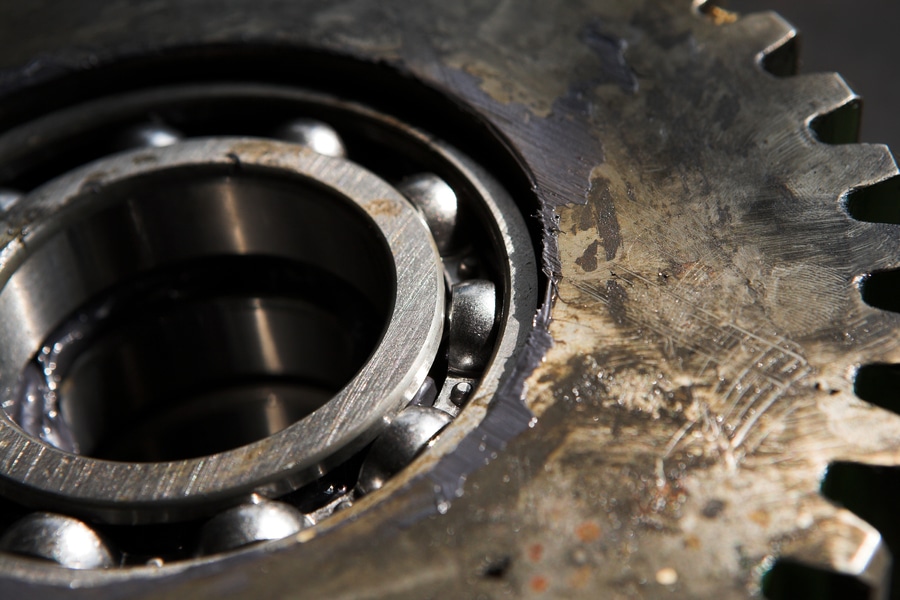
#Product Trends
Detecting Mechanical Condition Issues with the SDT340: A Key to Proactive Maintenance
Mechanical condition monitoring is an essential part of maintaining industrial equipment, and the SDT340 ultrasound device stands at the forefront of this technology.
Monitoring the health of mechanical components like bearings allows industries to detect early signs of wear and tear before they turn into catastrophic failures. This proactive approach minimizes unscheduled downtime, increases operational efficiency, and significantly reduces maintenance costs.
The importance of bearings in industrial applications
Bearings are pivotal in countless industrial machines, from turbines to pumps and motors. A single bearing failure, if not detected early, can cause extensive damage, leading to unplanned shutdowns and significant financial loss. In extreme cases, undetected failures can result in catastrophic damage, posing risks to both equipment and personnel.
For high-speed bearings, maintenance programs commonly rely on techniques like vibration analysis, temperature monitoring, and even wear debris analysis to track their health. However, these methods have limitations, especially for low-speed bearings operating below 250 rpm. This is where traditional techniques fall short, and ultrasound technology like that offered by the SDT340 shines.
What ultrasound brings to the table
Ultrasound is a powerful way of detecting mechanical issues that are otherwise invisible to traditional methods. The SDT340 detects and measures high-frequency acoustic waves generated by bearing impacts, friction, and poor lubrication. These high frequencies are especially useful in low-speed applications where vibrations are minimal, and early warning signs might be missed.
The SDT340’s ability to detect localized energy released by the impact of bearing damage sets it apart. It converts these ultrasonic signals into audible sounds through a process known as heterodyning, making it easier for technicians to recognize and interpret issues before they escalate.
Why ultrasound for mechanical condition monitoring?
The benefits of ultrasound for condition monitoring can be summarized in two main advantages:
Sensitivity to High-Frequency Signals: Ultrasound focuses on high-frequency impacts, making it ideal for detecting weak signals from low-speed bearings that might not generate strong vibrations.
Detection of Shock Waves: Ultrasound identifies the shock waves from bearing defects, enabling early detection even in machinery operating at slow speeds. This is crucial for spotting problems before they cause larger, more expensive issues.
For example, when a bearing begins to degrade, the friction it generates can be detected by the SDT340’s sensor long before the failure manifests through vibration or temperature changes. Ultrasound’s selectivity also helps to isolate these problems from background noise, ensuring accurate and reliable detection.
Listening: The first line of defense
The primary function of ultrasound in mechanical condition monitoring is to transform high-frequency signals into audible sounds, allowing operators to “listen” for warning signs. Even an inexperienced technician can quickly identify issues such as poor lubrication or bearing defects simply by listening for specific sounds like crackling or grinding.
This simplicity makes the SDT340 accessible to a wide range of users, from new technicians to experienced engineers, enabling quick and effective monitoring without requiring complex signal analysis.
Combining ultrasound and vibration: A dual approach
While ultrasound excels at detecting friction and impact phenomena, it works even better when combined with vibration analysis. The SDT340 integrates both technologies into a single device, offering a versatile tool for complete machine health monitoring. Vibration analysis is particularly useful for identifying issues like misalignment, imbalance, or structural problems that might go undetected by ultrasound alone.
This dual approach is especially valuable in predictive maintenance (PdM) programs where monitoring needs to be both comprehensive and cost-effective. The SDT340 provides a fast, reliable, and straightforward solution for detecting 80% of potential machine failures using static measurements, while dynamic measurements can offer deeper diagnostics when necessary.
Dynamic and static measurements: A comprehensive solution
The SDT340 offers both static and dynamic measurements, allowing for basic monitoring as well as more in-depth diagnostics when necessary. Static measurements, which are quick and easy to perform, give maintenance teams a baseline for trend analysis and condition monitoring. Meanwhile, dynamic measurements provide detailed insights into the root cause of mechanical issues, offering advanced analysis when further investigation is required.
With ultrasound technology, time-domain representation is particularly useful for identifying repeated shocks and pinpointing the exact cause of a failure. This level of detail is essential for ensuring that maintenance is targeted and effective, ultimately extending the lifespan of critical equipment.
Cost-effective maintenance: Save time and resources
In today’s industrial landscape, maintenance teams are under increasing pressure to optimize production while keeping costs low. The SDT340 excels in this environment by providing fast, accurate condition monitoring that reduces unnecessary data collection and analysis. By focusing on only the 20% of machines that need attention, and resolving 80% of those issues quickly, maintenance teams can simplify their operations and maximize efficiency.
Versatility in a single instrument
The SDT340 is more than just an ultrasound device; it’s a versatile tool capable of addressing multiple maintenance challenges. It’s perfect not only for mechanical condition monitoring but also for energy cost control, leak detection, and even monitoring the health of hydraulic systems, valves, and electrical systems. This broad functionality makes it an invaluable asset for any maintenance team looking to optimize performance and minimize costs.
When it comes to bearing monitoring, the SDT340’s ability to quickly and accurately detect problems like friction, impacts, and lubrication issues means you can address potential failures before they lead to major disruptions.
Conclusion
The SDT340 ultrasound solution is a game-changer in mechanical condition monitoring. Its ability to detect early signs of bearing failure and friction in both high-speed and low-speed applications makes it an essential tool for predictive maintenance programs. By combining ultrasound with vibration analysis, the SDT340 delivers a complete, versatile solution that improves efficiency, reduces costs, and prevents catastrophic equipment failures.
Investing in the SDT340 means investing in the long-term health of your machinery—and the efficiency of your maintenance program. Whether you’re monitoring bearings, detecting compressed air leaks, or inspecting electrical systems, the SDT340 has you covered.