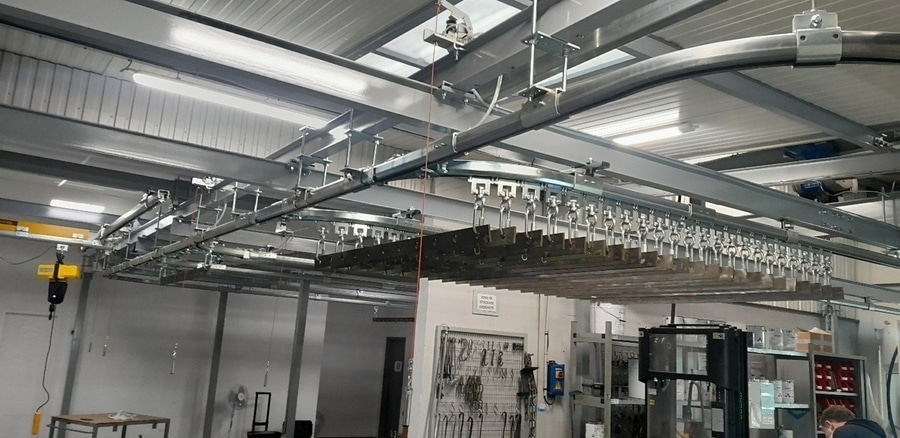
#Industry News
OCA improves the industrial process of a company specializing in surface treatment
The OCA team recently completed a project with a dual objective: to modernize and maximize the production capacities of a major player in the surface treatment industry.
In industry, surface treatment presents many logistical and organizational challenges. Companies must not only ensure optimum quality, but also improve productivity while reducing costs. It was against this backdrop that our OCA experts carried out a tailor-made project for a manufacturer of cooling radiators, with considerable results.
A project with a dual objective: modernize and maximize production capacity
Our customer, a specialist in the manufacture and refurbishment of train radiators, was experiencing significant limitations in its surface treatment process. It had two single rails, designed solely to transport parts (weighing several hundred kilos) to a paint booth. This restricted its production capacity and storage space, both of which were crucial to meeting a growing number of projects. The manufacturer therefore turned to OCA to design an adapted solution to improve the flow of its produced parts and optimize its facilities.
The OCA solution: customized manual overhead handling
To meet this need, OCA designed a manual conveyor for load transfer, incorporating customized elements. Here are the main operations carried out:
- Installation of an overhead crane with hoist: capable of supporting a maximum payload (MPL) of 350 kg, it facilitates the handling of heavy radiators, thus reducing the physical effort required of operators.
- Addition of 5 pneumatic direction-changing modules controlled by pull rods: These devices enable loads to be directed flexibly to different areas (paint booth, oven, drying and storage area), optimizing internal logistics.
- Manufacture and adaptation of lifting beams: 25 new lifting beams were delivered, and 15 old ones were retrofitted to make them compatible with the new OCA rails. This cost-effective approach enabled our customer to minimize costs while modernizing its equipment.
- Installation of around 80 meters of rails: this covered a large part of our customer's production area.
Advantages of the OCA conveyor system
Thanks to its new manual handling system, our customer can see immediate benefits:
- Optimized flows: product radiators circulate more efficiently in the workshop between the various processing stations.
- Productivity gains: operators reduce their handling time and can concentrate on higher value-added tasks. What's more, the OCA conveyor now enables our customer to double or even triple its daily production.
- Cost reduction: the reuse of existing lifting beams has limited investment.
- Optimization of working postures: operators are now protected against the onset of musculoskeletal disorders (MSD), thanks to the OCA handling system, which is at an ergonomic height.
In general, overhead handling systems, such as surface treatment conveyors, offer a flexible solution adapted to industrial constraints. Through this project, OCA demonstrates its know-how in creating customized solutions that sustainably improve its customers' performance, reducing handling times and increasing production capacity.
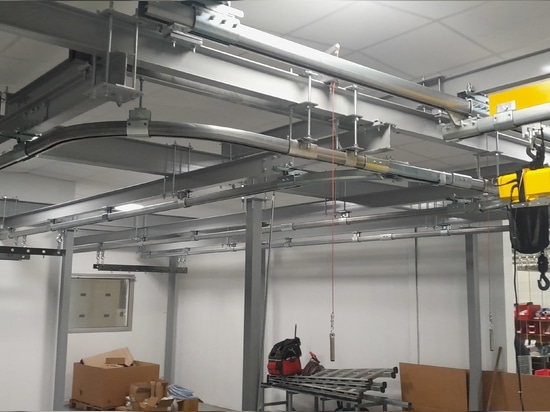
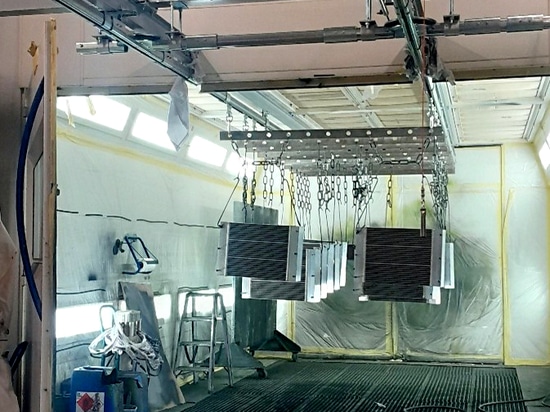