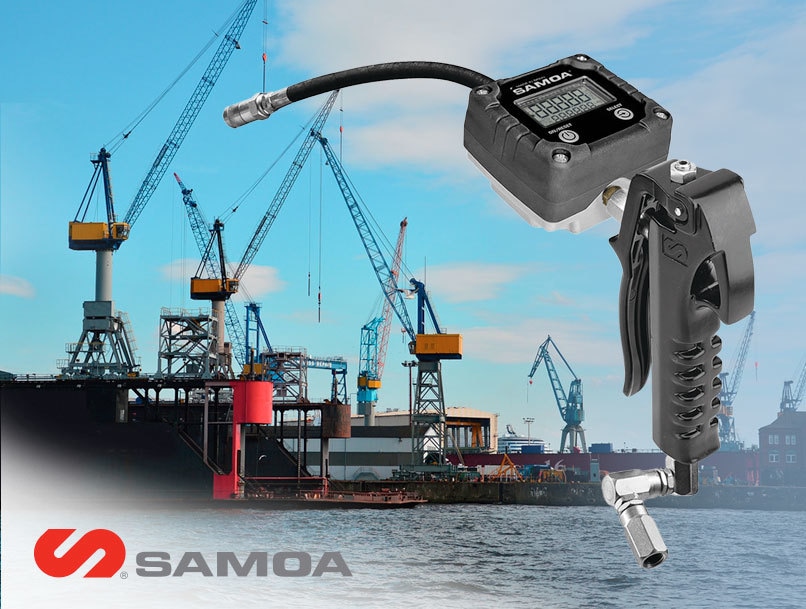
#Industry News
Why use volume flow meters to improve productivity?
What is a flow meter?
A volume flow meter is a device, usually made of metal or plastic material, specifically designed to measure and display the volume of fluid passing through its measuring chamber. It may be installed in-line with the system piping or directly on a dispensing gun.
Volume flow meters are usually classified by fluid inlet/outlet connections size, manufacturing material, the flow rate range, and the maximum operating pressure.
Volume flow meters are suitable for all types of fluids and applications (vehicle maintenance, industries, etc.). Depending on the application and the fluid being measured, you can choose a meter with a greater or lesser flow range and inlet/outlet connection, thus satisfying any need, if its material is compatible with the fluid to be measured.
Why use a volume flow meter?
Knowing what they are, how they are classified, and what they are used for, they offer several advantages in the operations or production processes where they are used:
Accurate measurement: they are designed to accurately measure the volume of fluid dispensed.
Increased productivity: as they are a reliable measuring system, they facilitate control of the quantity dispensed, allowing less time to be spent on each operation.
Cost optimization: by knowing the precise amount of fluid dispensed, it is possible to avoid waste and minimise unnecessary expenses associated with the extra fluid delivered.
Safety: they can supply the precise amount of fluid required for maintenance and avoid future problems due to insufficient or excessive lubrication. On the other hand, thanks to the meters it is possible to avoid the use of measuring cups, in which the fluid can spill over the work area.
What types of fluids can be measured?
Volume flow meters can measure from the lowest viscosity fluids, such as water-based fluids, to the higher viscous fluids, including lubricating greases.
There is an important difference between the measurement of low and medium-viscosity fluids and high-viscosity fluids. The former is measured in volume units, while the latter is measured in mass units.
High viscosity fluids such as grease are difficult to measure. Water and oil-based fluids can be measured with an accuracy of 0.5 %, while greases have an accuracy of 2 to 3 %.
In which applications and industries is grease applied?
Grease, a vital component in a wide range of industries, is a semi-solid lubricant composed of oil, thickener and additives. Characterized by its ability to reduce friction, protect surfaces and improve machinery performance, grease has numerous applications in different industries, providing benefits in each one of them.
Automotive industry:
It relies heavily on grease to ensure the smooth operation and longevity of numerous components. Grease provides a protective film that reduces wear and friction and helps withstand common heavy loads, shocks and vibrations in vehicles.
Construction industry and heavy-duty machinery:
Grease is vital for the proper functioning of various components. It is used in excavators, cranes, loaders and other construction machinery. It helps lubricate pins, bushings, guides and hydraulic systems, ensuring smooth operation, preventing corrosion, and extending equipment life.
Manufacturing and machinery:
Grease plays a key role in machinery and equipment operating in demanding environments. It is used to minimise friction, reduce noise, and prevent wear. Grease also protects against contaminants and extends machinery life, resulting in higher productivity and less downtime.
Marine industry:
Grease is widely used, where equipment and machinery are exposed to hostile saltwater environments. It is used in marine engines, horns, propellers, winches and deck machinery. The grease offers corrosion resistance, water resistance and high load carrying capacity, ensuring reliable lubrication and protection against harsh marine conditions.
Power generation:
This industry relies on grease to ensure efficient and reliable operation of turbines, generators and other equipment. Grease is used to minimize friction, reduce heat generation, and improve performance. It also provides protection against moisture, contaminants and oxidation, helping to extend equipment life.
Aerospace industry:
The grease is indispensable for critical applications that require reliable lubrication under extreme conditions. It is used in aircraft engines, landing gear, actuators, and control systems. Grease helps maintain smooth motion, prevent corrosion and withstand the high temperatures and pressures encountered during flight.
The question we must ask ourselves is… Why is it important to measure high viscosity greases?
Considering the aforementioned, and since greases are not applied in such large quantities as oils, they are mostly dispensed “by eye”, which leads to worse control and its consequences. Therefore, grease metering is important for several reasons:
Optimal maintenance: precise application of the required amount ensures proper lubrication, avoiding possible damage or malfunctions.
Component longevity: the precise amount of grease provides optimum protection of equipment, minimises friction between components and regulates temperature, extending its longevity and therefore the longevity of the equipment itself.
Increased performance and efficiency: by metering and applying the correct grease amount, equipment can run smoothly, reducing friction losses. This contributes to optimum performance and fuel efficiency.
Cost management: greases can be expensive, and knowing the quantity supplied avoids wasting grease and thus minimises and controls the costs of purchase.
Overall, accurate metering and application of high viscosity lubricating greases are crucial to ensuring equipment quality and performance, managing costs, protecting equipment, extending equipment life, and improving maintenance in a variety of industrial applications.
MEET OUR NEW ELECTRONIC GREASE METER!