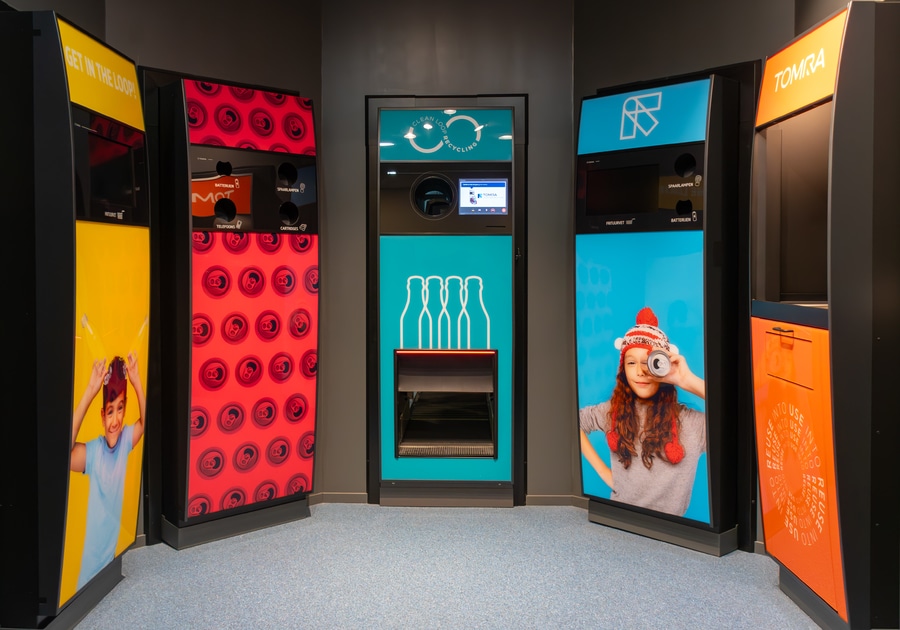
#Industry News
Revolutionising packaging waste reduction
Nidec Drives and the circular economy
The growing volume of packaging waste has evolved into a significant global issue, with estimates showing that up to 91% of this material ends up in landfill or incinerators. This leads to underutilised resources and increased CO2 emissions. A portion of the remaining waste contaminates the environment, contributing to plastic pollution, the degradation of ecosystems, and even entering the food chain in the form of microplastics.
Thankfully, engineers worldwide are developing solutions to combat this crisis. Nidec Drives, a leader in advanced variable speed drive solutions, is playing a key role in tackling these environmental challenges. In Europe, Nidec Drives collaborates with TOMRA, a pioneering company that designs machines to optimise resource recovery.
For over 50 years, Norway-based TOMRA has been at the forefront of global packaging collection. The company’s innovative technology handles the intake, sorting, and processing of empty beverage containers such as bottles and cans. TOMRA’s "Clean Loop Recycling" model facilitates the collection of over 46 billion containers annually. This approach ensures that collected packaging materials are recycled into new packaging, reducing the demand for raw materials and minimising greenhouse gas emissions. TOMRA operates extensively across Europe, particularly in countries with deposit systems for PET bottles, cans, and glass containers. With more than 100,000 installations across 80 global markets, TOMRA is a vital player in the effort to promote sustainability and reduce packaging waste.
How packaging machines work: A behind-the-scenes look
Packaging machines play a vital role in recycling, and their operation can be broken down into two main components. The first part is customer-facing, where users can deposit their empty packaging through an opening. Once placed, the machine scans the packaging and transports it via a conveyor system; often a conveyor belt. The scanning technology identifies the type of packaging and calculates the deposit the customer will receive. After entering their items, the customer can press a button to retrieve a receipt for their deposit. Additionally, they have the option to donate their deposit to charity.
The second part of the machine, known as the backroom, is where the actual processing occurs. This area, located behind the customer interface, collects the empty packaging for further handling. Depending on the machine, the packaging may be temporarily stored for transport, sorted by size and material, or compressed to save space. At TOMRA’s facility in Apeldoorn, Netherlands, the backroom component is assembled and customised for each client’s specific needs and location. This tailored approach ensures that TOMRA’s machines maximise efficiency and adaptability for different environments.
Adapting to the expanding deposit system: Overcoming the can challenge
In April 2023, TOMRA encountered a significant challenge when the Dutch deposit system expanded to include cans in addition to plastic bottles, with the goal of reducing "street waste". The new target aimed to collect 90% of all packaging sold, equating to 900 million small PET bottles and 2.5 billion cans annually.
The expansion of the deposit system in the Netherlands required extensive modifications to the existing recycling infrastructure. Key updates were made to the software to enhance the database, and modifications to the equipment behind the packaging machines were necessary to maintain optimal performance. Some retailers addressed the increased volume by compacting PET bottles and cans. However, for those using two Reverse Vending Machines (RVMs) side by side, TOMRA’s Z-conveyor system became essential.
The Z-conveyor transports uncompressed beverage containers, like PET bottles and cans, into large storage bags. Initially designed to manage smaller volumes (primarily PET bottles) the Z-conveyor faced challenges with the expanded deposit system, which introduced a much higher volume of cans. The original system was not equipped to handle the surge efficiently, risking potential bottlenecks and operational delays.
