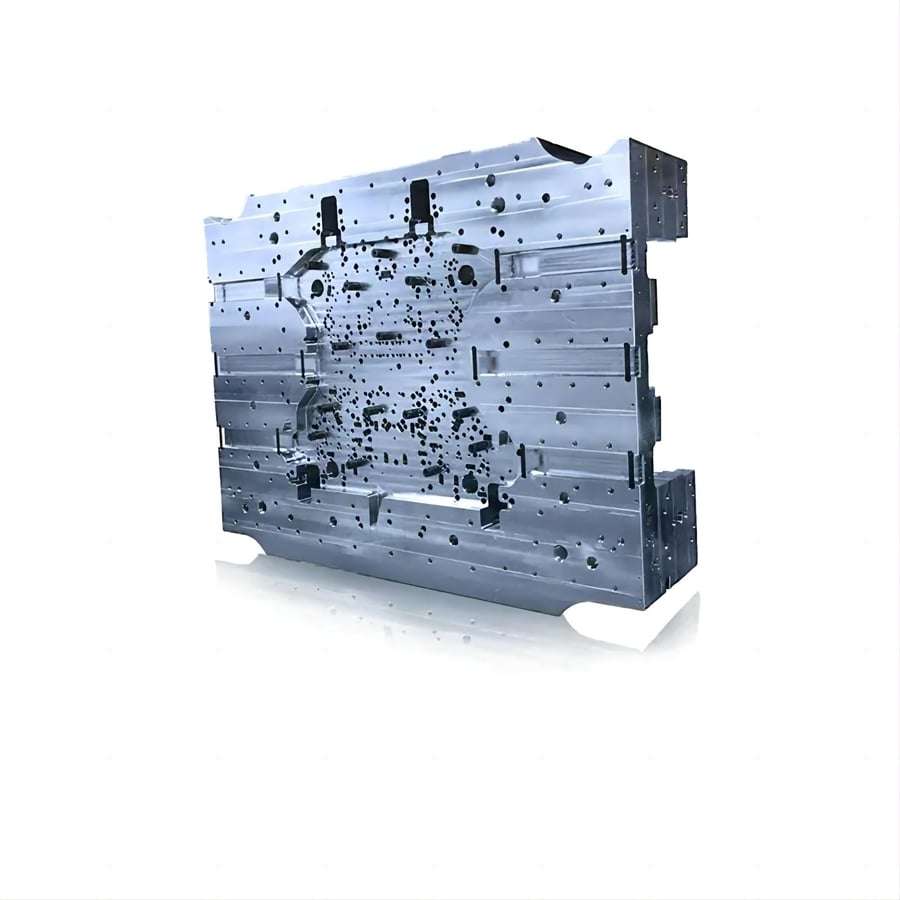
#Industry News
Metal Casting Is A Manufacturing Process That Involves Pouring Molten Metal
Metal Casting Is A Manufacturing Process That Involves Pouring Molten Metal
Metal Casting Mould Base
Metal casting is a manufacturing process that involves pouring molten metal into a mould cavity of a desired geometrical shape and then cooling it to solidify a metal part. Casting is one of the oldest manufacturing techniques in history, and it can be used to produce a variety of parts from automobile engine blocks, crankshafts, and power tool housings such as pillar drills, plumbing parts, turbine blades, and metal statues.
The first step in the metal casting process is to create a mould base. These are metal blocks that can be machined to form the mold, and they also contain a gating system to allow the molten metal to flow into the mold cavities.
This process can be done by hand, or it can be automated using a die-casting machine. In either case, the mould base should be manufactured from a durable material that can withstand the heat and pressure of the poured metal.
There are a number of different types of mould bases. Some of them are made from natural sand that has been moistened, while others are manufactured from special materials.
Typically, the sand used is made of a combination of about 15 to 30 percent clay and 8 percent water with silica added for strength. Other metals can also be inserted into the sand.
Most sands have a low melting point, and they can be manipulated into various shapes by heating them in an oven or other controlled setting. They are also very malleable, which can be important for making complex shapes and shapes that require precise machining.
Another type of sand is made from an aluminum-based alloy, which can be shaped into various shapes by welding it with the use of a high-powered laser. This sand is also very tough and has high mechanical properties, making it ideal for complex shapes that can't be produced using other methods.
It is important to design a die cast mold with a pattern that includes a shrinkage allowance. This is necessary to account for the shrinking of the metal during the solidification process.
The pattern should also have a projection area that will help you understand the force that the molten metal can exert on the die walls during the filling of the mold. This can help you reduce the chance of burrs or other aesthetic flaws, and it will also make it easier to determine the final size of the molded part.
Finally, it's important to design the mold cavity and core to fit the melted metal in the mold. This requires careful analysis of the molten metal's movement and orientation, as well as the shape dimension direction.
Generally, the top half of the mold, known as the cope side, is machined first. Then the bottom half, known as the drag side, is machined.
The pattern is then placed over the sandbox. The sand and resin are mixed to create a partially cured shell that adheres to the metal pattern. Then the two halves are assembled, supported by sand or metal shot in a box, and the pouring begins. This process produces a metal casting that is similar to sandcasting but in a more uniform and finished manner.