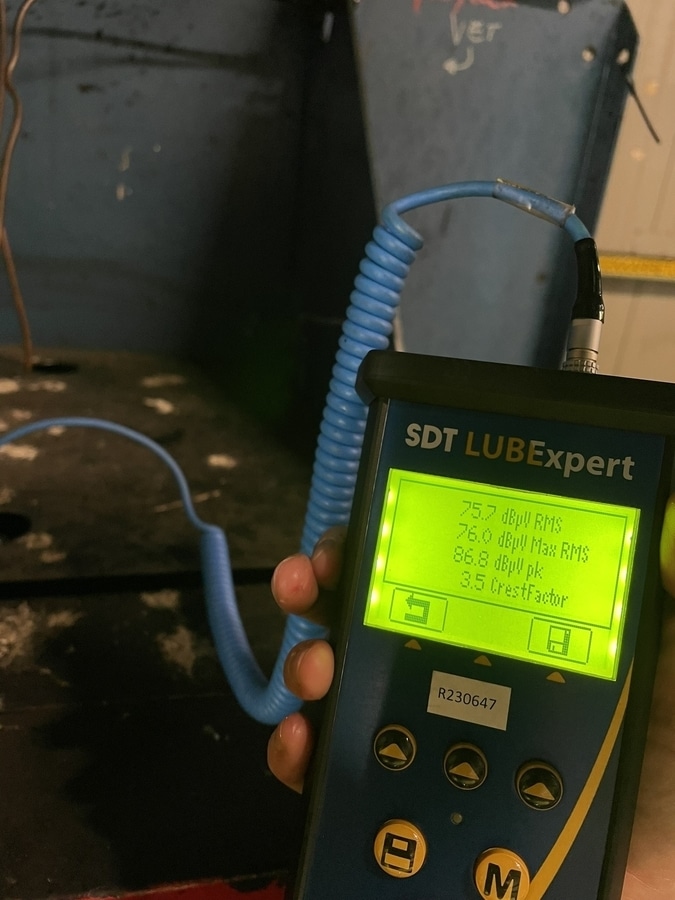
#Product Trends
Lubrication Using Ultrasound: A Pragmatic Way to Determine the Correct Amount of Grease
Proper lubrication is critical for the efficient and reliable operation of machinery.
Traditionally, maintenance schedules are based on operating hours, with lubricants applied at regular intervals. While logical, this approach does not account for dynamic factors such as load variations, environmental conditions, and temperature changes. To prevent over- or under-lubrication, which can lead to increased friction and wear, ultrasound equipment offers a more precise solution. By using ultrasound measurements, maintenance teams can accurately determine when and how much grease to apply, ensuring optimal machine performance.
One of the most advanced tools available for this purpose is the LUBExpert, a device specifically designed to streamline lubrication processes through precise ultrasound analysis.
The challenge of traditional lubrication methods
In industrial applications, lubrication maintenance aims to minimize friction and effectively remove heat and contaminants. Companies typically follow schedules that specify which components need lubrication and when. These schedules are often based on fixed intervals, such as weekly, monthly, or bi-annually. However, this static approach does not account for varying operational conditions.
A more dynamic method involves lubrication based on operating hours, which helps prevent premature lubrication for irregularly used machines. Visual and auditory inspections are also common, but these methods do not adequately address changing lubrication needs due to factors like machine overload or temperature fluctuations. Such conditions can lead to under-lubrication, causing increased friction, higher energy consumption, noise levels, and shorter component lifespans.
The ultrasound solutions
Traditionally, maintenance schedules are based on operating hours, with lubricants applied at regular intervals. While logical, this approach does not account for dynamic factors such as load variations, environmental conditions, and temperature changes. To prevent over- or under-lubrication, which can lead to increased friction and wear, ultrasound equipment offers a more precise solution. By using ultrasound measurements, maintenance teams can accurately determine when and how much grease to apply, ensuring optimal machine performance.
One of the most advanced tools available for this purpose is the LUBExpert, a device specifically designed to streamline lubrication processes through precise ultrasound analysis.
Practical applications of the LUBExpert in ultrasound lubrication
Baseline Measurements
To implement ultrasound lubrication effectively, companies must first perform reference measurements on properly lubricated bearings. These baseline values serve as benchmarks for future assessments. The LUBExpert excels in capturing these baselines with high precision.
Regular Monitoring
Using the LUBExpert, technicians can regularly monitor bearings for deviations from the reference measurements. When the device detects amplitude increases above a certain threshold (typically around 8 dB), it signals the need for lubrication. This method helps schedule maintenance actions precisely when needed, avoiding both over- and under-lubrication.
Optimized Lubricant Application
During lubrication, the LUBExpert measures noise levels in real-time, guiding technicians to add grease until the optimal decibel value is reached. This feedback mechanism prevents over-lubrication, which can cause increased friction and unnecessary grease usage. If noise levels rise due to excess grease, the LUBExpert alerts the technician to stop and clean the bearing.
Advantages of using the LUBExpert
Precision and Reliability
The LUBExpert’s advanced technology provides precise and reliable measurements, allowing for accurate lubrication. Its ability to isolate high-frequency sounds ensures that measurements are not contaminated by background noise, a common issue in industrial environments.
User-Friendly Interface
The LUBExpert is designed with ease of use in mind, requiring minimal training. Its intuitive interface and clear displays make it accessible for maintenance teams, even those with demanding schedules.
Real-Time Data and Trend Analysis
The LUBExpert supports real-time measurements and can store large volumes of data for trend analysis. This feature allows maintenance teams to track historical lubrication activities and make data-driven decisions, enhancing maintenance planning and efficiency.
Implementing the solution
When integrating the LUBExpert into lubrication practices, it is advisable to partner with SDT for comprehensive support and training. This ensures the technology is effectively utilized from the outset, maximizing its benefits.
Recording lubrication activities, including dates and grease quantities, is crucial. The UAS3 software facilitates this by allowing easy data entry and retrieval, ensuring accurate tracking and analysis. This practice helps determine the optimal amount of grease for each bearing, avoiding both premature and delayed lubrication.
By fine-tuning lubrication intervals based on ultrasound measurements from the LUBExpert, companies can reduce labor hours and lubricant usage, leading to cost savings. More frequent lubrication, if needed, prevents unnecessary friction, prolonging component lifespans and reducing energy consumption.
The LUBExpert represents a significant advancement in maintenance technology, offering precise and reliable measurements that traditional methods cannot match. By adopting the LUBExpert, companies can ensure their machinery operates efficiently and reliably, reducing downtime and maintenance costs. As the technology continues to evolve, it promises even greater benefits for industrial maintenance, making it an essential tool for any maintenance department. With the LUBExpert, the future of lubrication maintenance is not only precise but also exceptionally efficient.