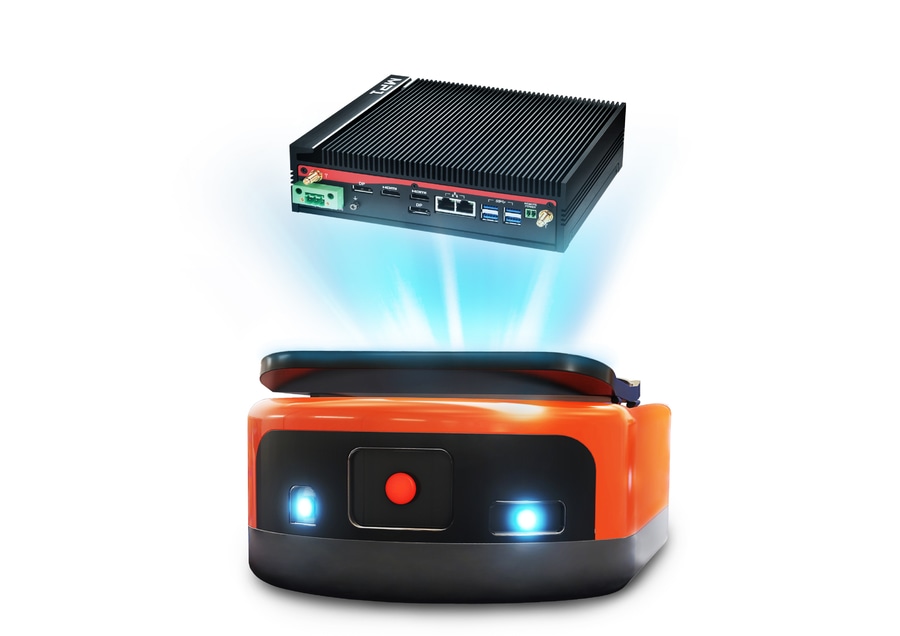
#Industry News
COMPLETE YOUR SMART FACTORY WITH AN AMR
The fanless MP1-11TGS embedded system is a perfect candidate for an AMR
Smart factories are fairly new concepts, but have evolved more in the last decade than in the 50 years prior. First, a smart factory is an advanced manufacturing facility that employs cutting-edge technologies such as the IoT, AI, and automation to optimize the entire production process.
It seamlessly connects machines, devices, and systems to a centralized network, enabling real-time data exchange and analysis. These various connections enhance operational efficiency, quality control, and responsiveness.
To gain intelligence, sensors gather data on equipment performance, production metrics, and environmental conditions, facilitating predictive maintenance and reducing downtime. AI algorithms interpret this data to optimize production scheduling, resource allocation, and process adjustments, improving overall productivity.
Over the past few years, smart factories have undergone a remarkable evolution driven by autonomous mobile robots (AMRs), new vision technologies, and AI. The IoT allows these machines to collect data in real time at speeds not seen before. AI, combined with machine learning, allow for sophisticated predictive and prescriptive analytics, optimizing production processes, and minimizing disruptions.
Edge computing has gained prominence, enabling data processing closer to the source for faster decision-making. Furthermore, 5G technology has begun to revolutionize communication within smart factories, facilitating ultra-low latency and high bandwidth connectivity.
Automation, driven by robotics and intelligent systems, handles repetitive tasks with precision and speed. Known as collaborative robots, or cobots, these systems are becoming more prevalent, enhancing human-robot interaction and flexibility in production lines.
Let the AMR Take Over
AMRs can navigate and perform tasks without the need for continuous human intervention. They integrate various technologies, such as sensors, cameras, lidar, and advanced algorithms to perceive and interpret their surroundings. These robots can autonomously plan paths, avoid obstacles, and make real-time decisions, enabling them to efficiently perform tasks in dynamic environments.
AMRs are being used across various industries, such as manufacturing, warehousing, logistics, and healthcare, to transport goods, perform inspections, and assist in various operations. Unlike human workers, AMRs don’t mind repetitive work, they don’t complain, and they don’t need vacations or sick days, although they do require periodic maintenance.
The AMR is typically comprised of several key components that enable it to navigate and perform tasks independently. Sensors, including cameras, lidar, ultrasonic, and inertial sensors, provide environmental data for perception and obstacle detection. These sensors feed information to onboard processors—powerful CPUs and GPUs—that are responsible for real-time data processing and decision-making. The robot's control system integrates motion planning algorithms that generate feasible paths while avoiding obstacles.
To execute physical tasks, autonomous mobile robots utilize actuators such as wheels, tracks, or legs for movement and manipulation. These components are driven by motor controllers. Communication modules, like Wi-Fi or 5G, facilitate connectivity with central systems or other robots for coordination and data exchange. In addition, the robot's software stack includes navigation software, localization algorithms, and AI components for advanced decision-making and learning.
In general, you can expect to see to see AMRs that move inventory within a facility, that assist in the picking process, and can provide a flexible sortation solution. Specifically, those applications include:
1. automated case and pallet handling
2. automated inspection
3. automated storage and retrieval
4. barcode/QR code reading
5. picking systems
6. robot guidance
7. sortation systems
8. warehouse automation
Embedded Systems Up To the Task
The fanless MP1-11TGS embedded system is a perfect candidate for an AMR. It’s driven by an Intel Tiger Lake-UP3 microprocessor.
A platform such as the MiTAC MP1-11TGS is well suited to drive AMRs in a smart factory. Based on the Intel Tiger Lake-UP3 Core i7/i5/i3/Celeron ULV family of processors and integrated Intel Iris Xe graphics, it exhibits outstanding graphic computing capabilities. There’s support for quadruple displays through HDMI, and as well as DisplayPort. Up to 32 Gbytes of DDR4 memory can be utilized, as well as an SSD/HDD through the hot-swappable slot. I/O is handled with six USB ports and four COM interfaces. Input voltage can range from 8 to 24 V.
The MiTAC MP1-11TGS-D offers similar characteristics, but it’s in a slightly larger package. Hence, it doubles the SSD/HDD support and permits a wider input voltage, from 12 to 36 V. In addition, the platform provides I/O module expansion in both the front and rear, as well as PoE ports for camera connectivity.
Both systems are designed to maximize power efficiency. In addition, each can accommodate an expansion module to greatly increase the I/O support through LAN, PoE, COM, CAN, and other ports.
Smart factories are becoming the best option for many manufacturing and automation facilities. If you’ve already made that decision to move to a smart factory, take a hard look at the MiTAC offerings, which are quite robust. The platforms described here can handle the necessary levels of shock and vibration and operate without fans.