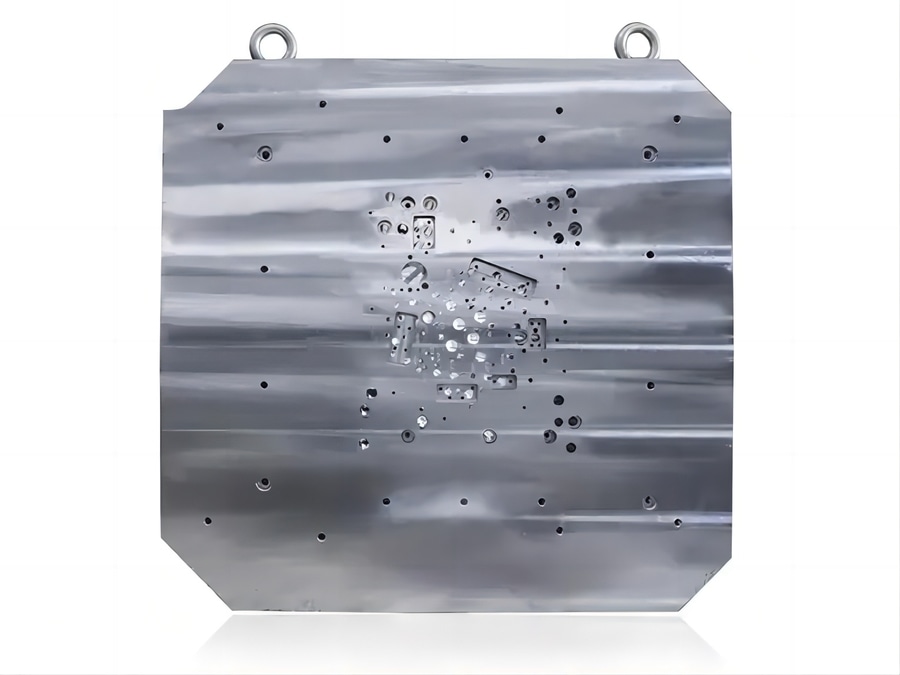
#Industry News
A Die Casting Mold Is A Steel Structure That Is Designed To Produce Thousands Of Metal Parts In One Process
A Die Casting Mold Is A Steel Structure That Is Designed To Produce Thousands Of Metal Parts In One Process
Die Casting Automotive Mould Base
A die casting mold is a steel structure that is designed to produce thousands of metal parts in one process. Typically, these are used to manufacture engine brackets, gearbox cases, valve bodies, hydraulic cylinders and more.
The primary components of this type of mold are the frame and steel plates that make up the base system. They are the foundation for all other mold components, such as cores, insert pins, sliders, cavities and inserts.
In addition to the base system, a die casting mold also requires different specialized parts. These include a shot sleeve, injection cylinder and hydraulic plunger for the aluminum casting process.
Shot sleeve is the piece of metal that is used to pour molten metal into the mold cavity during an injection process. It is an essential part of the die casting process and it enables manufacturers to achieve high-quality castings.
Another important component of a die casting mold is the ejector pin that carries the melted metal. This is a crucial piece of the mold that carries the molten metal to the surface of the mold for a smoother finish.
Moreover, the ejector pin is also responsible for the removal of the casting from the sleeve. The ejector pin is calibrated and uniformly operates to push the casting out of the mold.
The ejector pin is usually placed on a portion of the mold that has an open surface, which allows it to be pushed out of the sleeve. This is a critical step in the manufacturing of die cast products since it ensures that all parts will be filled properly and that no voids are created.
Bosses are molded mounting points that are often used to support the weight of die-cast components. These are sometimes made with a hole in the center to ensure that the wall thickness of a molded product is uniform.
These are generally sized according to the dimensions of a die-cast component. Manufacturers can place them in different locations to optimize their function.
It is important to consider the size and shape of the molded part when designing a mold. This will determine the volume and shape of the cavities. It will also affect the filling method.
This will allow the mold to achieve the desired results and the optimum amount of material can be inserted into each cavity. It is a vital aspect of the design that will have a significant impact on the quality of the final product.
For this purpose, a simulation of the filling process is conducted. This will help in calculating the modality of the mold-filling process and it will also help to predict any possible defects that may arise from this process.
Besides, the mold design will be affected by the type of material that is to be used for the die-casting. This can affect the strength and durability of the final product.
Some of the most commonly used metals for auto parts are aluminum and zinc. These metals are extremely lightweight, durable, and provide excellent dimensional stability. They are also very eco-friendly and they can be recycled to create new products. They are also incredibly strong and can withstand high temperatures. They are an ideal choice for automotive products that need to be robust and efficient.