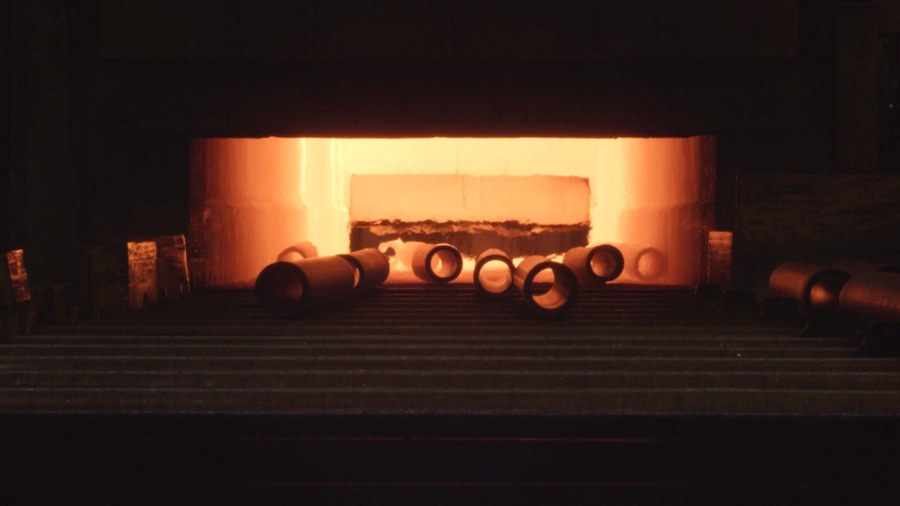
#Industry News
Dry Rolls made by S+C
Sustainability in industrial furnace construction as an economic opportunity
Components made of heat-resistant stainless steel and nickel-based alloys are utilized for decades in the industrial furnace construction. Increasing requirements on product quality and productivity often require very high process temperatures. On one hand, this promotes wear and, on the other hand, solutions on the plant technology, such as internal water cooling of furnace rollers, which results in heavy heat losses. These losses have to be re-heated with fossil energy, which causes high energy costs and at the same time emits large quantities of the environmentally harmful CO2 gas, the saving of which represents the greatest environmental challenge of our time but can also offer companies great advantages.
At many companies the investment in heat resistant steel components for industrial furnace construction is today still dominated by the classic methods of product and supplier selection. Materials and solutions proven in the past are often used when equipping existing furnaces. This conservative method, coupled with the current high cost pressure, can prevent opportunities to convert own furnaces for a more sustainable operation. Ecological issues do not necessarily have to lead to disadvantageous technical and economic solutions. On the contrary, today it is possible to develop practical solutions that offer furnace operators important advantages, such as described in the following example:
Following in-depth consultation by S+C, a customer who previously used water-cooled furnace rollers in their furnace changed over to uncooled furnace rollers made from Centralloy® 60 HT R, a patented special alloy of S+C, developed for operating temperatures of up to 1250° C (2282° F). The higher procurement costs compared with the usual water-cooled rollers were offset by lower operating costs and other advantages. Changing over to “dry” furnace rollers reduced the energy consumption and therefore the energy costs by up to 35% annually. Taking as a basis the entire plant (capacity 4 million tones/year) and taking into account the longer service live of dry rollers, savings of between 1.8 and 2.5 million US$ are achieved per year. The lower energy input and the lower raw material requirement, for manufacturing the rollers, have another advantage: Both protect the environment, something that is of increasing importance to companies pursuing sustainability.
The optimization of heat-resistant components in terms of service life and sustainability are among the main topics when equipping new and existing furnaces. Important aspects of S+C’s consultation are operating temperatures, furnace atmospheres, heating, heating curves, product quality, service life expectations, material selection, etc. It’s worth mentioning that S+C is certified according to ISO 50001: 2018 for energy management systems. This also identifies and leverages potential energy savings in the manufacturing plant, all in the sense of a more sustainable production which includes recycling: Customers can offer S+C their scrapped high-grade steel components so that they can be returned directly to the material cycle.
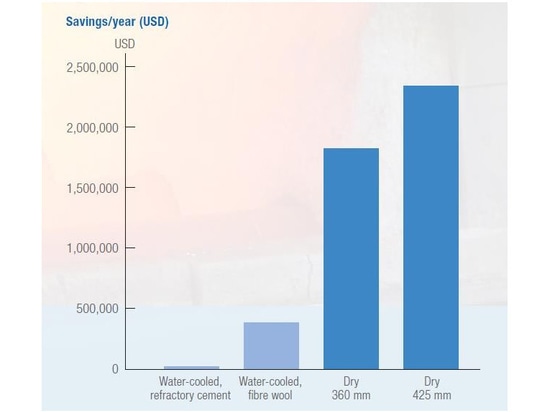