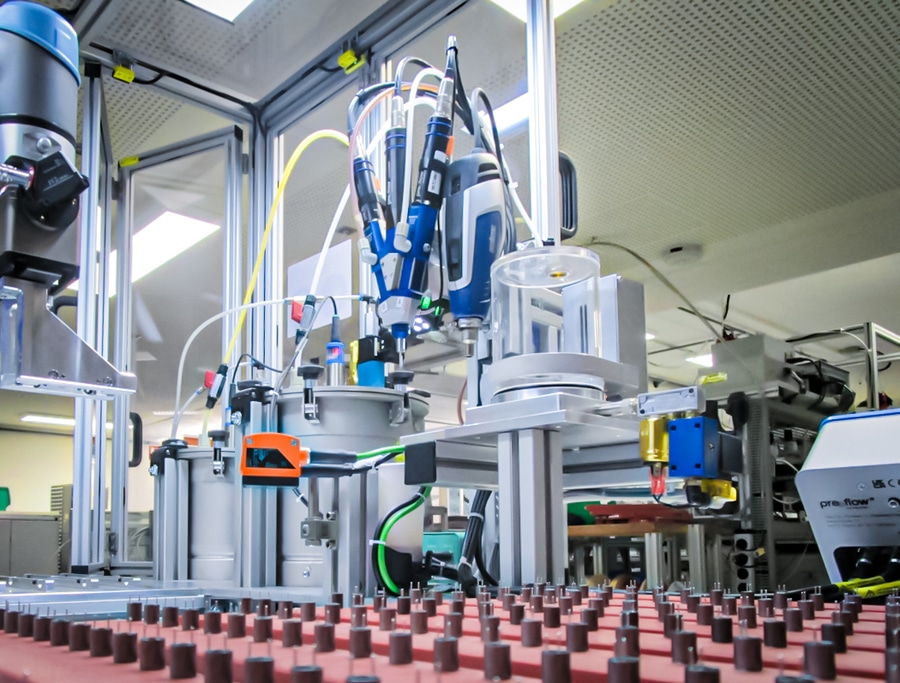
#Industry News
Challenge: Clean pins for micro solenoid valves
How Staiger is improving quality in a potting process with 2-component media
• eco-DUOMIX in use at Staiger for automated dosing of a 2-component potting compound from Henkel
• Collaboration has led to important insights regarding the further development of the eco-CONTROL EC200 2.0
• Staiger benefits from improved process and processing stability, as well as occupational safety
Pins in particular are critical to parts and components during potting processes. If the miniature contacts become contaminated with glue, the electrical conductivity suffers, along with the component quality.
Staiger – a company based in Erligheim in the German state of Baden-Württemberg – has automated the potting of 2-component adhesives in magnetic heads for solenoid valves, in order to reliably prevent this issue from occurring in the manufacturing of micro solenoid valves of just 7 mm in size, and to also ensure that exactly the same filling heights are always achieved. "Up until now, we've been mixing the material by hand and then also dosing it into pallets manually," explains Stefan Waldinsperger, the department head for operational and test equipment construction and process development at Staiger. Although the manual potting performed by the four highly trained employees responsible for this process was of an acceptable quality, it nevertheless proved too monotonous to handle for manufacturing quantities of between 600 and 800 units per shift. The increasing difficulties in finding suitably qualified personnel, along with the consistent precision guaranteed by robotics, ultimately drove the decision to automate the process instead.
Initial tests were carried out with the eco-DUO from preeflow, which Staiger procured via an authorized preeflow sales partner. Over the course of these tests, it then became clear that the two components of the Henkel potting compound used are only suitable for static mixing in the eco-DUO under certain conditions. "The 2-component material poses challenges for mixing and dosing," explains Waldinsperger. For this reason, he got in touch directly with preeflow, a provider of microdosing solutions. His objective: To discuss alternative technical solutions to the challenge faced by his company. In particular, this concerned the very small design of the solenoid valves and the associated wish to have a precise dosing system that can handle very small quantities. At the same time, the technology needed to be suitable for the challenging material properties of the 2-component potting compound. Waldinsperger explains it as follows: "The hardener is of very low viscosity – it hardens quickly even as an individual component and must therefore be processed swiftly. All of this has an impact on the process."
Over the course of joint discussions, the responsible parties evaluated the technical requirements and suitable technologies and decided on the eco-DUOMIX. The greatest advantage over the eco-DUO is that the eco-DUOMIX implements the mixing dynamically using a high-torque engine. Particularly for complex media of varying viscosities, this increases the process stability and consequently has an impact on the processing quality.
By chance, preeflow happened to be developing the eco-CONTROL EC200 2.0 control unit in parallel to the Staiger project. As a manufacturer of valves, Staiger also possesses the relevant expertise in control systems to be able to reliably integrate processes into series production. Consequently, the company proved a beneficial consultation partner for the developers of the DUOMIX feature within the new eco-CONTROL EC200 2.0 control unit from preeflow. "We have a number of renowned major clients that have enormously high expectations in terms of quality. For us as a supplier, therefore, it's always an advantage when we're able to sample a great number of parameters that are relevant for process monitoring," Waldinsperger explains of his everyday work. ViscoTec swiftly took on board the feedback from Staiger and modified the eco-CONTROL EC200 2.0 stage by stage. To name just one improvement, it's now possible to record data even on the operating status of the third engine responsible for the mixing, for example. "The collaboration with Staiger at that time proved fortunate for the new development of the eco-CONTROL EC200 2.0," remarks Thomas Schmid, business area manager at preeflow. Stefan Waldinsperger agrees, although for a different reason: "Our employees are particularly happy that the manual mixing of the two components is now largely done automatically in the eco-DUOMIX, and that maintenance is a simple matter of filling the tanks with the Henkel material. It means there's less direct contact with the material, and that's naturally great from a health and safety perspective."