TOMRA’s conveyor upgrade: Nidec Drives and Duursma delivering efficient solutions
TOMRA needed to adapt its Z-conveyor for handling increased volumes of both PET bottles and cans seamlessly, to allow retailers to cope with the expanded deposit system without disruption. TOMRA consulted Duursma, a Dutch technical wholesaler known for its expertise in variable speed drive technology and industry services such as maintenance, assembly, and support. As a long-standing supplier of components for TOMRA’s machines, Duursma was well-positioned to address the challenge and sought the assistance of partner Nidec Drives. For over 23 years, Duursma and Nidec Drives have collaborated to solve complex technical issues, often utilising Nidec Drives' Control Techniques products – which are renowned for their 50 year tradition of innovation, reliability, and ease of use.
To meet TOMRA’s needs, the original 1-phase motor of the Z-conveyor was replaced with a 3-phase motor combined with the Control Techniques Commander S Micro AC variable speed drive. The Commander S variable speed drive offers power ratings from 0.18 to 4 kW and a maximum output frequency of 300 Hz, which enabled smooth motor control, and making it possible to switch the conveyor motors on and off in a controlled manner; preventing high starting currents and overheating.
This solution allowed for a direct, 1:1 replacement of the old motor without requiring the entire machine to be returned to the manufacturer. The Commander S variable speed drive’s offline programming capability meant that technicians could arrive on-site with a pre-set configuration, simplifying installation. Once the new motor was mounted, only four parameters needed adjustment to get it up and running, offering TOMRA an efficient and reliable solution for the conveyor upgrade.
Why TOMRA chose the Commander S variable speed drive: Durability, innovation, and ease of use
TOMRA’s selection of the Commander S variable speed drive wasn’t just about functionality - it aligned with their commitment to sustainability and durability. The Commander S features a sleek, curved design that minimises its carbon footprint while offering easy access to terminal blocks. Its click-on/click-off DIN rail mounting system ensures a straightforward installation process.
One standout feature of the Commander S is its status as the first frequency inverter to come with standard wireless communication via NFC (Near Field Communication). Unlike Bluetooth or WiFi, NFC provides faster, more stable, and energy-efficient connections within a short range (10 cm), ensuring secure communication. NFC is already widely used in smartphones for tasks like payments, making it both a reliable and proven technology.
What truly set the Commander S apart is the Marshal app, which allows technicians to wirelessly commission, monitor, and diagnose the drive. The app simplifies tasks such as copying and transferring settings between controllers. This feature is particularly beneficial when retrofitting a large number of machines, as any TOMRA mechanic, regardless of electrical expertise, can easily install and program the Commander S with the help of the app. This combination of durability, innovation, and user-friendly features made the Commander S an ideal solution for TOMRA's operational needs.
Collaboration in action: TOMRA, Duursma, and Nidec Drives
Across the Netherlands, the process of replacing the variable speed drives for TOMRA’s Z-conveyors with new frequency-controlled 3-phase motors is well underway. Reflecting on the collaboration between TOMRA, Duursma, and Nidec Drives, this project serves as a textbook example of effective teamwork and innovation. TOMRA is highly satisfied with the swift response from Duursma, who worked closely with Nidec Drives to deliver a timely and reliable solution
Duursma, a key partner in the project, emphasises the strength of their long-standing relationship with Nidec Drives:
"This project is further confirmation for us that in Nidec Drives we have a partner we can rely on. With their extensive knowledge, experience, and range of Control Techniques variable speed drive products, we were able to quickly find the optimal solution for TOMRA".
The success of this collaboration is attributed to the strong communication between Duursma’s engineering team and Nidec Drives, allowing for quick and effective responses to the customer’s needs. The triangular relationship - where both Nidec Drives and Duursma maintain direct contact with TOMRA - proved essential in delivering a customer-specific, innovative solution. This partnership, built on trust and shared goals, has provided TOMRA with an efficient and lasting upgrade for their recycling systems.
Securing the future: The role of variable speed drives in the circular economy
Thanks to the collaboration between Nidec Drives and Duursma, along with the introduction of the Control Techniques Commander S in TOMRA’s Z-conveyor, TOMRA can now offer an efficient solution that helps collection points comply with current laws and regulations.
This innovation allows TOMRA to maintain its pivotal role in the circular economy, making it easier for consumers to return their packaging and contribute to a sustainable future. By streamlining the recycling process, TOMRA continues to support environmental goals, reducing waste, and promoting resource reuse. This partnership not only ensures compliance but also strengthens TOMRA's ability to lead in sustainability and recycling innovation.
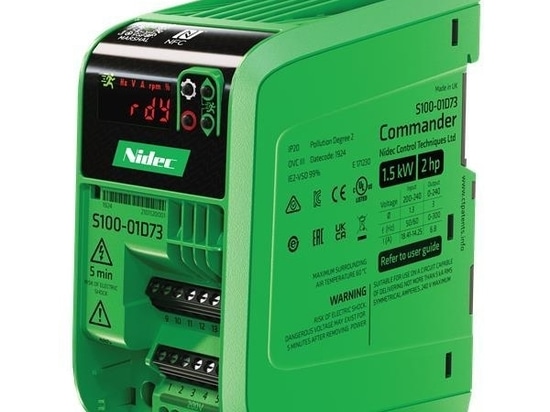