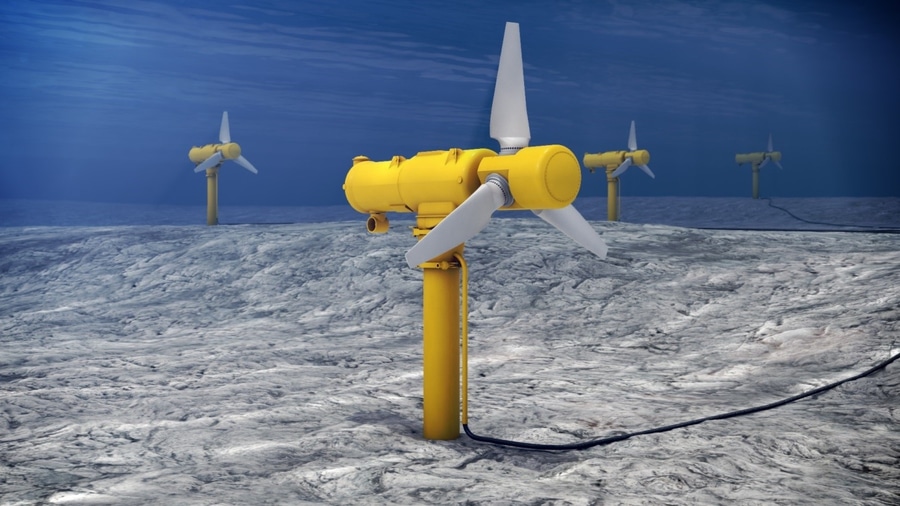
#Industry News
Case Study: GE tidal turbines
Adams simulation helps reduce need for physical testing of tidal turbines
Overview
There are many coastal areas where local geography constrains the movement of ocean tides, resulting in very strong currents. Water is 800 times denser than air so these currents could potentially generate a lot of electricity. GE tidal turbine technology brings proven concepts and industry-leading knowledge to tap into this reliable and predictable energy source. The Oceade* tidal turbine features a buoyant nacelle that enables the turbine to be easily towed to and from the operating site. This eliminates the need for specialist vessels, reducing the cost of installation and maintenance. GE has proven its Oceade* turbine operating at a full 1 Megawatt, injecting over 1.2 GWh of electricity to the grid. This test program has enabled GE to validate the installation and retrieval processes, autonomous running, the performance and power curve of the new turbine.
Challenge
The turbine was originally designed using different simulation software packages linked together to obtain a global view of the system’s interactions with its environment. The primary focus of GE was to precisely quantify and maximize the power produced from tidal currents. Thus GE made efforts to simulate the interaction between the fluid and the turbine at a high level of fidelity. Originally, the powertrain was simply modeled as a high level mass-spring system. However, this approach is not sufficient to study the internal dynamic behavior of drivetrain core components such as backlash in the gearbox, flexibility of the gear teeth and shafts, and friction and play in the bearings. The structure is large and complex so building and testing even a single full scale prototype is costly. GE engineers wanted to make they got the design right the first time and reduce or eliminate the risk of multiple build and test iterations.
Solution/Validation
GE selected Adams multibody simulation tools to predict the dynamic behavior of the turbine. Adams predicts the motion of bodies as does kinematic analysis and also simulates the forces that are responsible for this motion. So, the multibody dynamics model can simulate dynamic loads on various components, vibration, the effects of bodies contacting one another, deflections, etc.
To save time and develop skills in multibody dynamic simulation, GE contracted with MSC to perform dynamic simulation of the tidal turbine design. MSC deployed a multinational team consisting of eight people from France, Germany and Sweden including a bearing expert, a gear expert and a Nastran expert. The team developed an Adams model that incorporates nine flexible bodies including a composite shaft, dynamic models of the gearbox and bearings and interfaces with the turbine control system.
The nine flexible bodies were modeled with MSC Nastran finite element software with some of the models consisting of more than 10,000 nodes. The manufacturer of the composite shaft provided mechanical properties such as the stiffness and inertia of the shaft. MSC consultants modeled the shaft using a Nastran specific composite module and calibrated the model to achieve the correct properties. Nastran was then used to generate a modal neutral file (MNF) that was imported into Adams.
The Adams/Bearing Advanced Technology (AT) toolkit was used to model the bearings. This toolkit saved simulation time by making it possible to model the bearings simply by defining a few geometric parameters and material properties. Bearing AT then created Nastran finite element models of the rolling elements and rings that were added to the system model.
