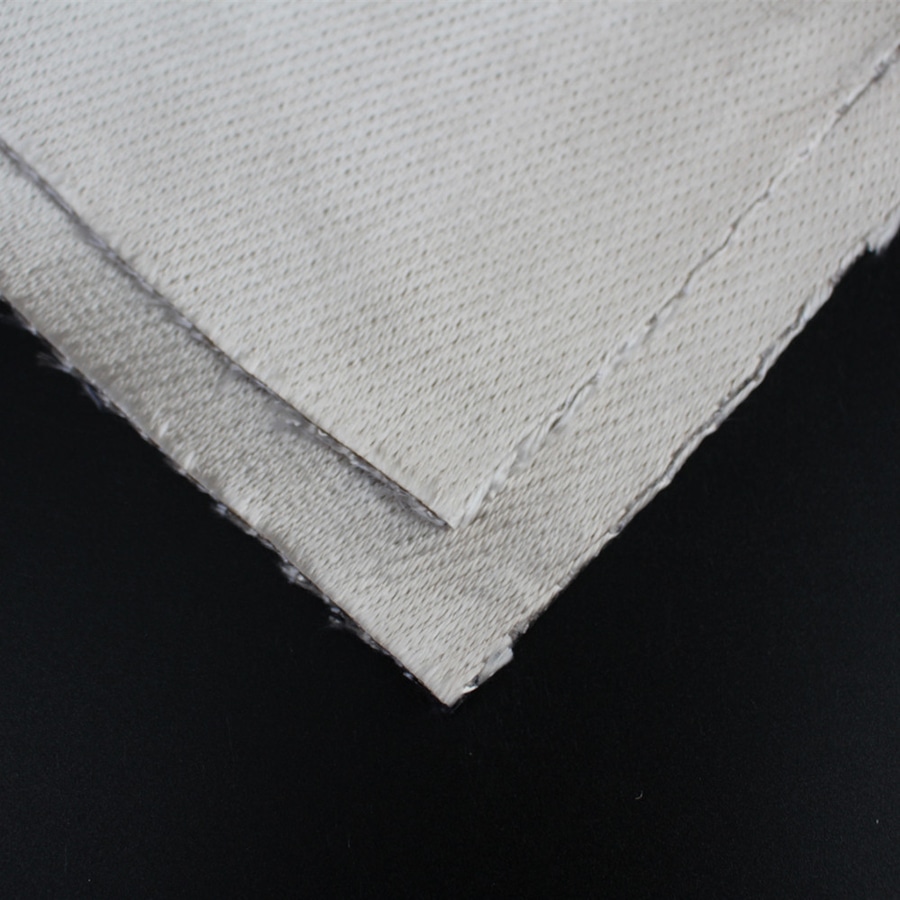
#Product Trends
How Does Woven Silica Fabric Enhance Safety and Efficiency in Extreme Environments?
Woven Silica Fabric
In industries where high heat, flames, and hazardous materials are everyday risks, ensuring safety and efficiency is critical. Woven silica fabric excels in these extreme environments by providing a robust barrier against high-temperature hazards, while simultaneously improving the performance and energy efficiency of industrial systems. Here’s how:
1. Superior Protection Against High-Temperature Hazards
Woven silica fabric offers exceptional protection in environments where exposure to high heat and flames is a constant concern. Its high thermal resistance—capable of withstanding temperatures up to 1,800°F (982°C)—creates a reliable heat barrier that minimizes the risk of burns and fires. This makes it ideal for applications in welding areas, exhaust systems, and industrial furnaces. By insulating workers and equipment from direct contact with extreme heat, woven silica fabric significantly enhances workplace safety.
2. Fire-Resistant and Flame-Retardant Properties
Silica fabric’s natural fire-resistant properties make it a valuable tool in mitigating fire risks. In hazardous environments such as chemical plants or metal smelting facilities, woven silica fabric is used to shield workers and sensitive equipment from the heat generated by flames or molten metal. Whether used as protective wraps for hoses, wires, or components, woven silica fabric helps contain the spread of fire, reducing the likelihood of damage and potential loss.
3. Thermal Insulation to Improve Energy Efficiency
In addition to its safety benefits, woven silica fabric enhances operational efficiency by providing superior thermal insulation. By reducing heat loss in critical systems like exhausts, furnaces, and thermal reactors, silica fabric helps maintain optimal temperatures for processes. This improved insulation leads to better energy efficiency, lowering operational costs and reducing the need for excessive energy consumption to compensate for heat loss. This is especially beneficial in industries such as power generation, automotive, and petrochemical refining.
4. Resilience to Harsh Chemicals and Molten Metals
One of the key advantages of woven silica fabric is its resistance to a range of harsh chemicals, acids, and molten metals. In environments where materials like acid vapors, oils, or molten metal may come into contact with protective materials, silica fabric’s chemical resistance ensures that it maintains its structural integrity and protective properties over time. This makes it ideal for use in chemical processing plants, metal foundries, and other high-risk industries where exposure to corrosive substances is inevitable.
5. Longevity and Reduced Maintenance Needs
Woven silica fabric’s ability to withstand high temperatures, chemical exposure, and physical wear means it requires less frequent replacement compared to other materials. Its durability and resistance to degradation result in longer service life, reducing maintenance needs and operational downtime. This longevity translates into cost savings, making silica fabric a more cost-effective solution for industries with extreme heat or chemical exposure.
6. Real-World Applications
Power Plants: Silica fabric is used to insulate steam pipes and equipment, preventing energy loss while protecting against accidental burns or thermal damage.
Welding and Metalworking: Welders rely on woven silica fabric for personal protective equipment, heat shields, and fire blankets to safeguard against high heat, molten metal splashes, and sparks.
Petrochemical Refineries: Silica fabric is used to protect piping and valves in high-temperature reactors, providing both insulation and resistance to aggressive chemicals, extending equipment lifespan and improving operational safety.