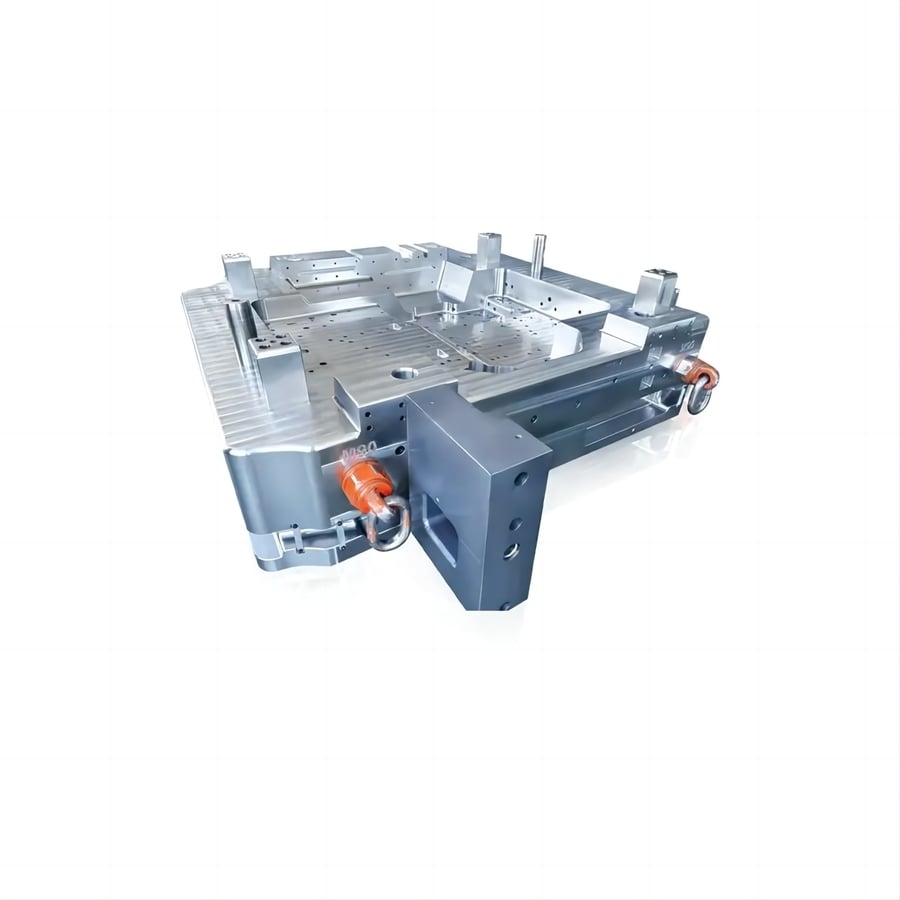
#Industry News
The Main Function Of The Die Casting Automotive Mould Base Is To Produce The Metal Parts Through A Process Known As Die Casting
The Main Function Of The Die Casting Automotive Mould Base Is To Produce The Metal Parts Through A Process Known As Die Casting
Die Casting Automotive Mould Base
The Die Casting of Automotive Mould Base plays an essential role in the production of different types of products used in the automotive industry. It helps to create parts like engine blocks, wheel spacers, alternator housings, and command cable terminals.
The main function of the Die Casting Automotive Mould Base is to produce the metal parts through a process known as die casting. It is an inexpensive and reliable way of producing large numbers of parts for many industrial applications.
This method produces a product by injecting heated molten metal into a mold. It is an excellent choice for small or large quantities of parts and can deliver a high degree of accuracy and finish.
It is also very suitable for the production of parts that require low weight and high strength. The most popular materials for die casting include aluminum, zinc, and magnesium.
One of the biggest advantages of this process is that it can be used for producing a wide variety of shapes and sizes. It is also capable of delivering parts within closer tolerances than other mass production processes.
However, there are several drawbacks to die casting. These include the initial expense of the dies and the need to create a mold for each casting project.
The Mold Design
The mold design of the die-cast mold is an important factor in the overall quality and performance of the part. The design should be simple, accurate, and repeatable.
A well-designed mold will reduce the cost of the parts produced. It will also increase the efficiency of the process.
It should be easy to operate and maintain, as well as have high dimensional accuracy and surface finish. It should also be designed with the right materials, such as steel so that it can withstand long-term wear.
The mold should be designed to be able to withstand a wide range of temperatures and pressures. This will help to prevent defects in the final product.
Consideration of the Draft Angle
The draft angle refers to the degree to which the inner wall of a mold can be tapered to enable smooth ejection from the die. It varies depending on the type of alloy and the geometry of the mold.
This is a key consideration because untapped holes are susceptible to shrinkage during the casting process, which could lead to defects in the finished product. It is therefore vital to design the die with a draft angle that is suitable for the particular application.
A good draft angle will also ensure that the parts are pushed out of the die without being damaged. It is possible to determine the ideal draft angle for a specific project by performing a draft angle analysis.
In addition, the draft angle will be influenced by the type of metal that is being cast. For example, aluminum and zinc alloys typically require a higher draft than magnesium.
Aside from these factors, there are other things that can impact the machining and finishing of a die-casting product. For example, the lubricant should be carefully chosen. It should not contain any solvents, as this could cause a chemical reaction that can affect the parts. The lubricant should also be applied in the correct quantity to avoid the formation of scale or other contaminants. It should be water-based to prevent the buildup of minerals that can lead to surface defects.