After discussion with GE, a compromise was made between time constraints and model accuracy. The consultants used Adams/Machinery to create the gears. Adams/Machinery gear models can accurately simulate gear backlash and rattle effects. In future projects, MSC consultants plan to use Adams/Gear Advanced Technology (AT) plug to create even more accurate flexible gear models.
The control system was developed internally by GE so the consultants were provided with a Windows dynamic-link library (DLL) file that defined the output of the control system under specific conditions. MSC consultants linked the Adams model to the DLL to co-simulate the Adams model and the control system.
Adams solution provided forces and displacements for every component under each loading condition
GE provided 10 load cases representing different sea conditions and MSC consultants used analytical solutions to estimate the resulting loading on the turbine. The team performed modal analysis of the full structure, steady state analysis under operational conditions, rotating speed ramp up and dynamic force response for each loadcase.
Validation of Adams simulation against results of GE Renewable Energy high level kinematic model
The results were validated against the high level model used to design the turbine and showed good agreement. In addition, Adams multibody dynamics model provided more detailed results about the dynamic of internal components of the turbine. Next, the team validated the modal analysis results with the ones issued from GE Renewable Energy high level model.
Results
The simulation results provided the information to evaluate the dynamic response of the proposed design prior to investing in a physical prototype and testing. Based on the results, GE design assumptions and margins were verified and opportunities for optimization identified. The company is now moving forward to the testing phase confident that the design has been “de-risked” from a dynamic as well as a kinematic standpoint. “This project was a great working experience that allowed the GE team and MSC consultants to share knowledge and gain experience from their own respective expertise,” concluded Valentin Radigois, Lead Engineer, Mechanical-Components, GE Renewable Energy.
About GE Renewable Energy
GE Renewable Energy has made significant investments in the reliable, inexhaustible, and predictable energy source that is tidal power. The company offers complete solutions that work to improve tidal farm economics based on over 10 years of accumulated experience. This includes the successful testing of 500 kW and 1 MW turbines, resulting in over 1.5 GWh of electricity being added to the grid and providing invaluable data to the industry.
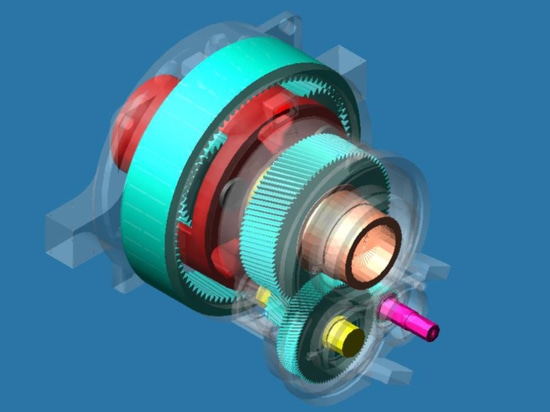
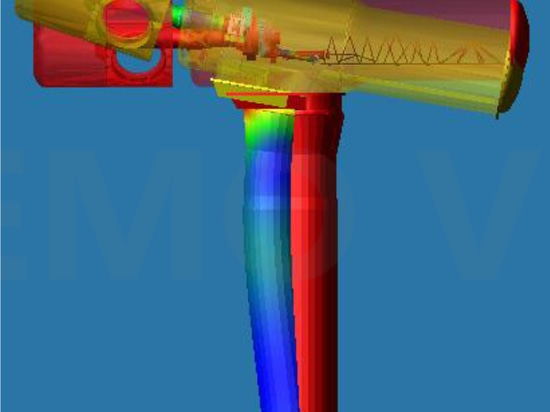
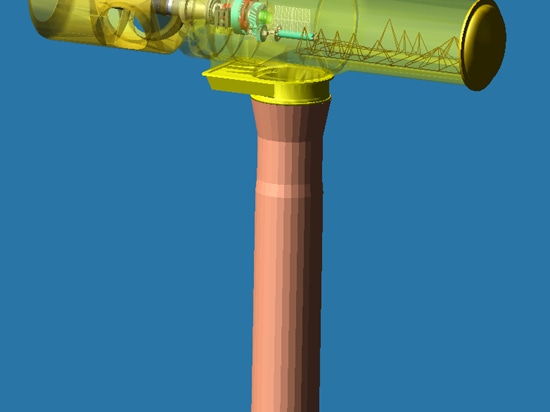