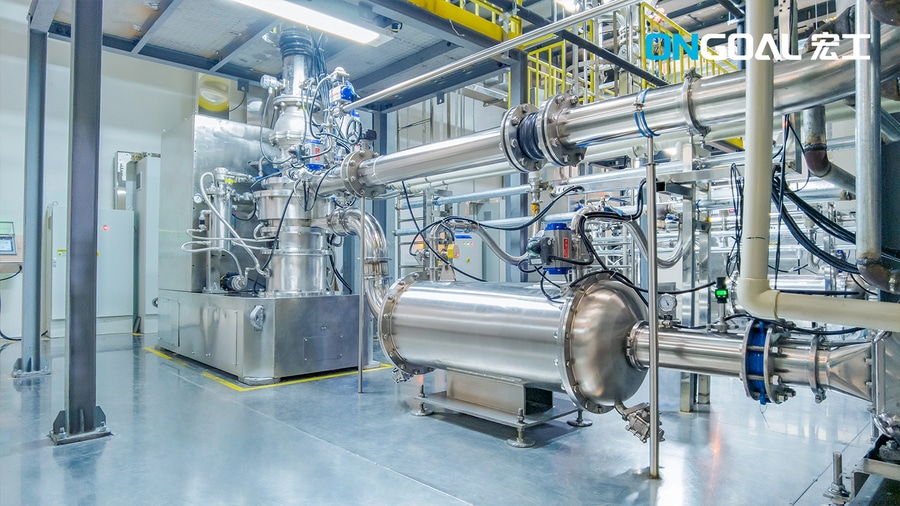
#Industry News
An Effective Mixing for 1600L Lithium Ion Battery Slurry
Lithium battery cell slurry mixing is the mixing and dispersion process in the entire production process of lithium-ion batteries. The quality of the product impact degree of more than 30% is an essential part of the production process.
Recently, a battery batching and mixing project using the circulating slurry mixing process was put into production, for which ONGOAL TECH provided a high efficiency slurry mixing system and a matching dosing and metering conveying system, helping the customer to upgrade the pulping process.
System Benefits
- Operating Costs: Reduced space requirements, much greater compatibility and flexibility, lower overall production costs
- Increased efficiency: The "specific dispersion tray" structure allows for inevitable infiltration and dispersion of the slurry, resulting in a significant increase in efficiency
- Better quality: Better product consistency and higher solids content for high quality battery slurry
- Stable performance: Separate channel design for mixing and dispersing functions solving problems such as discharge blockage and easy overload
Dust free feeding
The main material packed in bulk bags passes through the bulk bag unpacking station and fed into the temporary storage metering silo by negative pressure feeding. The feeding is equipped with a micro-negative pressure to prevent dust lifting and meets the standards of a class 100,000 dust-free workshop
In a separate suction workshop, the auxiliary powder passes through the suction gun. The suction gun is designed with a double-layer structure and has air admission and anti-blocking function.
After dosing, the powder is conveyed to the high efficiency slurry mixing system by negative pressure, gravity drop and other pipeline conveying methods.
Circulating high efficiency slurry mixing process
After metering, all powders and liquids are fed into the production line's "heart" - the high speed dispersion mixer.
The new high efficiency pulping system adopts the powder and liquid feeding at the same time, and the narrow and long path of dispersion chamber makes sure all slurries pass through the effective dispersion zone.
The structure of "specific dispersing plate" make the slurry inevitably enter the full infiltrating and dispersing state. The filling rate of slurry in dispersing area is increased to 100% without foaming and significantly improves slurry mixing efficiency and shortens cycle times. After the slurry discharged, the cycle is repeated between the circulation tanks until the required quality parameter values are reached.
After filtering and removing iron, the mixed slurry is transferred to the finished product tank and conveyed by screw pump to coating transfer tank. It realizes the automatic conveying of finished slurry with no foam and impurities introduced.
The system is equipped with a main line pigging function to achieve automatic pipe cleaning and avoid pipe blocking and cross contamination.
Full process traceability for production management
From the front-end feeding to the back-end slurry conveying, the production control system can realize the integration of production management and process control, with the functions of real-time data collection, data tracing and analysis, real-time equipment monitoring, abnormal automatic alarm, and online tracking of the pigging ball.
Before production, the system can call up the recipe for automatic slurry mixing according to the incoming recipe, generating a pulping report and real-time batching data, and the equipment has a dynamic parameter check function.
The complete system enables efficient slurry mixing and low cost operation and maintenance through a circular slurry mixing process, helping customers to maintain their differentiation in the power cell market.