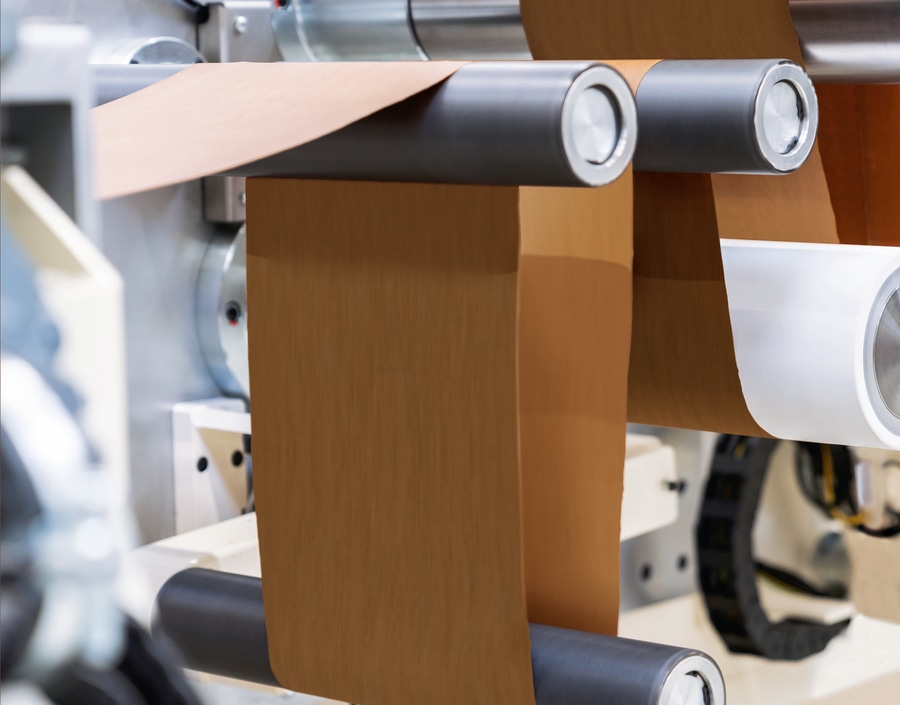
#Industry News
Energy-saving with recon tobacco
TDA stands for tobacco dust amalgamation, a sustainable manufacturing method for recon. The substrate product optimised for tobacco heating products (THP) impresses with its exceptional smoke profile and energy-saving manufacturing.
Manufactured from tobacco dust, recon is primarily used to produce heated tobacco products. In the context of a global increase in demand for recon, our Primary experts in the Körber Business Area Technologies developed a pioneering manufacturing method and brought the associated machine onto the market in 2021.
“The TDA method has several considerable advantages,” declares Alexander Dzingel, Senior Business Development Manager at Körber Business Area Technologies. “In short, these include standardised quality of the highly flavourful products, the small, flexible system footprint and low water and energy consumption during production.”
The conventional method to produce recon is what is known as the slurry or cast-leaf method, during which a tobacco mixture consisting of 80 percent water is poured onto an elongated metal drying belt and spread with a doctor blade. “Large surfaces and a great deal of energy are required for this method: added ingredients such as fibre, glue and, depending on the method, a considerable amount of water are required to produce a sheet made of tobacco dust,” states Dzingel. “To achieve the right amount of moisture in the final product, most of the water required in the mixing process must be evaporated again. “The dryers used devour a significant amount of energy.”
New method for greater sustainability
A suitably more sustainable process is the TDA method for what is known as dough recon, in which the tobacco blend contains 30 percent water instead of the usual 80 percent. “Consequently, 15 times less water needs to be evaporated during the manufacturing process,” explains Dzingel. “With a processing speed of 1,000 kg/h and 2,000 hours per year, using the TDA method saves over six million litres of water and some four million kilowatt hours of energy every year compared to using slurry. In the case of gas, this corresponds to a reduction of 730 tons of carbon per year.”