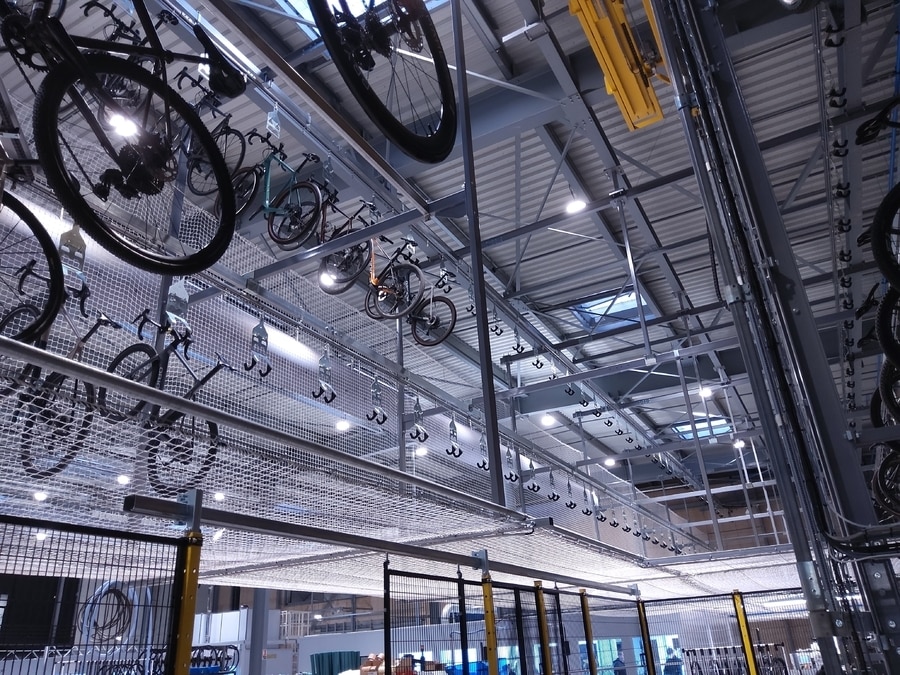
#Industry News
Transporting and storing is as easy as riding a bike!
For the first time in 43 years, OCA has put its expertise at the service of a French bicycle manufacturer.
Whether for ecological or practical reasons, bicycles are all the rage! So when they're also "Made In France", bicycles are often victims of their own success. The 2-wheeled pedal trend has given rise to a number of bicycle manufacturing plants in France. A few months ago, one of them contacted the OCA teams to take up a challenge: optimize the production of its future factory! We explain how OCA is helping to make France a greener place, thanks to its overhead conveyors.
Optimizing production at a bicycle factory with OCA overhead conveyors
For the first time in 43 years, OCA has put its expertise at the service of a French bicycle manufacturer. Having integrated a new warehouse, our customer wanted to include overhead conveyors to store bicycle frames and forks above a painting facility. The bike manufacturer's primary objective was to optimize its production space while ensuring traceability of the parts produced and stored. Secondly, our customer also expressed the wish to store its finished bikes above ground. Storing products assembled and ready for delivery would save time when shipping the bikes, thanks in particular to a process that would enable a precise order to be retrieved via a traceability system.
Transport, storage and tracking with overhead conveyors for improved productivity
Having listened carefully to our customer's wishes, our teams then proposed the integration of 3 overhead conveyors in the bicycle production area:
1 transport conveyor for bicycle parts to be assembled ;
2 storage conveyors for bikes awaiting shipment. One extends over 2 floors and can store up to 126 finished bikes. The other will store a multitude of spare parts (forks and frames) for around 8 different bike ranges.
To achieve this, our teams have designed and created a manual loading and unloading station for the bikes, as well as 2 automatic transfer stations to facilitate the handling and movement of the bikes at the end of the production line to their final storage area.
The entire OCA system communicates with an ERP system, enabling traceability of the various elements stored, and authorizing or refusing unloading.
The challenge was considerable, since our teams had to work to plans, as the premises were still under construction when the transport and storage conveyor project began.
What benefits do transport and storage conveyors offer our bicycle manufacturer?
After months of planning and 12 weeks of assembly, the 5 overhead handling systems for transporting and storing parts were installed on a 516 m2 site. In the end, these overhead transport and storage systems will bring several benefits to our customer:
Saving space in the production area, also securing the circulation space for production operators;
Tracking of parts & bicycles via a traceability system, including in particular monitoring of loading and unloading times, and of the people carrying out the operations;
Prevention of musculoskeletal disorders (MSD) and ergonomic workstations.
All we can do now is wish our customer a successful production! From now on, when you use a bicycle, you'll know that OCA may have contributed to its manufacture!
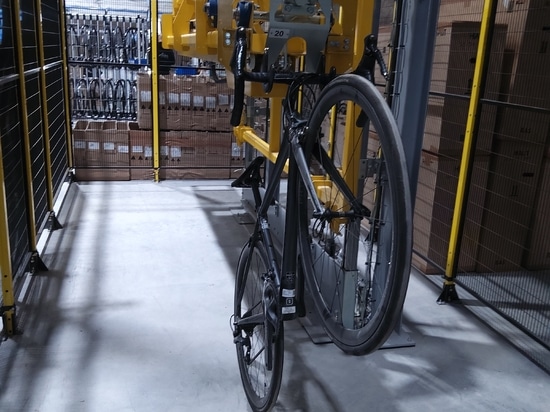
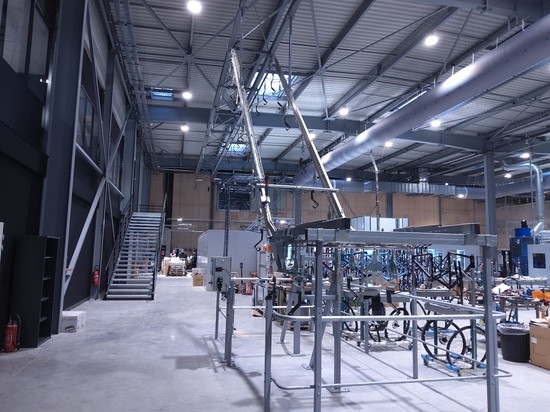
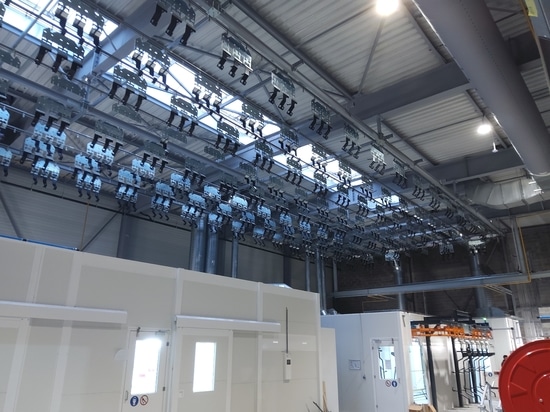