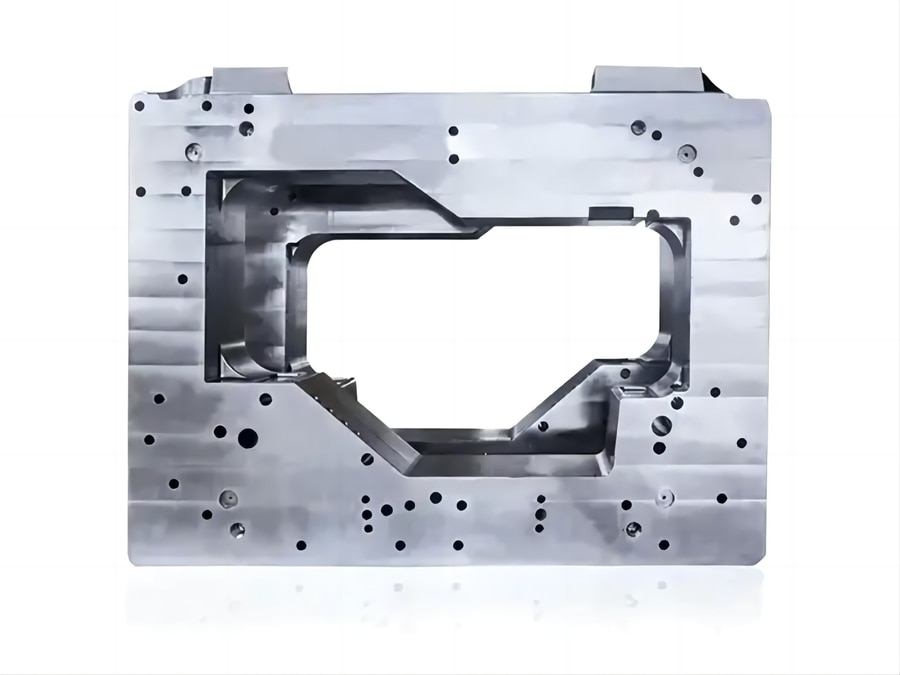
#Industry News
The Automotive Mould Base Consists Of Two Primary Components
The Automotive Mould Base Consists Of Two Primary Components
Automotive Mould Base
The Automotive Mould Base consists of two primary components: the injection mold (A plate) and the ejector mold (B plate). Molding machine operators inject molten plastic resin into the cavity images in the A plate; the resulting plastic part then cools and hardens before being removed from the B plate.
The runner system in the injection mould directs molten plastic resin from the barrel of the injection molding machine into the cavity images. This is achieved through a sprue bushing, which seals tightly against the nozzle of the injection barrel and directs the molten plastic to these cavities. In addition to a sprue, the runner system may also include an opening (tunnel gate) in the mould surface on the parting line that allows molten plastic resin to run freely through the runner.
These sprues are a vital part of the injection molding process; they enable molten plastic resin to flow into the cavity image through channels that are machined into the faces of the A and B plates. Unlike the injection barrel and sprue, these runner systems are cold; they are not designed to be heated.
Injection moulds are the most common method of manufacturing plastic parts for the automotive industry. They are scalable and can produce many parts in a single moulding cycle, which makes them an ideal choice for mass production applications.
They can be used to manufacture both exterior and interior car parts, which help manufacturers reduce the weight of their vehicles. They can also be used to create decorative elements, such as grilles, door handles, and air vents.
Using plastics for these car parts is an effective strategy to help lower the overall weight of a vehicle and improve fuel efficiency. In addition, many plastics are able to resist extreme weather conditions and harsh terrains, which can be challenging for metals.
Another significant advantage of plastics for car parts is their low cost. Injection molded plastics are usually much cheaper than their metal counterparts, which helps manufacturers save on production costs. Additionally, they can be customized to meet a specific aesthetic requirement, which is helpful for enhancing the look of a vehicle.
When designing and producing a plastic component for an automotive application, it is essential to partner with an experienced injection molder who understands the unique requirements of the application. They can leverage their material expertise to help ensure that the component meets regulatory specifications and performs as expected, as well as offer valuable insights into the automotive industry.
The right material is the key to the success of any automotive plastic part design. Injection molders can advise on the best polymer type to use based on their material strength, dimensional stability, and heat-resistance properties.
They can also provide recommendations on how to optimize the design to achieve the desired functionalities and performance goals for each application. This is especially important for complex and high-volume components, such as those found in the engine bay of a vehicle.