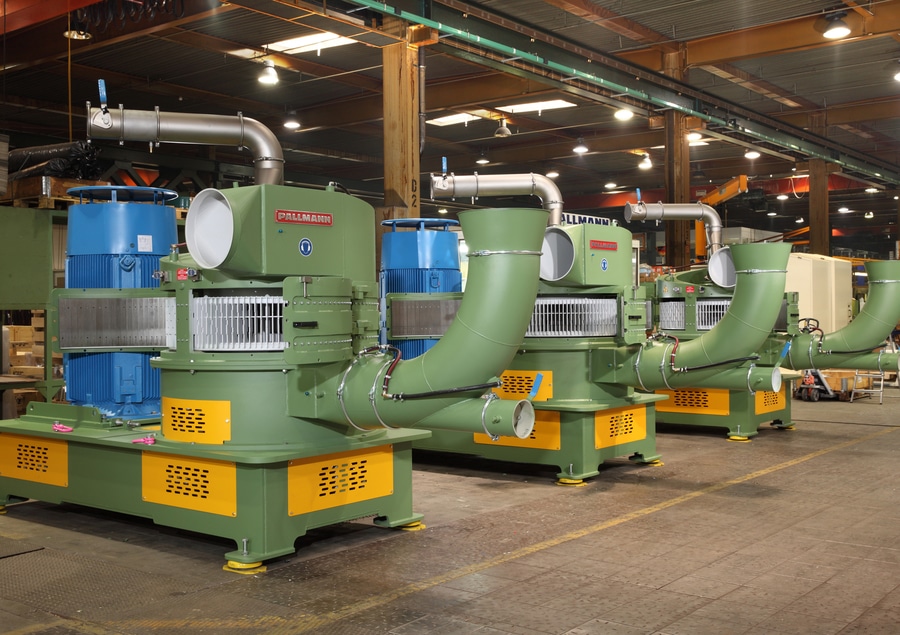
#Industry News
Rubber Powders of Finest Qualities
Turbofiner “LYNX”, type PLMW
More than 3 million tons of waste tires and a considerable amount of rubber waste are ready to be disposed of annually in Europe. More than 30 percent of this amount are meanwhile recycled. This means that they are not burnt but are mechanically processed. Against the background of diminishing raw materials and the increasing impacts on our environment with carbon dioxide, this is definitely the most efficient manner to deal with waste tires.
Mechanical processing, especially the pulverization into finest powders is performed by special machinery. PALLMANN presents the Turbofiner “LYNX”, type PLMW, developed for this application, during the IFAT 2015 in hall C2, booth 117/216. This special pulverization process allows for end product sizing of minus 425 micron. Any rubber tires waste, precut to 2 – 4 mm, or other natural- or synthetic rubber as well as hard to grind or temperature-sensitive products can be used as feed material to be processed.
This achievable, ultra-fine material optimizes the uses of the rubber powder during the production of new tires, as an admixture for insulation boards and rubber products. Besides, it also improves the feel of commodities.
The entire process is performed at ambient temperature. The feed material does not need to be additionally cooled with nitrogen, resulting in the maintenance of the rubber characteristics while achieving greatly decreased processing costs.
The precut material is introduced into the Turbofiner “LYNX”, type PLMW by means of a vibratory feeder or rotary valve. Possible contaminants such as metal pieces are preliminarily separated by means of a solenoid coil or an air sifter. Downstream pulverization is performed in the pulverizing chamber by means of material impact at the grinding path and the reciprocal particle impact in the air whirls behind the beater plates of the high r.p.m rotor. The newly developed beater plate geometry and the high circumferential speed of the rotor in the Turbofiner allow for final particle sizes that have not been achieved with traditional ambient grinding processes. The maximum achievable or desired end product sizing fineness can be determined by selection of the suitable grinding track profile. An adaption to other materials or fineness is also possible at any time. After the pulverization process, the material is pneumatically suctioned and transported into a downstream filter which separates the powder according to particle size. Material that does not correspond to the desired end fineness is automatically reintroduced into the pulverization process.