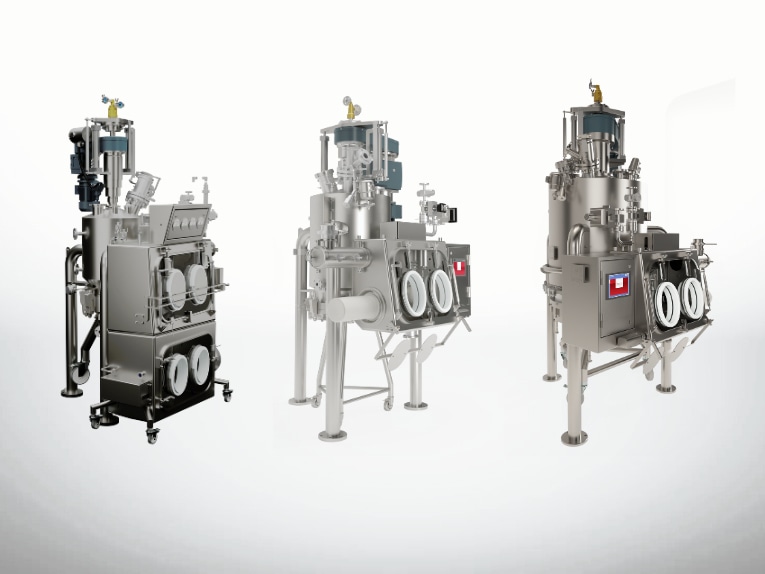
#Industry News
How Agitated Nutsche Filter Dryers Work
The Nutsche Filtration and Drying Process Explained
Agitated Nutsche Filter Dryers (ANFD) are regularly used in pharmaceutical and fine chemical manufacturing. These versatile machines serve multiple industrial purposes, though their primary use is for filtering Active Pharmaceutical Ingredients (APIs) after crystallization. But how exactly does agitated nutsche filtration operate?
Agitated Nutsche Filtration and Drying (ANFD) plays a vital role in isolating solids during batch processing. While there are various methods for recovering Active Pharmaceutical Ingredients (APIs) from slurry, the unique advantage of ANFD systems lies in their ability to combine slurry filtration, product washing, and vacuum drying into a single unit.
Earlier versions of this technique used open vessels for separating solids from liquids via suction. However, modern enclosed designs, developed in the 1960s, improved the process significantly. These newer systems incorporate pressure and agitation, offering better process control and enabling the handling of highly potent compounds that require strict Occupational Exposure Limits (OELs).
Agitated Nutsche Filter Dryers generally consist of five main components:
1. Jacketed Pressure Vessel - Allows positive pressure or low vacuum with high sealing efficiency.
2. Bi-directional Agitator - Features an adjustable stroke, where each direction offers a different effect on the product.
3. Base Filtration Element - Available in various configurations and pore sizes to fit different product profiles.
4. Heating Elements - Control the process temperature, either heating or cooling.
5. Discharge Plug/Valve - Must be designed to maximise product recovery yield.
Additional components, such as bayonet plugs for quicker maintenance, integrated cameras for method control, and dust filters to contain highly active ingredients, are also available to enhance performance.
Initiating Filtration
The filtration process begins when the slurry is introduced into the vessel, either in bulk or gradually. Agitation typically starts after this step, with the agitator's blades performing a low-speed, high-torque mixing action near the filter media. This ensures the cake height does not impede filtration. Gas pressure is then applied, and the solid-liquid separation begins. As filtration progresses, the agitator blades rise to the top of the product cake to smooth out cracks or preferential channels, accelerating the filtration rate compared to gravity-based methods.
Slurry Washing
After API crystals are separated, any remaining filtrate and impurities must be removed via washing. In a traditional wash, solvent seeps through the product cake to remove residual traces of impurities, often requiring multiple cycles for optimal results.
In contrast, in a re-slurry wash solids are re-suspended by using the agitator to plough the solvent into the cake. This approach increases the contact between solid surfaces and solvent, reducing the overall solvent volume needed to achieve the same level of purity. After washing, any persistent liquid is pressure-filtered from the system.
Drying
Once washing is complete, drying begins. This can be achieved through either pressurised gas heating or vacuum-assisted heating, both of which rely on optimal heat transfer within the vessel. Heat transfer media is typically applied to the vessel’s sidewalls, filter base, and agitator blades to ensure effective drying.
The agitator continues to provide gentle mixing, ensuring uniform drying. Vertical homogeneity is maintained by raising and lowering the agitator, and more challenging products can be handled by reversing the agitator’s direction when necessary. Temperature-controlled zones within the vessel can be cooled at the end of the process to safely lower the product temperature before discharge.
Convective drying, when done effectively, can significantly shorten the drying time and improve process efficiency.
Dispensing the Product
In the final stage, the agitator pushes the dried product cake toward the vessel wall and discharge plug. A funnel is typically used to optimise packing, while an additional product rake can be employed for maximum product recovery from the vessel (heel recovery).
Looking for More Information on Agitated Nutsche Filter Dryers?
Interested in learning more about Agitated Nutsche Filter Dryers or have specific requirements? Contact a member of the Powder Systems team today for expert guidance and solutions meet to your needs. Let us help you optimise your filtration and drying processes!