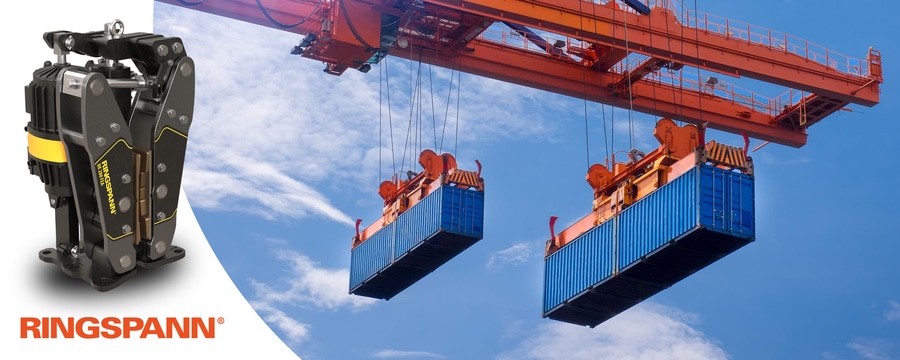
#Product Trends
Innovative braking and emergency stop solution for heavy-duty cranes
Extremely fast and without damaging flank changes
Bad Homburg, March 2024. – “Our two new developments in the field of brake technology have what it takes to revolutionise the design of heavy-duty hoists for use in industrial and harbour cranes," says Martin Ohler, Business Developer Brakes at RINGSPANN. He leaves no doubt about the importance of his division’s latest innovations. And if you look closely, it actually turns out that he could be right. Because what the brake technology specialists of the German company have come up with this time starts exactly where many hoist designers have problems: coping with the enormously high dynamic forces to which the trend towards ever faster and more efficient drive systems forces them. At the same time, the innovations are astonishing due to their simplicity, which is shown by the fact that their use does not require a complete replacement of existing disc or drum brakes from RINGSPANN. "From the very beginning, our aim was to provide retrofittable solutions for the safe control of the ever-increasing energy pulses in crane construction, which score points with high availability and MRO affinity and also improve the performance of the hoists," emphasises Martin Ohler. He and his team have achieved these goals through two crucial new developments: First, a thruster that gives the electrohydraulic brakes of the DX, DS and DT series from RINGSPANN (https://www.ringspann.de/en/products/brakes/electrohydraulic-brakes) mounted on the motor side of the hoists exceptionally short closing times. And secondly, a control unit that significantly increases the service life of the hoist gearboxes.
The extremely short, above-average fast and flexibly adjustable closing times of the new thruster are the result of a benchmark in which the RINGSPANN engineers compared the effects of different pump types on the closing process of the hoist brakes used on the motor side. This showed that the use of a special gear pump could significantly reduce the volume of oil that has to be displaced during closing. "This gives the brake a dynamic that was previously hard to imagine. We were able to measure closing times of less than 0.08 seconds," reports Martin Ohler. In addition to the fact that the low oil consumption, and the fact that the brake switches to a low-power depressurised mode after opening together reduce the operating costs of the hoist – and minimise its ecological footprint – the responsiveness and flexibility of the brake result in far-reaching functional, safety and maintenance advantages for the drive unit.
In particular, one aspect should be mentioned here that has repeatedly caused major problems for hoist designers to date: since the new thruster from RINGSPANN offers the possibility of varying the closing times, it can be used to eliminate tooth flank changes in the hoist gearbox. Martin Ohler explains: "Tooth flank changes always occur when braking is first on the ’wrong’ side. When lifting, the braking effect must first set in on the transmission side, as the driving force is the engine. In lowering, on the other hand, the driving force is the crane hook with the load. Since the engine only follows this force, it is necessary to brake on this side first. By varying the closing time, it can be ensured that the brakes are always applied in time on the opposite side of the driving force, so that the pairs of teeth remain in close contact at all times and cannot hit each other." Regardless of the direction of travel, the gearbox between the drive motor on the one hand and the winch on the other side is relieved in such a way that a harmful flank change of its gears is ruled out. This prevents the formation of cracks and pitting on the contact surfaces of the gear pairs, reduces downtime due to repairs and gives the gearbox a significantly longer service life. Other positive effects include reducing the operating noise of the hoist and avoiding harmful vibrations.
