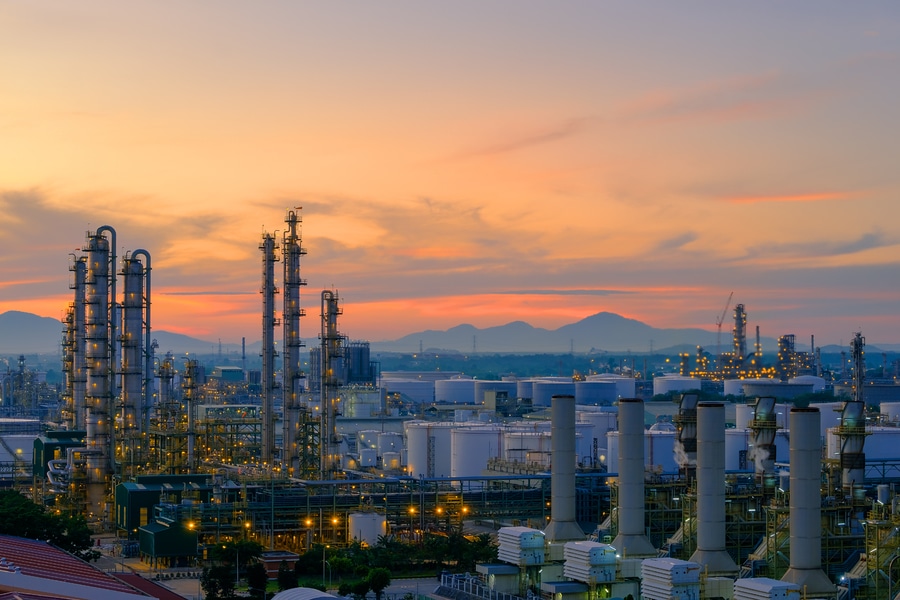
#Product Trends
Oxygen measurement in natural gas
How to identify oxygen contamination in natural gas
Oxygen has many properties. It is vital to sustain life, essential for the environment, supports combustion and acts as a catalyst in many industrial and biological reactions and processes. Yet, when it comes to processing and transporting natural gas, oxygen is considered to be an unwanted and potentially dangerous contaminant.
Oxygen can enter the natural gas train at various stages. Most frequently, oxygen will enter pipelines and distribution systems through leaks in pipes, valves and other equipment. It’s worth noting that even if the pipeline gas pressure is significantly higher than that of the external environment, oxygen will still ingress though a leak in pipework. This is due to the different vapor pressures between the gas in the pipe and the surrounding air. For example, pipeline gas pressurized to 1,000 psig may typically have an oxygen content that is less than 200 ppmV; the latter will have a vapor pressure of 10.5 mmHg. By comparison, the vapor pressure of oxygen in air is around 157 mmHg. This represents a differential pressure ratio of nearly 15:1, which, even with an escaping gas pressure of 1,000 psig, is sufficient to cause oxygen to leech back into the pipe.
Oxygen can also be drawn into the natural gas processing and transmission network by faulty equipment, due to incorrect purging after systems have been shut down for maintenance or vacuum extraction processes. The latter are increasingly being used to extract as much natural gas as possible from depleted reservoirs but can also draw in excessive oxygen through either existing leakage points or compressor inlets.
The presence of oxygen in natural gas can create a number of issues:
Corrosion: oxygen can combine with moisture to attack metal surfaces; research carried out by a major gas transmission company identified dissolved oxygen as ‘one of the more corrosive contaminants in natural gas’.
Safety: either where excessive corrosion results in gas leaks, or where oxygen combines with other gases to increase the risk of explosion.
Reduction in production efficiency: oxygen can degrade additives such as amines, which inhibit their ability to remove CO2 and H2S and affect the properties of some mercaptans, which reduces the effectiveness of these odorants.
Contractual compliance: oxygen contamination can cause the quality of natural gas to exceed contractual specification, leading to potential penalties for transmission and supply operators.
Oxygen measurement in natural gas: best practice
Clearly, given the potential impact that oxygen contamination can have on the safety, quality and operating cost of natural gas systems, the use of highly accurate and reliable oxygen monitoring instruments is critical.
There are a number of technologies used for detecting and measuring oxygen concentrations in natural gas. These include gas chromatography, coulometric sensors, parametric oxygen cells, fluorescence quenching and galvanic fuel cells. Although each has its advantages and disadvantages, one of the best solutions is to use a specialized sensor based on a galvanic electrochemical cell that is then connected to an advanced process monitor. For example, the combination of our Minox-i intrinsically safe oxygen transmitter, combined with our latest multichannel process monitor, allows oxygen concentrations down to 1 ppmV in natural gas to be easily detected with fast response times and exceptionally high levels of repeatability.
The Minox-i uses a stable, long-life galvanic electrochemical cell. This is constructed from four layers: a gas permeable membrane, an anode manufactured with a high concentration of gold, an electrolyte, and a lead-based cathode. The complete assembly is contained with on-board electronics in a compact stainless-steel housing.
The sensor works by passing a gas sample over the high-concentration gold anode, where oxygen reacts to form hydroxyl ions. These then diffuse through the electrolytic membrane to the cathode, where they oxidize to become lead oxide. This reaction produces a voltage, which is directly proportional to the concentration of oxygen in the gas mixture. The voltage is then processed by the system electronics to give a 4…20 mA output signal, which can be used to accurately calculate the trace level of oxygen in the sample.
Real-time oxygen monitoring
The output signal from the Minox-i, as well as that from other process sensors, should ideally be fed to a dedicated process monitor, such as the latest Michell Instruments Multi-Channel Process Monitor (MCPM). This six-channel instrument features a large color touch-screen LCD, making it simple to configure and use, and providing real-time display of multiple process parameters.
The new MCPM allows NAMUR 102 standard process alarms to be set, provides full data logging, plus comprehensive connection options, including RS485 and Ethernet for Modbus TCP/IP. By using the technology described above, natural gas producers and transport operators have access to vital real-time data that will ensure process and distribution systems function safely, efficiently and profitably.
We are the world’s leading experts in specialized gas, moisture monitoring and dew-point measurement. We have an extensive range of products, backed by unrivalled technical and customer support. To learn more, talk to one of our application specialists today.