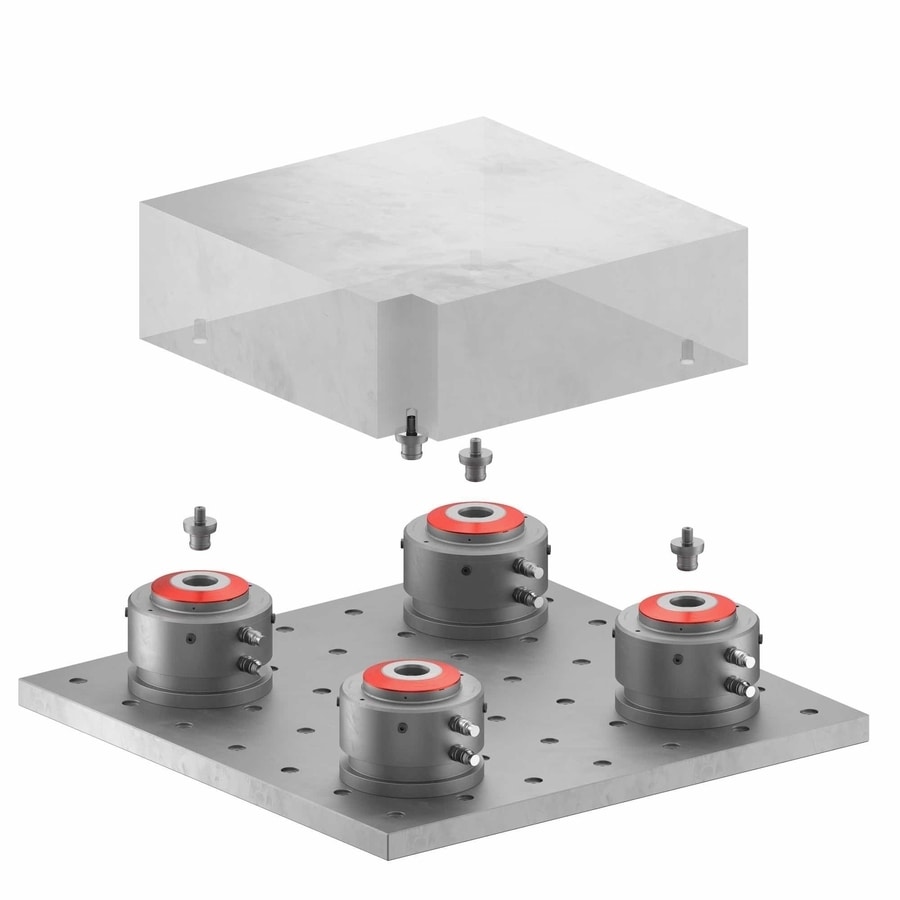
#Trade Shows & Events
ROEMHELD at the AMB: Workpiece clamping technology with sensors for digitization, automation and flexibility
Premieres: swing clamps with integrated pneumatic query, HILMA.ASH automation system and "balance" clamping systems for distortion-free clamping of workpieces.
Laubach, July 14th, 2022. Workpiece clamping technology with sensors for efficient production is the focus at ROEMHELD at the AMB from September 13th to 17th in Stuttgart. The clamping technology specialist offers a growing number of workpiece clamping elements and systems for digitizing, automating and making clamping and set-up processes more flexible. With them, forces, paths and pressures and other parameters for the manufacturing process can be recorded and processed. A number of other components from the ROEMHELD portfolio have electronic or pneumatic control options that provide information about the respective clamping status.
The premieres at this year's trade fair include ROEMHELD swing clamps for low operating pressures, the HILMA.ASH automation system and new "balance" clamping systems for distortion-free clamping of workpieces. All innovations, an overview of the large range of clamping technology and a selection of customer-specific clamping solutions will be presented by ROEMHELD in Hall 1 at Stand 1H70.
New series: hydraulic swing clamp with pneumatic position control for 70 and 120 bar
A new series of hydraulic swing clamps, based on the well-known 70 and 120 bar series, has an integrated pneumatic position control. Due to its compact design, the outer geometry is identical to the version without control.
They are mainly used in fully automatic production with very short cycle times and in clamping devices where handling systems are used to change workpieces.
Automation clamping system HILMA.ASH for automated production
The HILMA.ASH hydraulic double-acting long-stroke clamp presented for the first time is characterized by a very large stroke of 80 mm. It is ideal for different sizes of families of parts that are clamped in a clamping system. Therefore, the number of workpiece-specific clamping devices can be significantly reduced and clamping device costs can be saved. Another advantage: The machine running time is not limited by the number of clamping devices and pallets.
The large stroke offers sufficient flexibility for the fully automated production of workpieces for the first and second clamping. An automated jaw change is also possible. This means that raw parts and semi-finished products can be alternately clamped and machined with different clamping forces without any manual intervention.
In cooperation with a robot, the HILMA.ASH replaces a large number of conventional clamping systems, which often only have a stroke of a few millimeters and therefore only offer little flexibility.
Parts families can be manufactured with the HILMA.ASH much more cheaply than with standard vices or pallet systems thanks to shorter set-up times and lower personnel and system costs.
New "balance" clamping systems for distortion-free clamping of workpieces
The HILMA MC-P machine vice with balance function and the hydraulic single-acting STARK.balance zero-point clamping system adapt to the workpiece. This allows you to position and clamp it without distortion. This balancing function prevents deformation of the workpieces, so that precise and process-reliable production is guaranteed at all times.
The STARK.balance quick release fastener enables a very large compensation of ± 0.75 mm. It was specially developed for the special requirements of direct clamping and large pallets.
If the workpiece changes, for example as a result of temperature fluctuations, the clamping mechanism can move sideways. This allows position errors of up to 1.5 mm to be compensated.
Due to the collision-free accessibility on five sides, STARK.balance systems are also ideal for 5-axis machining and for the flexible production of different component dimensions.
Clamping with integrated sensors, active retraction and compensation: STARK.connect
System-related inaccuracies can also be included in the STARK.connect exhibited at the AMB. Its integrated sensors indicate the various clamping states "clamped without retractable nipple", "retractable nipple clamped" and "released" using LEDs on the element. In addition, the information is forwarded to a PLC control via PNP outputs.
STARK.connect has an active infeed that noticeably improves the clamping quality. Other systems with active feeding such as STARK.classic, STARK.hydratec and STARK.sweeper can also be seen at the booth.