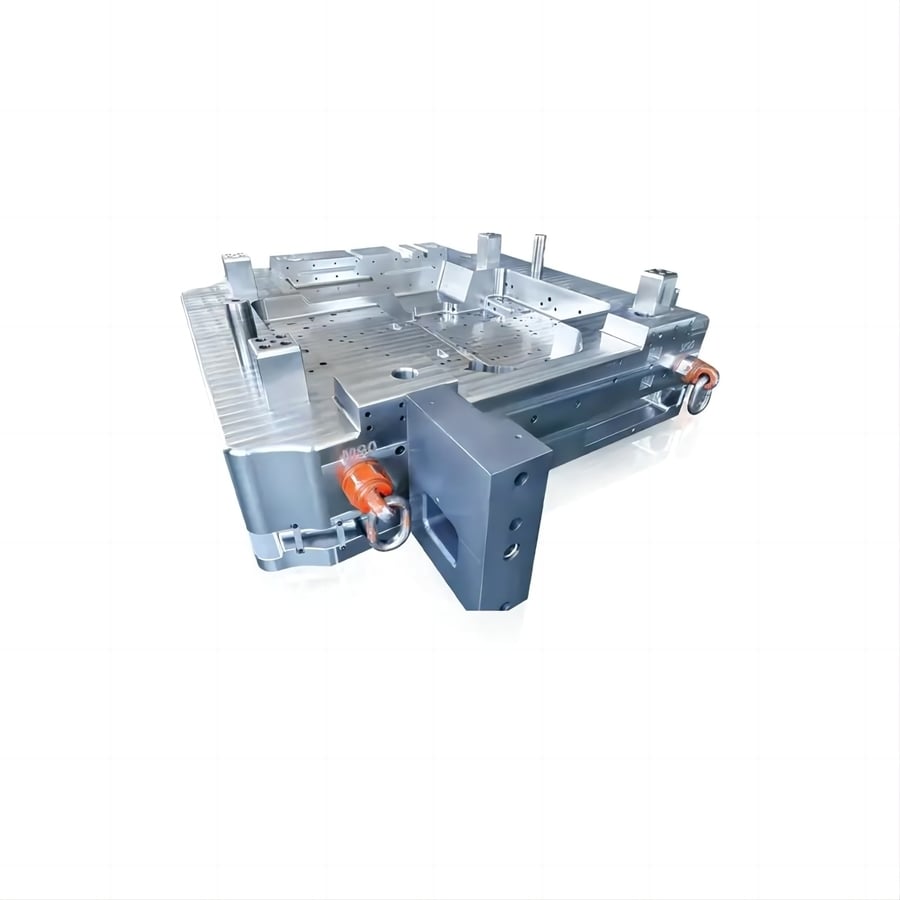
#Industry News
There Are Several Key Aspects To Consider When Designing And Making A Die Casting Mold
There Are Several Key Aspects To Consider When Designing And Making A Die Casting Mold
Die Casting Automotive Mould Base
The automotive industry is very competitive, and with the increasing demand for fuel economy and emission control, manufacturers are turning to die casting for many of their parts. This method of metal casting is able to reduce weight and save on manufacturing costs while also producing parts that meet the exact requirements of the customer.
There are several key aspects to consider when designing and making a die casting mold. These include the materials used in the part, the type of metal being molded and the shape and accuracy required for the final product.
Draft Angle
The draft angle of a die casting mold is an important factor in the ejection of the molten metal and the quality of the end result. It varies depending on the shape of the wall and the type of molten alloy being poured, as well as on the depth of the mold core.
Holes and Windows
The holes in a die casting mold are essential for allowing the molten metal to flow through and eject smoothly from the mold. In addition, they allow for the creation of sizeable drafts that can be used to increase casting density and thereby improve the quality of the product.
Ribs
The design of ribs is an important consideration when creating a die casting mold. Ideally, ribs should be thin and deep to ensure the stiffness of the mold and minimize stress cracking in the molded part.
Pockets or Metal Saver
The pockets in a die casting mold are placed strategically to aid the flow of the molten metal and decrease the thickness of the finished product. This allows the part to be lighter without compromising its structural integrity.
Sprue Bushing
The sprue bushing is a vertical connector that connects the face of the mold to the machine’s nozzle. The sprue bushing is usually made from hardened steel or copper base alloy and helps to prevent the molten metal from dripping on the surface of the die.
Sprues are also a critical part of the die casting process because they control the molten metal flow and help to prevent solidification shrinkage cavities in the resulting mold. The sprue bushing is typically made from hardened steel and often has a ceramic coating for protection against the molten metal.
Ejector Die
The ejector die is located in the front part of the mold and acts as a guide for the molten metal to be sucked into the cavity. It is commonly made from hardened steel and can be lubricated to improve the ejection of the molten material and to make the process easier.
Cover Die
The cover die is the part of the die that covers the ejector die and is usually made from copper base alloy or hardened steel. It is usually designed to be as narrow as possible and to help with ejection of the molten metal.
Bosses
The bosses in a die casting mold serve as mounting points and standoffs for the various die cast parts. The bosses should be sufficiently thick to support the weight of each part, and they should be added with a hole in their interior structure to facilitate uniform wall thickness.