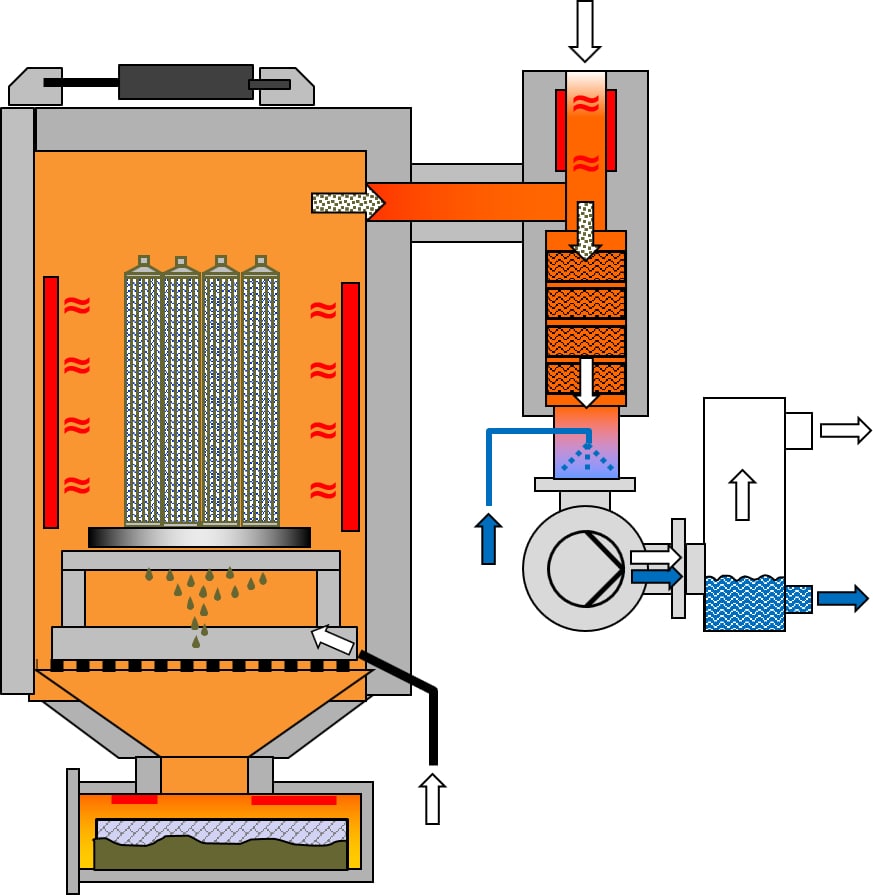
#Product Trends
Thermal cleaning of filter bundles for the packaging industry
SCHWING Technologies is an international specialist for environmentally friendly and cost-effective plastic removal from filters used in flat film production
The cleanliness of filter bundles and filter candles is essential when it comes to quality of the film. The packaging industry used to replace these filters, but today, they are often cleaned for reuse. Why? Depending on the degree of filtration, investments of roughly 600 Euro per filter candle are not uncommon. Cleaning in a VACUCLEAN vacuum pyrolysis system and other post-treatment equipment for reuse, on the other hand, is much cheaper. Systems gently remove all plastic residues from very fine filters. With regular cleaning, filter quality is guaranteed for best production results. Materials such as BOPP, BOPET and BOPA can be removed.
Complete cleaning shops
SCHWING Technologies, based in Neukirchen-Vluyn in the Lower Rhine region of Germany, is an expert for environmentally friendly and safe cleaning of machine tooling. The German company has offered systems to the industry for 50 years and is the only supplier worldwide for complete and customized cleaning equipment solutions. "We always tailor the cleaning shops very individually to the needs of our customers", says Virgilio Perez Guembe, Head of Sales at SCHWING, "with many years of know-how we guarantee maximum cleanliness - without any damage to the filters."
Worldwide sales and testing at the company headquarters
SCHWING sells its complete process solutions worldwide. The company also provides cleaning services in Germany and invites customers to test the cleaning processes at its headquarters in Neukirchen-Vluyn. "We are constantly developing our equipment to achieve optimum results", explains Perez Guembe,"and we are tailoring our cleaning processes to new material mixtures and metal filter designs.”
Individually tailored cleaning process
The cleaning process includes several individually tailored steps, the parameters of which are optimally adjusted: These include first cleaning in a VACUCLEAN vacuum pyrolysis system, post-cleaning processes and final checks.
Safe and gentle vacuum pyrolysis
Workflow of the cleaning process starts with disassembly of the filter bundle. "Then, we carry out the melting process in our VACUCLEAN vacuum pyrolysis system”, explains Perez Guembe. The experienced expert considers all cleaning factors, such as the positioning of the filter bundle, heating time, temperatures and duration of pyrolysis and oxidation. "Even the highest qualities can be cleaned with this system. In a very gentle way, we thermally melt and decompose organic material from temperature-resistant metals."
The fully automatic cleaning process of the VACUCLEAN takes place in an electrically heated vacuum cleaning chamber. Temperature of the filter bundle is measured directly, which is heated particularly slowly and gently. Here, a large percentage of adhering plastic melts off and flows out. At approximately 450 degrees Celsius, the decomposition of the remaining plastic takes place – remaining carbon is finally removed by introducing air (oxidation). An intelligent sensor system controls the oxidation process, so excess temperatures do not occur at any time.
Individualized post-treatment
The experts at SCHWING also offer tailor-made solutions for post-treatment. "Although the thermal cleaning systems remove all organic impurities, inorganic residues, such as residual ash, remain in the filter bundles", explains Perez Guembe. "Special post-treatment methods can remove these absolutely safely.” Post-treatment is always carefully matched to the individual filters and cleaning processes of the customer. Some solutions used are high-pressure water cleaning devices and an ultrasonic bath.
High-pressure post-cleaning and disassembly of the filter bundles
Manual high-pressure post-cleaning processes with water are suitable for removing further residues. The mechanisms for this are temperature and water pressure. Perez Guembe: "During the next step, filter bundles are broken down into individual candles and treated in a backwashing system in the form of back flushing and pressure. In this step, inorganic residues are removed from the inside and outside. Important parameters here are pressure and temperature of the flushing.
Ultrasonic bath, rinsing and drying
In the ultrasonic bath and with subsequent rinsing, the ultra-fine and sensitive filter candles are freed from further residual contamination, especially in difficult-to-access areas. In this step, SCHWING recommends that a number of specifications be taken into account – temperature, type of liquid, additives, filter position, ultrasonic frequency and cleaning time. The filters are then dried in a drying oven. Essential key data is temperature, position of the filter cartridges and drying time.
Inspection and documentation
Bubble tests document whether a filter candle is faultless or mechanically damaged, and a liter per minute (LPM) flow test also verifies the result. Characteristic parameters are liquid (water or isopropanol), test medium and test pressure. In the case of water, a new test is carried out in a drying oven; in the case of isopropanol, in an evaporation fixation. A final weight check confirms perfect cleaning of the filter cartridge.
Environmentally and user-friendly solution
The entire cleaning line is environmentally friendly, has low operating costs and is powered by only electricity and water. It is easy to install and can be quickly trained by SCHWING service team. Perez Guembe explains, "Another advantage for our customers in the packaging industry is that the service life of filter candles and filter bundles is significantly increased and systems can be operated under less pressure. This ensures not only the filter quality, but also the film quality in the long-term".
Keywords: Filter candles, Filter bundles, Filter cleaning, Plastic removal, VACUCLEAN, Vacuum pyrolysis system, Vacuum pyrolysis plant, Vacuum pyrolysis furnace, Thermal cleaning