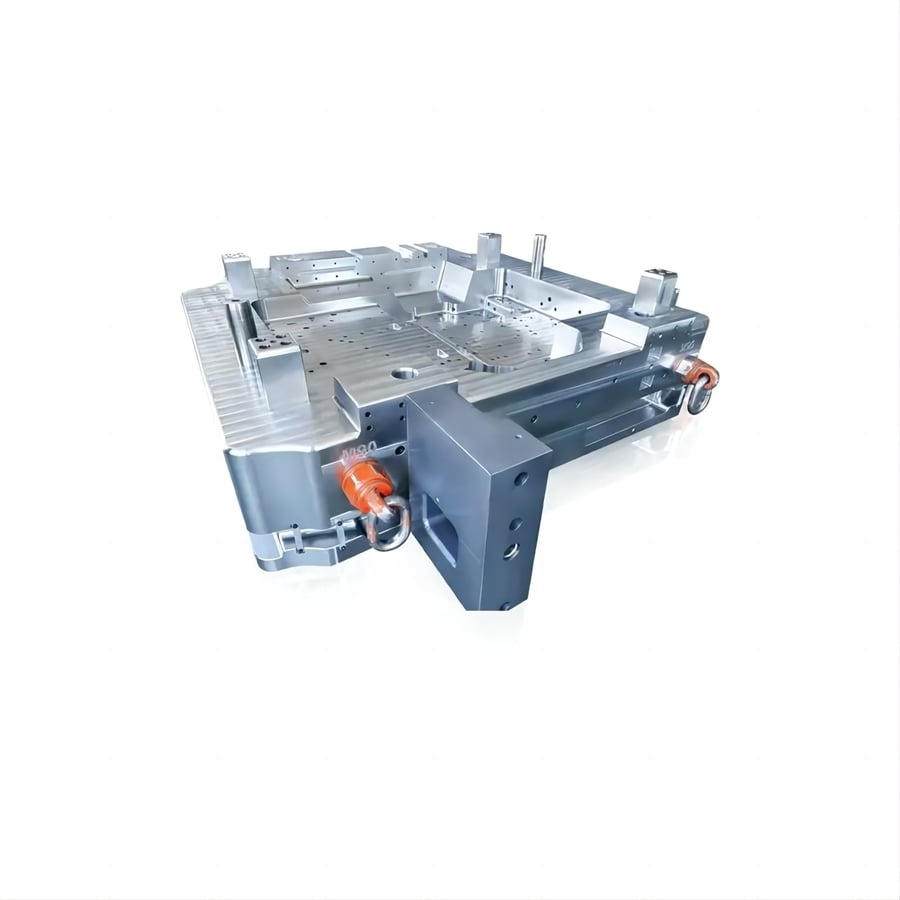
#Industry News
Injection Moulding Is An Important Component Of The New Energy Vehicle Manufacturing Process
Injection Moulding Is An Important Component Of The New Energy Vehicle Manufacturing Process
The New Energy Vehicle Mould Base
New energy vehicles are designed and developed in a different way than traditional cars. They are often constructed of lightweight materials, and use a range of innovative technology and design to reduce weight and make them safer and more durable.
The lightness of these vehicles is achieved by using a variety of different technologies, including lightweight aluminum alloys and composite plastics for the body panels and other parts. The metal used for the inner structure, known as a space frame, is often made from an impact-resistant material called SMC.
SMC is a high-performance plastic with a wide range of thermal, chemical and mechanical properties and cure speeds. Its durability and corrosion resistance makes it an ideal material for the automotive industry.
Compared to other thermoplastics, SMC is generally very low in viscosity, making it easy to fill a mold cavity. Besides, it can be cured at lower temperatures, reducing the need for expensive equipment and the cost of tooling.
Another advantage of SMC is that it can be used to build many different kinds of internal components for an EV. This enables the company to save money on tooling and produce components that are more consistent with a standard production cycle.
Injection moulding is an important component of the new energy vehicle manufacturing process. It is a process wherein a plastic compound is injected into a mold and heated to a specified temperature.
The resulting plastic part is then molded to form a finished product. The molded part is then tested and inspected before it is released to the market.
A variety of methods are used to ensure the quality of the molded parts, and this process can vary widely from company to company. Some methods include coating the surface of the molded parts with an appropriate surface treatment, such as chromium plating, to increase corrosion and wear resistance. Other techniques include using lubrication systems or adding additional support for the mold to prevent premature wear and tear, or using a combination of both.
Some mold manufacturers also provide a variety of maintenance and repair services for their customers, including resurfacing the entire mold to protect against wear and tear, and replacing broken parts. This type of service helps prevent costly repairs and downtime in the future.
This kind of service can be extremely helpful for the car manufacturer, as it allows them to keep their production costs down while increasing the durability and reliability of their products. It is a great way to ensure their customer satisfaction while still meeting their deadlines and delivering a high-quality product.
Mold design is crucial to the success of a molded part. Properly designed and maintained moulds can improve the quality of the molded part, increase its production efficiency and make it more resistant to wear and tear.
Maintaining the Mould Temperature
The temperature of the mould is very important in the molding process. If the temperature is too low, the injected plastics will deform and be difficult to shape. The mould temperature can also affect the injected plastics' flow, shrinkage and hardness.