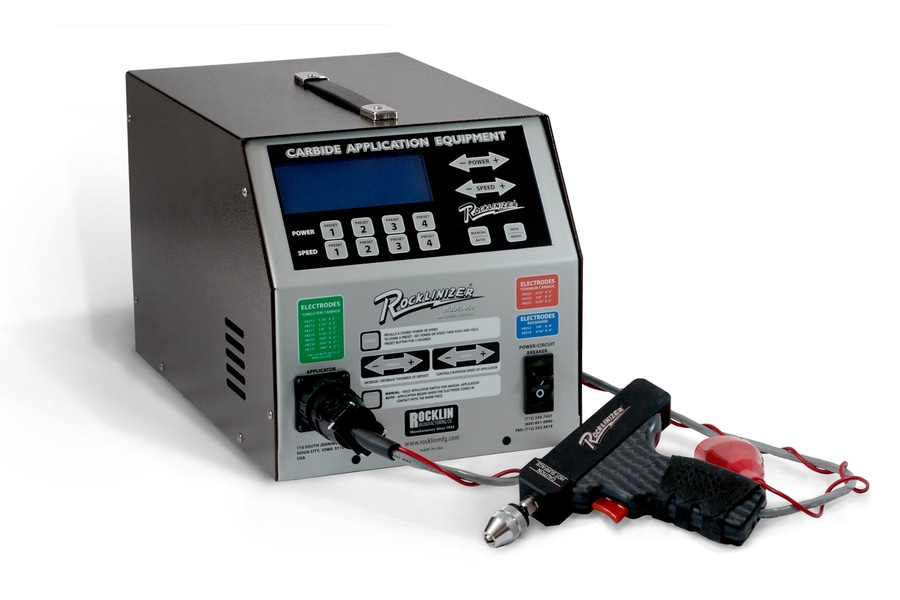
#Product Trends
10 Applications to Extend the Life of Your Tools & Dies
The Rocklinizer Carbide Application Equipment
What if you could prolong purchasing of tools and dies by several months or even years? What if you could buy your expensive molds and dies once every three years instead of annually? And what if at the same time you could improve maintenance and slash downtime?
These cost and time savings are surprisingly achievable by using the Rocklinizer Carbide Application Equipment. By applying a hard and wear resistant surface to metals, tools and dies, you can protect your tools and dies against wear, restore tolerances, and also enhance gripping.
The ROCKLINIZER Carbide Application Equipment does just that, extending the useful life of customers’ tools and dies. It works by quickly and accurately depositing wear resistant carbide material on top of and underneath metal surfaces. The user can deposit from .0001” up to .010” and higher, all controllable within .0001”. With the Rockhard (~60 Rockwell C), tungsten carbide (~70 Rockwell C), or titanium carbide (~80 Rockwell C) electrode options, the user can significantly increase surface hardness to protect against costly wear.
When might this be applicable? The range of applications is quite broad, but here are ten examples to consider directly from satisfied ROCKLINIZER customers:
“...in the past we have had problems with slugs ‘pulling’ and not ejecting properly. With a couple of well-placed touches with the tungsten carbide, the problem goes away, and we have noticed increased die life.”
“...to coat the HSS drills and reamers used in drilling cast iron. Our tool life improved 3 to 1 for drills, and approximately 6 to 1 for reamers...Now we use the Rocklinizer to coat milling cutters, spotfacers, taps, punches, and dies.”
“Our clamping jaws and punches get 2 to 3 times the life.”
“On some of our lathe operations where we once machined five pieces per tool bit we can now produce 25 and more.”
“We have used it for hardening bearing surfaces, cutting tools, dimensional build-ups, and wear surfaces, just to name a few. It is a great money and time saving device.”
“Before we purchased the Rocklinizer and had to service our press brake, it would take us 4.5 days from start to finish to put the machine back in service. Using the Rocklinizer we can build up the shaft in the bearing area... we can have the machine back in operation in 4.5 hours.”
“We were having particular trouble with a wipe down block getting galled up on one of our tools...We then applied the Tungsten Carbide coating with the Rocklinizer and haven’t touched the block in over a year.”
“We are treating cutting edges on paper cutting knives that make over 1 million cuts per day and have increased the time between sharpening 400 to 600%.”
“We have found that Rocklinizing prior to a production run eliminates soldering at gates and vents and the die cavity where molten metal has a tendency to solder to the cavity.”
“Since we can control the amount of deposit exactly, we have been able to resize dies and bearing shafts.”
This is just a small sample of the time and money that can be saved with the Rocklinizer Carbide Application Equipment. For more applications and customer examples, visit www.rocklinizer.com
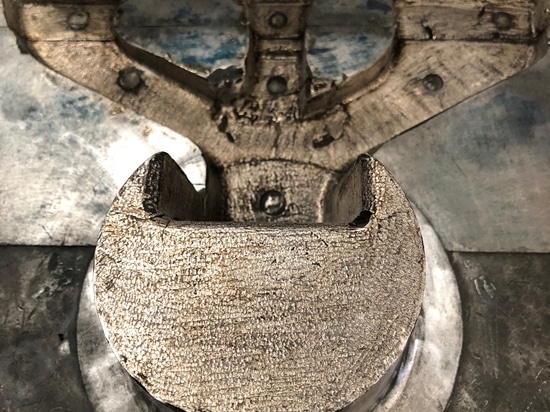
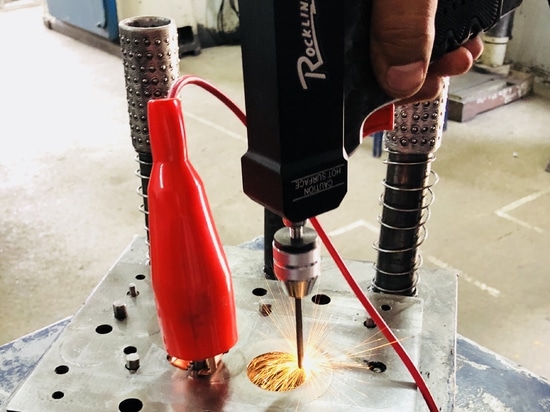
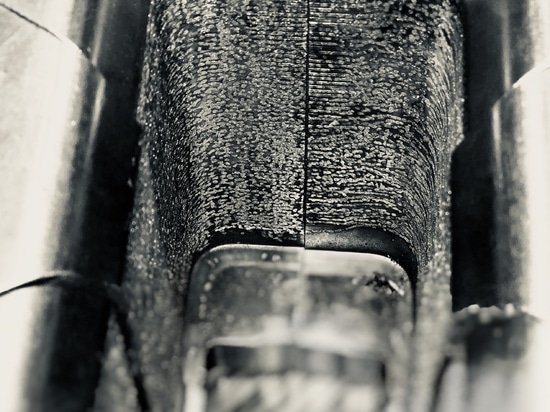