The effect of the second brake technology innovation from RINGSPANN – a new control unit – also leads to important relief. This is because it makes it possible to pre-select the emergency holding brakes used in the hoist via several valves and thus adapt the required braking forces to the driving speed and load. The user can set two different closing times in order to optimally adjust the safety factor of the emergency stop and service brakes to the actual driving conditions. "The result is a reduction in load peaks on the entire crane structure – especially the bearings and gears," says Martin Ohler.
Both braking innovations from RINGSPANN are extremely easy to integrate for the user. Thus, the new thruster is a compact, relatively light, maintenance-friendly and purely analogue unit without electronic components (circuit boards). It can be put in place of the previous thruster in just a few simple steps and almost all further adjustment and maintenance work on it can be carried out without removing it from the brake. Another great advantage is that many brakes of different sizes can be equipped with just a few thruster versions. The resulting reduction in variants simplifies spare parts management, makes it easier for the user to acquire know-how for all MRO work and minimises the expense required for warehousing.
It’s a similar story with the new control system. It consists entirely of components from the RINGSPANN one-stop shop and can be used quickly by making small modifications to the thruster. In addition, it is a hard-wired solution that meets the highest safety standards and can also be easily replaced or retrofitted. "The requirements for the customer’s data interface are simple, because our new control unit only needs a single signal: is the hoist running in lowering or lifting mode?" says Martin Ohler.
With its new all-in-one solution consisting of a high-speed thruster and intelligent control system, RINGSPANN offers designers of hoists and hoists for container, harbour and industrial cranes a braking innovation that enables them to create considerable added value for their customers. This is because hoists equipped with them will work more efficiently, cost-saving, resource-saving and safer than previous units. They meet the growing performance and quality requirements in modern crane construction and offer considerable competitive advantages.
Discover our latest electro-hydraulic brakes DX 280 FEA: https://www.ringspann.de/de/produkte/bremsen/elektrohydraulische-bremsen/federbetaetigt-elektrohydraulisch-gelueftet/dx-280-fea
Find out more about the benefits of this product innovation: https://youtu.be/SkIJSZzAGHw
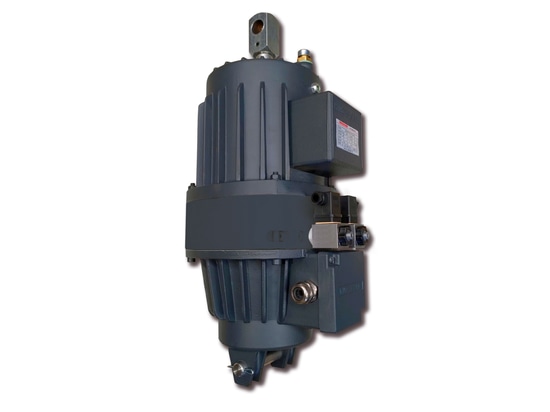
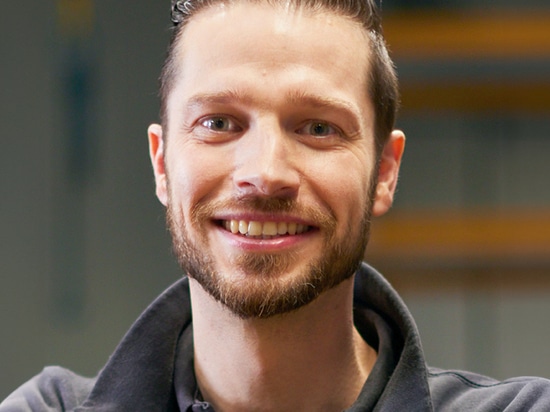
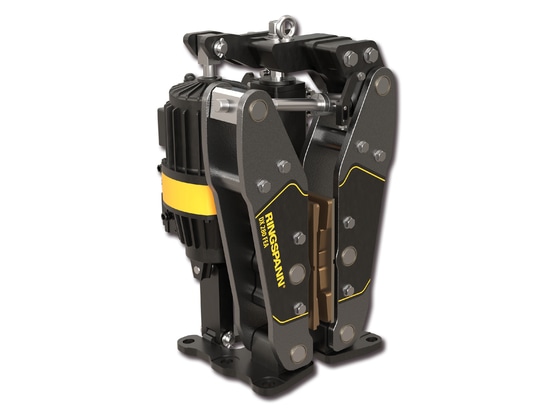