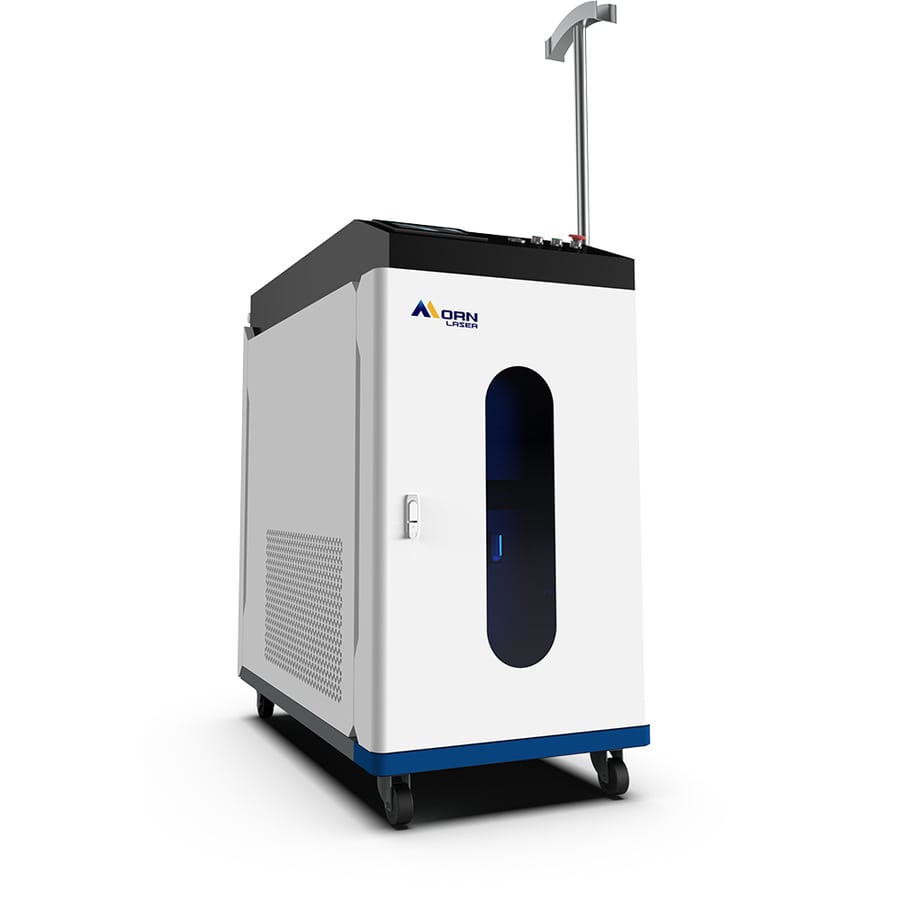
#Product Trends
Advantages of Hand-held Laser Welding Machine
Technological parameters of laser welding
Advantages of handheld laser welding:
1.The heat input can be reduced to the minimum required amount, the metal lographic change range of heat affected zone is small, and the deformation caused by heat conduction is also the lowest.
2.The welding process parameters of 32mm thick single pass welding have passed the verification, which can reduce the time required for thick plate welding and even save the use of filler metal.
3.There is no need to use electrodes, and there is no concern about electrode pollution or damage. And because it does not belong to the contact welding process, the wear and deformation of machines and tools can be minimized.
4.The laser beam is easy to focus, align and be guided by optical instruments. It can be placed at an appropriate distance from the workpiece and can be re-guided between machines or obstacles around the workpiece. Other welding rules cannot be used because of the above space restrictions.
5.The workpiece can be placed in a closed space (under the control of vacuumizing or internal gas environment).
6.The laser beam can be focused in a small area, and small and closely spaced parts can be welded.
7.There is a wide range of weldable materials, and various dissimilar materials can be joined with each other.
8.It is easy to carry out high-speed welding with automation, and can also be controlled by digital or computer.
9.When welding thin materials or small-diameter wires, there will be no trouble of reflow like arc welding.
10, It is not affected by the magnetic field (arc welding and electron beam welding is easy), can accurately align the weldment.
11.two metals with different physical properties (such as different resistances) can be welded
12.No vacuum or radiation protection is required.
13.if welding is done by perforation, the depth-width ratio of weld bead can reach 10:1
14.The device can be switched to transmit the laser beam to multiple workstations.
Technological parameters of laser welding:
(1) power density. Power density is one of the most critical parameters in laser processing. With higher power density, the surface layer can be heated to boiling point in microsecond time, and a large amount of vaporization is produced. Therefore, high power density is beneficial to material removal processing, such as punching, cutting and engraving. For lower power density, it takes several milliseconds for the surface layer temperature to reach the boiling point, and before the surface layer vaporizes, the bottom layer reaches the melting point, which is easy to form good fusion welding. Therefore, in conducting laser welding, the power density ranges from 10 4 to 10 6 W/cm 2.
(2) Laser pulse waveform. Laser pulse waveform is an important problem in laser welding, especially for sheet welding. When the high-intensity laser beam strikes the material surface, 60~98% of the laser energy will be reflected and lost on the metal surface, and the reflectivity will change with the surface temperature. During a laser pulse, the reflectivity of metal changes greatly.
(3) Laser pulse width. Pulse width is one of the important parameters of pulsed laser welding. It is not only an important parameter which is different from material removal and material melting, but also a key parameter which determines the cost and volume of processing equipment.