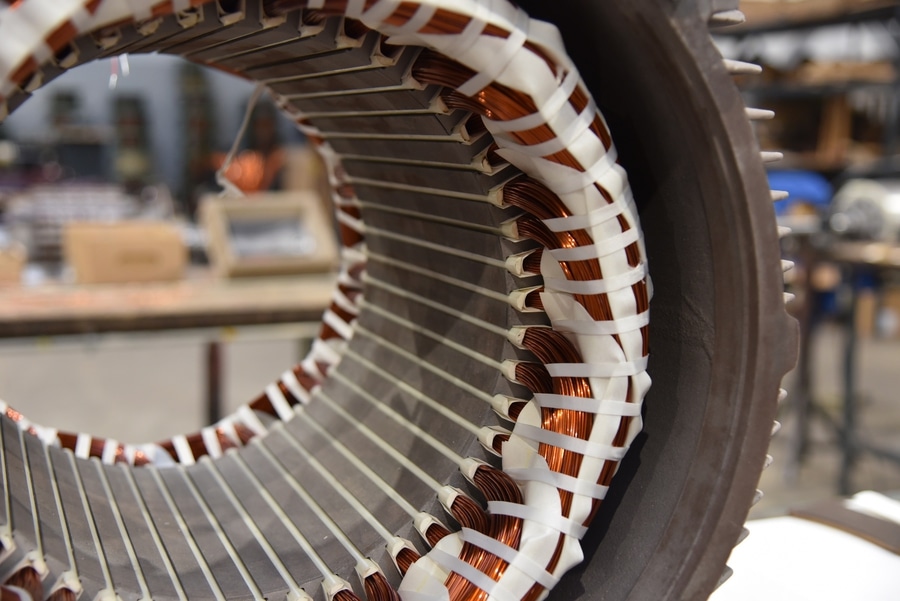
#Industry News
Pyrolysis systems from SCHWING Technologies clean electric motors and generators before repair
Thermal removal of resin and varnish from copper coils using 24/7 cleaning service
Electric motors ensure the reliable drive of many devices, machines, vehicles and plants. Electricity flows through copper conductor coils, which must first be freed of resin and paint layers in order to be recovered for maintenance or repair work. SCHWING Technologies is an expert in this type of thermal removal of resins and lacquer coatings. The company cleans electric motors, generators, stators, and other parts in large pyrolysis systems. Through thermal oxidation, the large MAXICLEAN systems remove all adherent resin and paint layers gently and effectively. "This is the fastest and most efficient method, removing all grease and other adherents without any residue", knows Viktor Brandner, coordinator of the service division of SCHWING. As a 24/7 service, the company cleans parts at its location in Neukirchen-Vluyn on the Lower Rhine and supplements its service with the corresponding logistics.
Cleaning service for electric motors for recycling
For more than 15 years the Duisburg-based repair company Bornemann GmbH has also been using these services. "Inspect, repair and replace" is the motto of this medium-sized company. Founded in 1968, Bornemann specializes in the maintenance, repair and overhaul of DC and three-phase motors, generators and pumps. "We always provide aid when repairs have to be carried out quickly in the event of damage," reports Managing Director Lars Bornemann and underlines: "Production downtimes are expensive – we want to keep them as short as possible." The company regularly delivers electric motors for cleaning to Neukirchen-Vluyn, approximately 15 kilometers away. Lars Bornemann knows from many years of experience that using the cleaning service is the simplest and safest way to remove paint from coils and protecting the expensive motors. In addition, the preparation of the cleaned stators and rotors for rewinding is much easier and has a higher quality, since there are no residues of old insulation and impregnation agents to be removed. He sees a further advantage in relieving employees of the heavy labor of conventional, physical removal of defective windings. "Since time is money, we appreciate the cleaning service from SCHWING", he concludes.
Safe, gentle and short cleaning process
Depending on component size, the pyrolysis systems from SCHWING remove all organic coatings in just one operation. The process takes about eight to ten hours and uses a temperature of about 400 degrees Celsius. Inorganic residues can be dissolved by means of a short post-treatment. "This cleaning process can be precisely controlled, and it can be reproduced at any time," emphasizes SCHWING expert Brandner and adds: "We use an externally gas-heated cleaning chamber for this purpose. There, a special hot air duct ensures optimal temperature distribution and guarantees the shortest possible cleaning time". The fully automatic cleaning process runs completely unattended and not only saves manpower, but also accelerates further production processes. SCHWING cleans at the company site in the Lower Rhine region and sells its thermal cleaning systems worldwide.
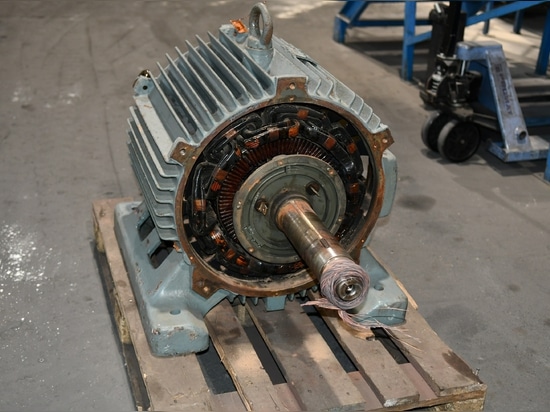