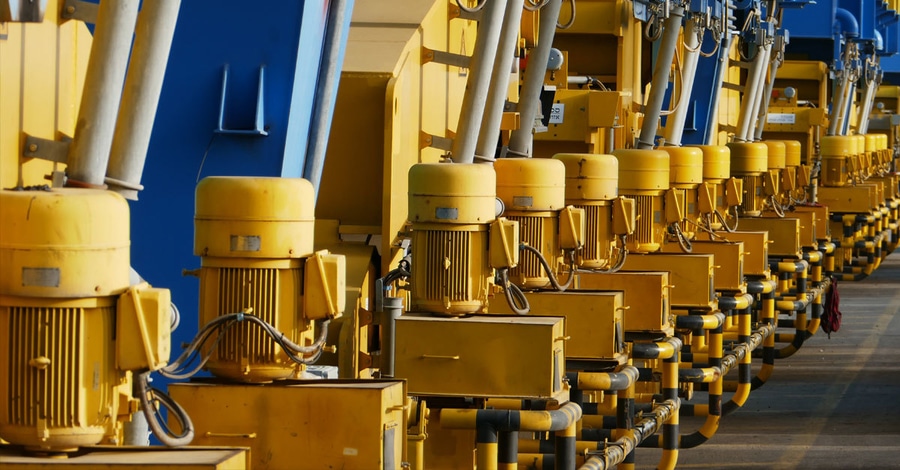
#Product Trends
Long gone are the days of time-based lubrication
Lubrication management is a cornerstone of industrial maintenance, encompassing a range of tasks far beyond the simple application of oil or grease to machines.
It involves meticulous selection of lubricants, proper storage and filtration, vigilant monitoring of bearing health, and prevention of over- and under-lubrication.
In the pursuit of operational excellence, the importance of effective lubrication supervision cannot be overstated. Fortunately, thanks to technological advances, new lubrication management tools have emerged, promising greater efficiency and reliability.
One of the most pressing challenges in lubrication management is over-lubrication, recognized by many experts as a ubiquitous problem in industrial plants worldwide. The consequences of excessive grease application are disastrous: heat generation, agitation and, ultimately, solidification, leading to clogging of the fresh lubricant and, with no surprise, bearing failure. Bearing failures, mainly due to lubrication problems, lead to unplanned downtime, hampering production and incurring significant costs. Clearly, meticulous lubrication practices are essential to the smooth running of industrial operations.
Conventional approaches to lubrication, while seemingly logical, are often unreliable. Many technicians still adhere to time-based, preventive lubrication methods, administering grease at regular intervals. While this strategy aims to limit under-lubrication and the resulting malfunctions, it often overlooks the risks associated with over-lubrication, which can accelerate bearing deterioration.
But the days of relying solely on time-based calculations can now be a thing of the past. With the LUBExpert ON-GUARD, precision and accuracy become the keywords for an effective lubrication strategy. This revolutionary device functions as a virtual “nutritionist” for machines, developing personalized, autonomous, data-driven maintenance plans that preventively address potential problems.
Imagine the peace of mind knowing that you no longer need to constantly visit each machine to ensure proper lubrication. With the LUBExpert ON-GUARD, the intricate task of bearing grease replenishment is seamlessly managed, eliminating the need for manual intervention. This not only reduces workload and minimizes grease waste but also guarantees optimal machine performance.
But what makes this device a real added value that can change the whole of a plant’s practices, is that its benefits are not limited to individual machines. It’s actually a versatile solution capable of transforming entire plants and lubrication programs, instilling a culture of reliability and efficiency.
Indeed, the LUBExpert ON-GUARD serves as a comprehensive solution for your entire plant and lubrication program. By automating lubrication tasks with precision, thanks to the SDT LUBrain’s advanced algorithm, the device ensures that every machine receives the right amount of grease precisely when needed.
The idea is not to improve the performance of individual machines. Rather, it’s about revolutionizing your entire approach to maintenance. Implementing the LUBExpert ON-GUARD solution means a change of culture and methodology. No longer bound by traditional time-based practices, you’ll be able to take condition monitoring and lubrication strategies to the next level.
In other words, it’s not just another set of components assembled and installed on machines. The LUBExpert ON-GUARD represents a complete solution to combat poor lubrication practices and promote reliability in your operations.
It’s an all-in-one package designed to establish new quality practices, where precision, efficiency and reliability come together to deliver unrivalled performance. With the LUBExpert ON-GUARD, you don’t just modernize your machines, you can transform your entire operation.