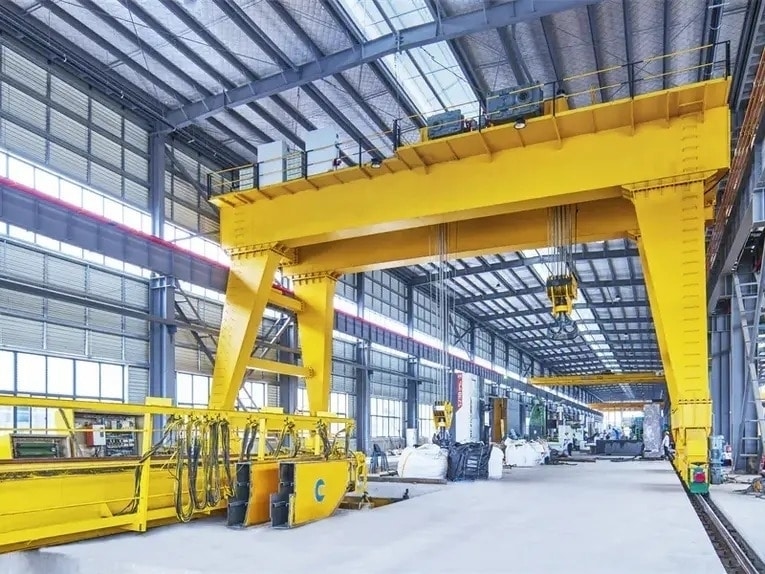
#Industry News
The Huge Impact Of One Piece Die Casting Automotive Mold Case
The Huge Impact Of One Piece Die Casting Automotive Mold Case
Integrated die-casting subverts the traditional car manufacturing process to achieve cost reduction and efficiency increase
1. Integrated die-casting subverts traditional automobile manufacturing methods
The traditional body has many structural parts and complex manufacturing processes, including stamping, welding, painting, and final assembly. The traditional body-in-white consists of 300-500 components, with as many as 4000-6000 welding points. The main car yard purchases stamping and die-casting structural parts from parts suppliers assemble and connect them (including welding, riveting, gluing, etc.), and then welds them with the outer cover parts stamped and manufactured by itself to form a body-in-white assembly.
2. Light weight, higher level of integration, greatly improved production efficiency
Integration simplifies the process and significantly improves production efficiency. The integrated die-casting is highly integrated, eliminating the need for stamping and welding, simplifying the production process, and applying new heat-free alloy materials, eliminating the need for heat treatment, and shortening the manufacturing time of body structural parts from 1-2 hours of the traditional stamping and welding process to 2-3 minutes. Lightweight increases cruising range.
3. Integrated die-casting significantly reduces the cost of the body
With the integrated die-casting aluminum alloy rear floor, the bicycle manufacturing cost is reduced by about 31%. The main equipment of the traditional stamping and welding production line is a punching machine, mold, and welding robot, and the main equipment of integrated die-casting is a die-casting machine and die-casting mold.
Kejia (Changxing) Mold Base Manufacturing Co., Ltd. not only has One piece Die Casting Automotive Mould Case but also Automotive Mould Base and other products, welcome to check our official website.