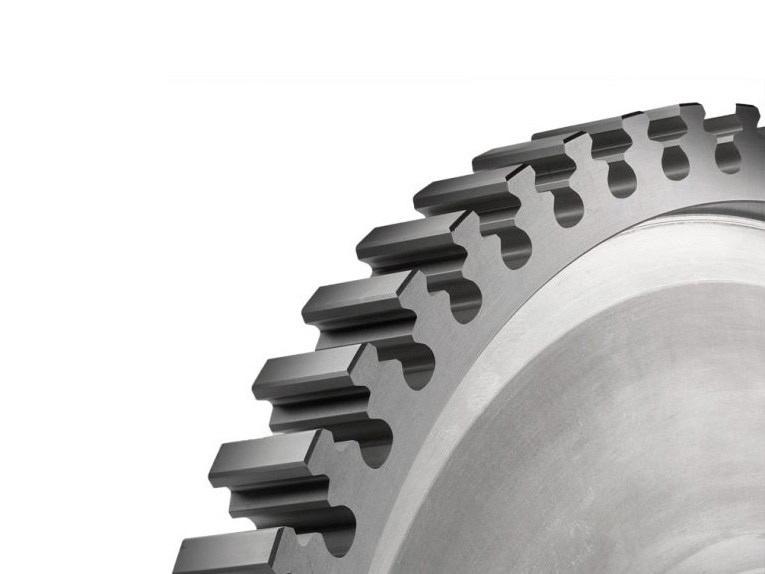
#Product Trends
Wire EDM as a future alternative to firtree profile machining
ONA has carried out a study to analyze a wire electro- erosion process (WEDM) as an alternative to the conventional machining (broaching) of firtree profiles in discs for the aeronautical sector.
\ CASE STUDY EDM TURBINE DISK MANUFACTURING
Being a leader in the EDM sector is only possible through continuous research work on new technologies and applications to provide advanced solutions adapted to clients’ needs. ONA is a clear example of a innovation oriented company which is certified by its 65 years spent delivering technological improvements in electro-erosion. In keeping with this approach, the Basque company has carried out a study to analyze a wire electro- erosion process (WEDM) as an alternative to the conventional machining (broaching) of firtree profiles in discs for the aeronautical sector. In fact, firtree slot WEDM could become a viable industrial option and replace broaching in the future.
\ Assumption and method
In its research, ONA compared the EDM process with more conventional machining like broaching and milling. As key points in the research, ONA compared parameters like surface integrity requirements, precision and processing time of the machining of firtrees.
The test involved cutting a turbine disc with the following characteristics:
• Material: Inconel 718.
• Outside diameter: 350 mm.
• 28 firtree slot profiles.
• Slot profiles at an angle of 30 degrees.
• 82 mm thick.
• Profile tolerance 0.01 mm.
• Firtree radial and angular positioning tolerance 0.08 mm.
The aim of the research was to cut the turbine firtree teeth using WEDM while complying with tolerance requirements in order to analyse the following information:
• Roughing time of the entire profile.
• Finishing time of the entire profile.
• Total erosion time of an entire profile.
• Total roughing time of the turbine disc (including preparation time).
• Total finishing time of the turbine disc (including preparation time).
• Total machining time (including configuration time).
• Material Removal Rate MRR (mm2/min).
• Recast layer thickness.
\ EDM configuration and machining conditions
To carry out the analysis, standard ONA technology was used for nickel alloy, a 2-axis rotary table and two different flushing conditions. On the one hand, good flushing conditions (closed nozzles) and, on the other, worse flushing conditions (open nozzles). In addition, 0.25 coated wire was used for roughing cut.
These two different scenarios chosen for the study (open and closed nozzles) enabled us to carry out different tests to properly evaluate erosion time, as this depends to a great extent on the flushing conditions. It is often the case that, due to the geometrical characteristics of turbine discs, cannot be used closed nozzles.
\ Research results
On completion of the tests, the results showed that you can obtain a recast layer thickness in the necessary micron range (around 5 µm) and with sufficient precision in the firtree profile within a tolerance of 0.01 mm. using WEDM technology. These results were obtained following one roughing pass and two finishing passes (3-cut strategy).
In worse flushing conditions (open nozzles), the material removal rate for roughing was 110 mm2/ min. In fact, for the strategy used in the research (one pass for roughing and two passes for finishing), the material removal rate was 60 mm2/ min.
On the other hand, in good flushing conditions (closed nozzles), a slight improvement in the material removal rate was observed. In the roughing process alone, it reached over 400 mm2/ min.
\ Comments based on the results obtained
Most of turbine discs have firtree profiles at an angle of between 5 and 30 degrees. The taper cutting function of ONA’s WEDM machine obtains good results regarding the geometrical precision for profiles of under 10 degrees. For greater angles, a 2-axis rotary table is recommended.
To remove the required material and improve machining times, the dielectric must be cleaned in the reheating area. It is essential that most of the nozzles are closed in the profile. For turbines discs with a smaller diameter (when the nozzles interfere with the fastening device), special nozzles are recommended.
Lastly, the use of coated wires is recommended to reduce the processing of WEDM, especially in the roughing cut process.
\ Conclusions
Following the research, we can conclude that WEDM machining of turbine disc firtree profiles is an extremely valid alternative to compete with broaching as an industrial solution in the aeronautical sector. State-of-the-art and increasingly powerful generators and more advanced numerical controls allow for the optimization of machining time and the reduction of the white layer thickness. In addition, they achieve very good geometrical precision.
In the study carried out by ONA (3-cut strategy), the machining of turbine disc firtrees meets geometrical tolerances and obtains a white layer of below 5 μm. Additionally, very valuable information is obtained on the material removal rate and machining time.
It is true that the certification of the complete machining process using EDM to standard aerospace standards may be a long and costly process. For this reason, ONA concludes that a better option would be to combine WEDM for roughing, as it is cheaper and quicker, together with broaching for final finishing. Consequently, the process would not need to be re-certified.
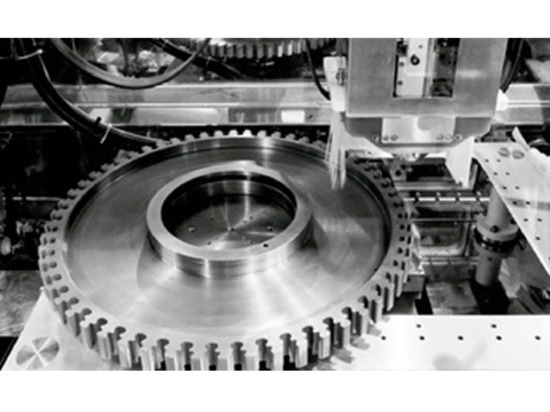