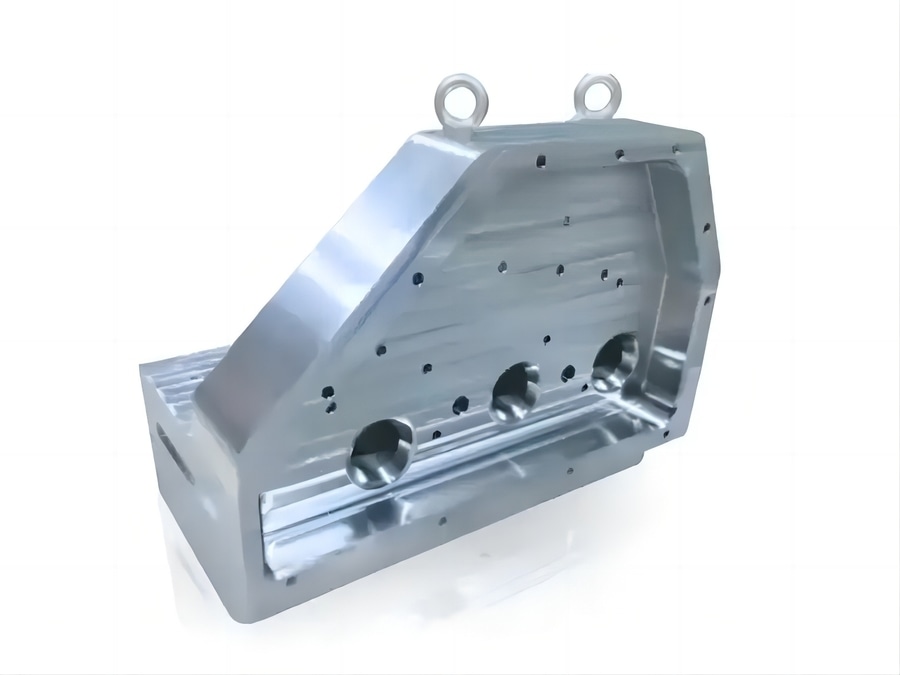
#Industry News
Injection Molded Automotive Parts Are Used In A Wide Range Of Applications
Injection Molded Automotive Parts Are Used In A Wide Range Of Applications
Automotive Injection Mold Base
Injection molded automotive parts are used in a wide range of applications. They are commonly used for exterior components such as fenders, bumpers, grilles, and door panels, as well as for under-the-hood items like cylinder head covers and oil pans. In addition, they can help to reduce the weight and cost of a car by replacing metal parts.
Typical Automotive Injection Mold Base
In most cases, the injection mold is made from aluminum, which is relatively inexpensive and can withstand a large number of injection cycles without breaking down or becoming damaged. However, for higher volumes, steel or titanium tooling is more common.
The Automotive Injection Mold Base consists of two halves: the core half and the cavity half. During each cycle, these two halves are aligned using guide pillars and guide bushings to ensure quality.
This alignment is based on the "POKE YOKE" concept and is achieved through interference fit between the top plate and the machine pattern and transmission fit between the top plate and the register ring. This alignment is critical to the injection molding process and helps to keep a part within tolerance while it's being injected.
Runners, Gates, and Injection
The molten plastic enters the injection mold through the sprue and then runs through several channels called runners. Each runner contains a gate that directs the flow of molten plastic. The runner system also allows the part to be separated from the mold after it's ejected.
There are different types of gates that can be used in the runner system. These include edge gates, tunnel gates, and post gates.
During the ejection process, plastic entrained in the runner system is pushed out of the molded part by the ejector bar, which is attached to the ejector plate inside the ejector box. The ejector bar then pushes the ejector plate forward inside the ejector box, which in turn forces the ejector pins to push the molded part out of the open mold cavity.
The ejection system is also designed to be flexible, so it can handle varying incoming pressures. This flexibility allows a wide variety of plastics to be molded in the same mold.
Molding is a complex process that requires precise engineering. This means that the Automotive Injection Mold Base has to be designed with precision and a high level of accuracy.
To make sure the mold base is strong and durable, it's important to design it with a minimum thickness that will be able to handle the injection molding cycle. Thinner designs reduce the amount of plastic used in the injection molding cycle, which can significantly cut costs.
It's also important to design the mold base so that it can withstand the high temperature and pressure of the injection molding process. A strong, properly-designed mold base will last longer and allow for greater production volumes.
Creating a CAD model of your automotive part is the first step in designing the Automotive Injection Mold Base. Typically, this takes one to two days depending on the size of the part. Once the CAD model is completed and DFM approved, the 3D modeling can begin. It's usually best to work on the CAD model in parallel with other aspects of the mold design so that the whole process is more efficient.