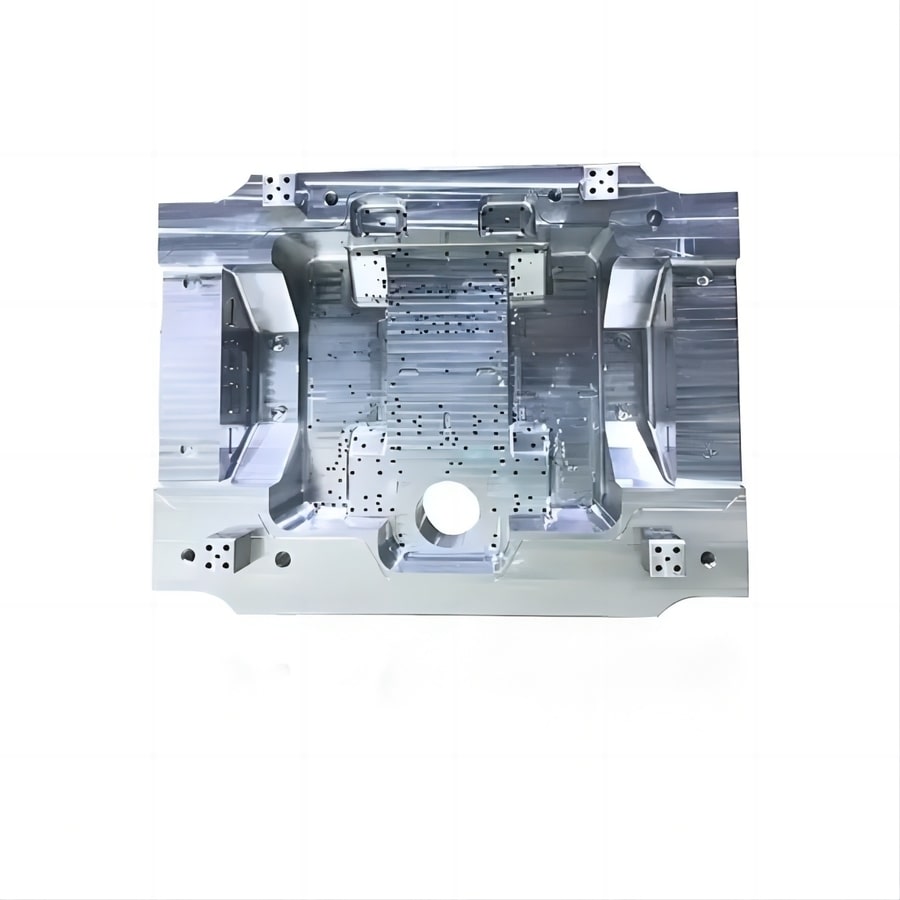
#Industry News
The Automotive Mold Base Is The Underlying Metal Structure Of The Injection Mold
The Automotive Mold Base Is The Underlying Metal Structure Of The Injection Mold
The automotive mold base is the underlying metal structure of the injection mold. The base is a solid piece of steel that supports the two halves that make up the mold. The mold base is designed for a specific product, and it can be made from carbon steel or stainless steel, depending on the application.
The base can be made to hold a variety of different inserts and cavities, which allows a single base to produce multiple variations of the same part. This type of interchangeable sort can help reduce the number of tooling changes and production costs, and it is a great option for smaller parts that require frequent changeovers.
In a standard production program, Kejia (Changxing) Mould Base Manufacturing Co., Ltd will typically design the base with anywhere from four to 32 cavities. This depends on the part geometry and production capacity requirements.
When the injection molded component needs to be produced on multiple machines, Kejia (Changxing) Mould Base Manufacturing Co., Ltd will typically design the base with two or more nozzles so that they can fill different cavities at the same time. This allows for heightened productivity and reduced costs when producing larger, more complex parts with multiple features.
A mold base can also be designed with an integrated flange seal that is molded to the surface of the part to provide additional sealing capabilities. This can be particularly beneficial for applications involving high-temperature environments, and it can save time and material as it eliminates the need to assemble the flanged seal separately from the molded component.
Often, the flanged seal is produced with a direct gate sprue, which removes the need for elevated marks or flash on the surface of the molded product and decreases the cost of materials. It also allows for better material flow to eliminate sprue accumulation, and it is more effective when the parts have complex features that aren't easily accessed with traditional tools.
The use of a direct gate can save up to 30% on material costs. In addition, it can reduce the need for de-burring after the molding process and minimize part weight as the sprue doesn't add any material to the part.
Injection molded components are used in a wide range of car parts, from dashboards and seats to hoods and fenders. The plastics used in these products vary, but they are most commonly PP (seats, body, under the hood), PU (seats, upholstery), and PVC (body, upholstery).
When designing the part, it's important to keep in mind that there are many factors that can affect mold life. Some of these include:
Using the correct material for the part's purpose and functionality
When creating the mold, it's important to choose a material that will perform well in the machining process. For example, aluminum is a good choice for a part with rounded surfaces because it's more resistant to bending than steel or iron, while copper is excellent for a smooth, polished finish.
It's also essential to pick a material that will stand up to the demands of a hot-running process. This is because heat can cause the part to lose its structural integrity, making it susceptible to breakage and damage during production.