energy. This enhanced crash resistance can protect occupants and reduce the severity of injuries, making NEVs with One-piece die-cast bodies safer on the road.
Sustainability:
The automotive industry is striving to reduce its environmental impact, and adopting a One-piece die-cast body structure in NEVs aligns with this goal. The manufacturing process of One-piece castings typically involves less energy consumption compared to traditional assembly methods with multiple components. As a result, there is a potential reduction in greenhouse gas emissions during the production phase.
Moreover, the lighter weight of the One-piece design improves the vehicle's energy efficiency, leading to reduced carbon emissions during the usage phase. In the context of new energy vehicles, this plays a crucial role in maximizing the benefits of electric or hybrid powertrains, extending driving range, and minimizing the carbon footprint associated with vehicle operations.
Manufacturing Complexity and Cost:
While the One-piece die-cast body structure offers numerous benefits, it also presents challenges related to manufacturing complexity and cost. The production of large, intricate castings requires specialized equipment and precise casting techniques. This could increase initial investment costs for automakers, potentially impacting the final price of NEVs equipped with One-piece castings.
Furthermore, any design changes or modifications may require the development of entirely new casting molds, which could add to the development time and cost. However, advancements in casting technology and material sciences are continually evolving, and with increased adoption, economies of scale may drive down production costs over time.
In conclusion, the One-piece die-cast body structure holds significant promise for new energy vehicles, with benefits spanning performance, safety, and sustainability. However, careful consideration of manufacturing challenges and cost implications is essential for the widespread implementation of this advanced technology in the automotive industry.